A heat treatment furnace is a specialized piece of equipment designed to alter the physical and sometimes chemical properties of materials, typically metals, through controlled heating and cooling processes. These furnaces operate by creating a controlled environment where materials can be uniformly heated to precise temperatures, held at those temperatures for specific durations, and then cooled at controlled rates. The goal is to achieve desired material properties such as increased hardness, improved strength, or enhanced ductility. Different types of heat treatment furnaces, such as vacuum furnaces, electric arc furnaces, and continuous furnaces, employ unique mechanisms to achieve these results. For example, vacuum furnaces prevent oxidation by operating in a low-pressure environment, while electric arc furnaces use electric arcs to generate intense heat for melting metals. The process often involves advanced features like inert atmospheres to reduce oxidation and automated systems for high-volume production.
Key Points Explained:
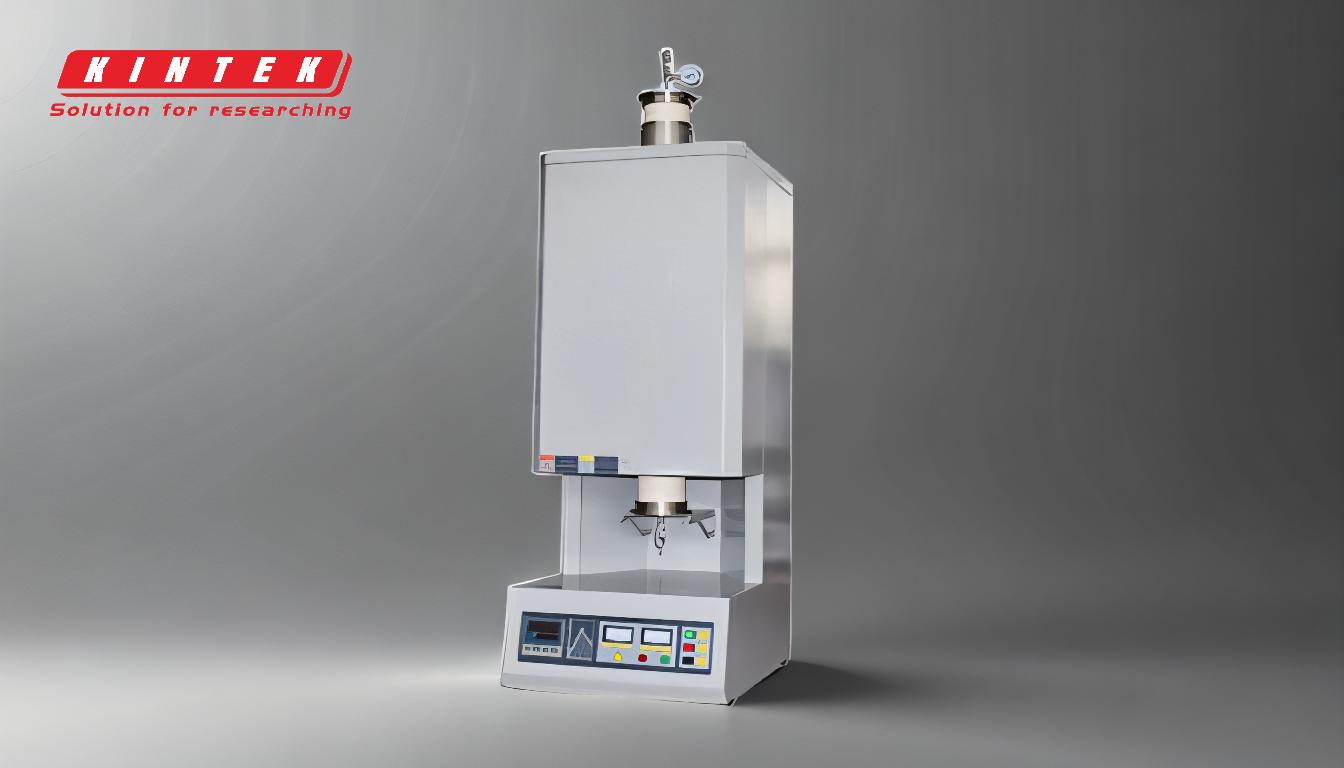
-
Uniform Heating and Temperature Control:
- Heat treatment furnaces are designed to provide uniform heating across the material being treated. This is crucial for achieving consistent material properties throughout the workpiece. Precise temperature control is achieved through advanced controllers that monitor and adjust the furnace environment to maintain the desired temperature.
-
Controlled Cooling Rates:
- After heating, the cooling rate is carefully controlled to achieve specific material properties. Rapid cooling, for instance, can increase hardness, while slower cooling can improve ductility. The furnace's cooling system is designed to manage this process effectively.
-
Types of Heat Treatment Furnaces:
- Vacuum Furnaces: These operate in a low-pressure or vacuum environment to prevent oxidation and contamination. They are ideal for processes like annealing, sintering, and heat treatment where material purity is critical.
- Electric Arc Furnaces: These use electric arcs to generate intense heat, making them suitable for melting metals. The heat is produced by creating an arc between two electrodes.
- Continuous Furnaces: Designed for high-volume production, these furnaces use conveyor belts or other automated systems to move parts through the heating and cooling processes. They are efficient for processing large quantities of identical parts.
-
Inert Atmospheres:
- Inerting involves using gases like nitrogen or argon to create a controlled atmosphere within the furnace. This reduces the risk of oxidation and removes unwanted materials, ensuring the integrity of the heat-treated components.
-
Specialized Furnace Designs:
- Tube Furnaces: These heat samples contained within a work tube. The furnace heats the outside of the tube, which then transfers heat to the samples inside.
- Retort Furnaces: These consist of interconnected chambers, such as a hot chamber and a fast cooling chamber, allowing for precise control over the heating and cooling phases.
-
Applications and Benefits:
- Heat treatment furnaces are used in various industries, including aerospace, automotive, and manufacturing, to enhance material properties. The benefits include improved mechanical properties, increased durability, and the ability to tailor materials for specific applications.
By understanding these key points, a purchaser can make informed decisions about the type of heat treatment furnace that best suits their needs, ensuring optimal results for their specific applications.
Summary Table:
Key Feature | Description |
---|---|
Uniform Heating | Ensures consistent material properties through precise temperature control. |
Controlled Cooling Rates | Adjusts cooling speed to achieve desired hardness or ductility. |
Types of Furnaces | Vacuum, electric arc, and continuous furnaces for specific applications. |
Inert Atmospheres | Uses gases like nitrogen or argon to prevent oxidation and contamination. |
Specialized Designs | Tube and retort furnaces for tailored heating and cooling processes. |
Applications | Used in aerospace, automotive, and manufacturing for enhanced material properties. |
Ready to optimize your material properties? Contact us today to find the perfect heat treatment furnace for your needs!