A VIM (Vacuum Induction Melting) furnace operates by using electromagnetic induction to heat and melt conductive materials within a vacuum environment. The process involves passing a high-frequency electrical current through a copper coil, which generates a fluctuating magnetic field. This field induces eddy currents within the conductive material placed inside the furnace, causing it to heat up due to electrical resistance. The vacuum environment prevents oxidation and contamination, making it ideal for melting high-purity metals and alloys. The temperature is precisely controlled, and the molten material can be poured into molds or used for further processing. This method ensures efficient, uniform heating and is widely used in industries requiring high-quality metal products.
Key Points Explained:
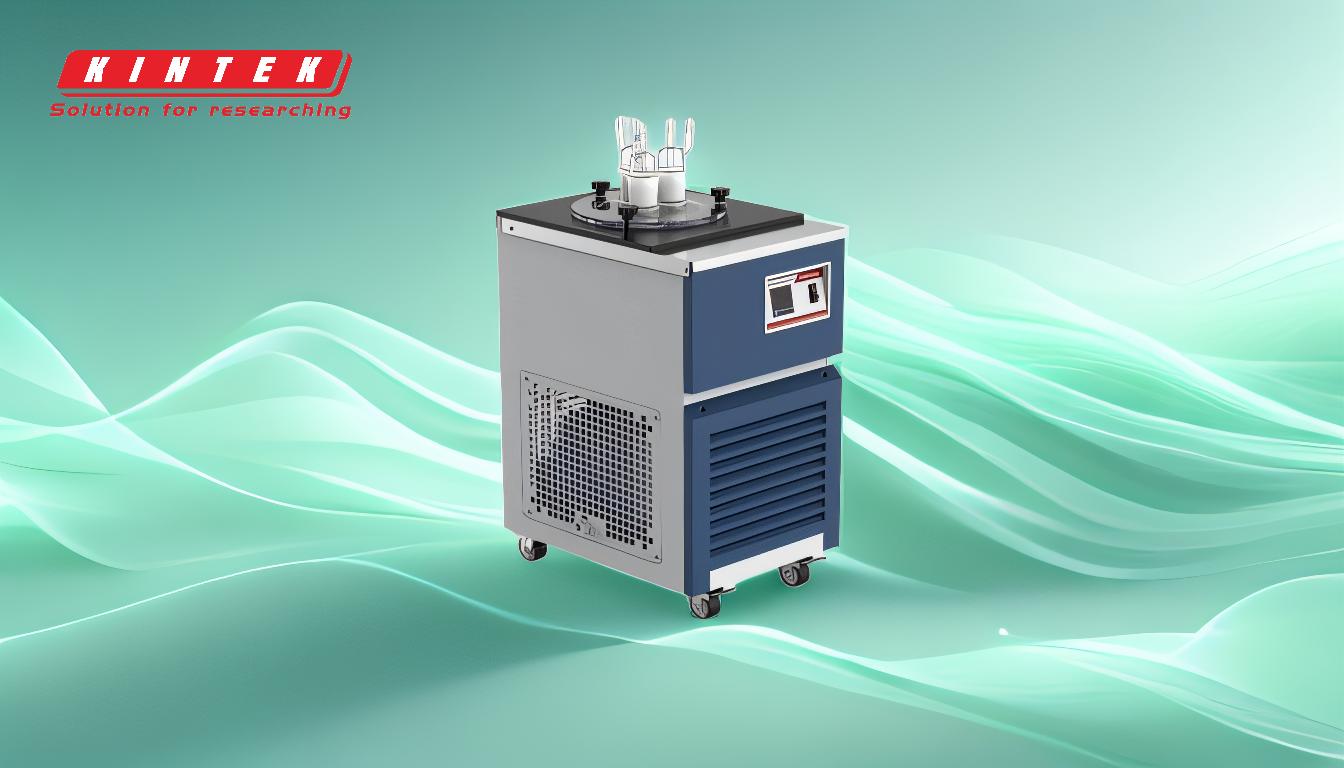
-
Electromagnetic Induction:
- The core principle of a VIM furnace is electromagnetic induction. A high-frequency alternating current is passed through a copper coil, creating a fluctuating magnetic field. This field induces eddy currents within the conductive material placed inside the furnace, generating heat through electrical resistance.
-
Vacuum Environment:
- The furnace operates in a vacuum, which is crucial for preventing oxidation and contamination of the material being melted. This is particularly important for high-purity metals and alloys, where even minor contamination can significantly affect the material's properties.
-
Heating and Melting:
- The induced eddy currents cause the material to heat up rapidly. Once the material reaches its melting point, it becomes molten and can be poured into molds or used for further processing. The temperature is carefully controlled to ensure uniform heating and precise melting.
-
Temperature Control:
- The furnace is equipped with a temperature control system that allows for precise regulation of the heating process. This ensures that the material is heated evenly and reaches the desired temperature without overheating or underheating.
-
Applications:
- VIM furnaces are used in various industries, including aerospace, medical, and electronics, where high-purity metals and alloys are required. The ability to melt materials in a vacuum environment makes it ideal for producing components with stringent quality requirements.
-
Advantages:
- The primary advantages of a VIM furnace include the ability to produce high-purity materials, precise temperature control, and efficient, uniform heating. The vacuum environment also allows for the processing of reactive metals that would otherwise oxidize or react with atmospheric gases.
-
Components:
- Key components of a VIM furnace include the induction coil, crucible, vacuum chamber, and temperature control system. The induction coil generates the magnetic field, the crucible holds the material, the vacuum chamber maintains the low-pressure environment, and the temperature control system ensures precise heating.
By understanding these key points, one can appreciate the sophisticated technology behind VIM furnaces and their critical role in producing high-quality metal products.
Summary Table:
Key Aspect | Details |
---|---|
Principle | Electromagnetic induction heats conductive materials via eddy currents. |
Vacuum Environment | Prevents oxidation and contamination, ideal for high-purity metals. |
Heating Process | Rapid, uniform heating with precise temperature control. |
Applications | Aerospace, medical, and electronics industries for high-quality metal products. |
Advantages | High-purity materials, precise control, and efficient heating. |
Key Components | Induction coil, crucible, vacuum chamber, and temperature control system. |
Interested in high-purity metal melting solutions? Contact us today to learn more about VIM furnaces!