Carbon regeneration, also known as reactivation, is a thermal process designed to restore the adsorption capacity of activated carbon by removing the contaminants adsorbed on its surface. This process involves heating the carbon to high temperatures in a controlled environment, which decomposes and volatilizes the adsorbed substances, leaving the carbon clean and ready for reuse. The regenerated carbon retains its porous structure and adsorption properties, making it a cost-effective and sustainable solution for industries relying on activated carbon for purification and filtration processes.
Key Points Explained:
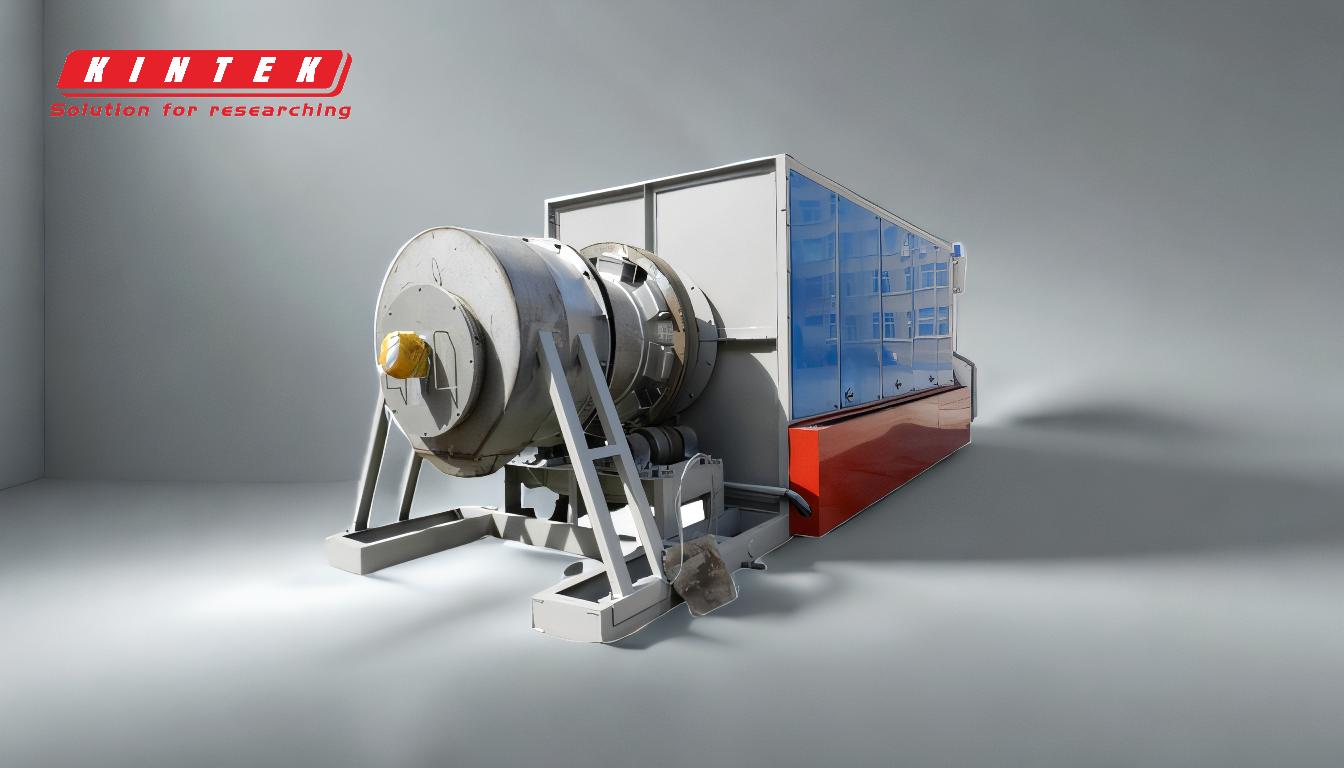
-
Definition and Purpose of Carbon Regeneration:
- Carbon regeneration is a thermal process aimed at restoring the adsorption capacity of activated carbon by removing adsorbed contaminants.
- The primary purpose is to reuse the carbon, reducing costs and minimizing waste, as regenerated carbon can perform similarly to virgin carbon in many applications.
-
Thermal Processing Mechanism:
- The process involves heating the spent carbon to high temperatures (typically 600–900°C) in a controlled environment, such as a rotary kiln or furnace.
- The heat breaks down the adsorbed organic compounds into gases (e.g., carbon dioxide, water vapor) and ash, which are then removed from the carbon surface.
-
Steps in the Regeneration Process:
- Drying: The carbon is first dried to remove moisture, which is essential for efficient thermal processing.
- Thermal Decomposition: The carbon is heated to high temperatures, causing the adsorbed contaminants to decompose and volatilize.
- Activation: In some cases, steam or carbon dioxide is introduced to further clean and reactivate the carbon pores, enhancing adsorption capacity.
- Cooling: The regenerated carbon is cooled before being reused or stored.
-
Types of Regeneration Systems:
- Rotary Kilns: Commonly used for large-scale regeneration, rotary kilns provide consistent heating and are suitable for a wide range of contaminants.
- Multiple Hearth Furnaces: These systems allow for precise temperature control and are often used for specialized applications.
- Fluidized Bed Reactors: These systems offer rapid heating and efficient regeneration but are typically used for smaller-scale operations.
-
Benefits of Carbon Regeneration:
- Cost Savings: Regeneration is significantly cheaper than purchasing new activated carbon, especially for industries with high carbon usage.
- Environmental Sustainability: Reusing carbon reduces waste and the need for raw materials, contributing to a circular economy.
- Performance: Regenerated carbon can achieve adsorption efficiencies close to those of virgin carbon, depending on the regeneration process and the nature of the contaminants.
-
Challenges and Considerations:
- Contaminant Type: Some contaminants, such as heavy metals or inorganic compounds, may not be fully removed through thermal regeneration.
- Carbon Loss: Each regeneration cycle results in a small loss of carbon mass due to oxidation and abrasion, typically around 5–10%.
- Energy Consumption: The process requires significant energy input, which can impact operational costs and environmental footprint.
-
Applications of Regenerated Carbon:
- Water Treatment: Used in municipal and industrial water purification systems to remove organic pollutants, chlorine, and odors.
- Air Purification: Employed in air filters to capture volatile organic compounds (VOCs) and other airborne contaminants.
- Food and Beverage Industry: Utilized for decolorization, deodorization, and purification processes.
-
Comparison with Virgin Carbon:
- While regenerated carbon offers cost and environmental advantages, its performance may vary depending on the regeneration process and the nature of the adsorbed contaminants.
- Virgin carbon is often preferred for applications requiring extremely high purity or specific adsorption characteristics.
By understanding the principles and processes of carbon regeneration, industries can make informed decisions about optimizing their use of activated carbon, balancing cost, performance, and environmental impact.
Summary Table:
Aspect | Details |
---|---|
Process | Thermal regeneration (600–900°C) to remove contaminants from activated carbon. |
Key Steps | Drying, thermal decomposition, activation, cooling. |
Regeneration Systems | Rotary kilns, multiple hearth furnaces, fluidized bed reactors. |
Benefits | Cost savings, environmental sustainability, high performance. |
Applications | Water treatment, air purification, food & beverage industry. |
Challenges | Contaminant type, carbon loss (5–10%), energy consumption. |
Discover how carbon regeneration can optimize your operations—contact us today for expert guidance!