The cooling rate significantly influences the mechanical properties of metals and alloys by altering their microstructure. Rapid cooling, such as quenching, can lead to the formation of hard and brittle phases like martensite in steel, while in aluminum alloys, it may result in a softer material due to the suppression of precipitate formation. Conversely, slower cooling rates allow for more controlled phase transformations, leading to balanced mechanical properties. Understanding the relationship between cooling rate and mechanical properties is crucial for tailoring materials to specific applications.
Key Points Explained:
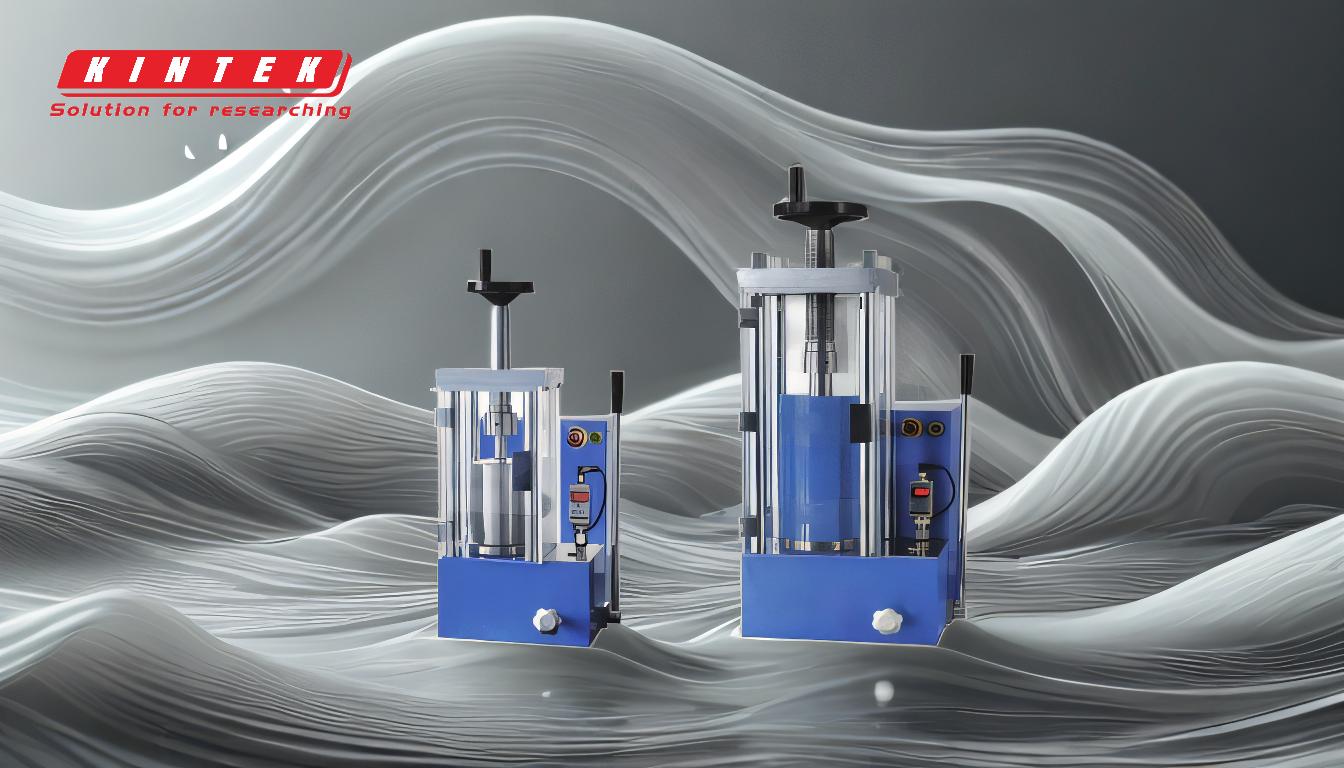
-
Cooling Rate and Microstructure Transformation:
- The cooling rate directly affects the microstructure of metals and alloys. During cooling, atoms rearrange themselves into different crystal structures, which determine the material's mechanical properties.
- Rapid cooling often prevents atoms from achieving their equilibrium positions, leading to metastable phases like martensite in steel. These phases are typically harder but more brittle.
- Slower cooling allows atoms to diffuse and form equilibrium phases, which generally exhibit better ductility and toughness.
-
Effect of Rapid Cooling on Steel:
- In steel, rapid cooling (quenching) causes the formation of martensite, a hard and brittle phase. This transformation occurs because the carbon atoms do not have enough time to diffuse out of the crystal lattice, resulting in a distorted structure.
- Martensitic transformation increases hardness and strength but reduces ductility and toughness. This makes quenched steel suitable for applications requiring wear resistance but less ideal for impact resistance.
-
Effect of Rapid Cooling on Aluminum Alloys:
- In aluminum alloys, rapid cooling suppresses the formation of precipitates, which are crucial for strengthening the material. As a result, the alloy remains softer and more ductile.
- This behavior is opposite to that of steel, where rapid cooling increases hardness. The difference arises from the distinct mechanisms of strengthening in these materials.
-
Effect of Slow Cooling:
- Slow cooling allows for controlled phase transformations and the formation of equilibrium phases. In steel, this can lead to the formation of pearlite or bainite, which provide a balance of strength and toughness.
- In aluminum alloys, slow cooling enables the precipitation of strengthening phases, enhancing the material's mechanical properties.
-
Practical Implications for Material Selection:
- The choice of cooling rate is critical in material processing to achieve the desired mechanical properties. For example, tools and dies that require high hardness are often quenched, while structural components needing toughness are cooled more slowly.
- Understanding the cooling rate's impact helps in selecting appropriate heat treatment processes for specific applications, ensuring optimal performance and durability.
-
Trade-offs in Mechanical Properties:
- There is often a trade-off between hardness and toughness. Rapid cooling increases hardness but reduces toughness, while slow cooling enhances toughness at the expense of hardness.
- Engineers must carefully balance these properties based on the intended application of the material.
By understanding how cooling rates influence mechanical properties, manufacturers can tailor materials to meet specific performance requirements, ensuring reliability and efficiency in various applications.
Summary Table:
Cooling Rate | Effect on Steel | Effect on Aluminum Alloys |
---|---|---|
Rapid Cooling | Forms martensite (hard, brittle) | Suppresses precipitate formation (softer, more ductile) |
Slow Cooling | Forms pearlite/bainite (balanced strength/toughness) | Enables precipitate formation (enhanced mechanical properties) |
Optimize your material properties with the right cooling rate—contact our experts today!