Heat treatment significantly impacts the surface roughness of metallic materials by altering their microstructure and mechanical properties. The process involves heating and cooling metals under controlled conditions, which can lead to changes in hardness, grain size, and residual stresses. These changes, in turn, affect the surface roughness. For instance, processes like annealing can reduce surface roughness by softening the material and reducing internal stresses, while hardening treatments may increase roughness due to the formation of harder, more brittle phases. The cooling rate, temperature, and specific heat treatment method all play critical roles in determining the final surface roughness.
Key Points Explained:
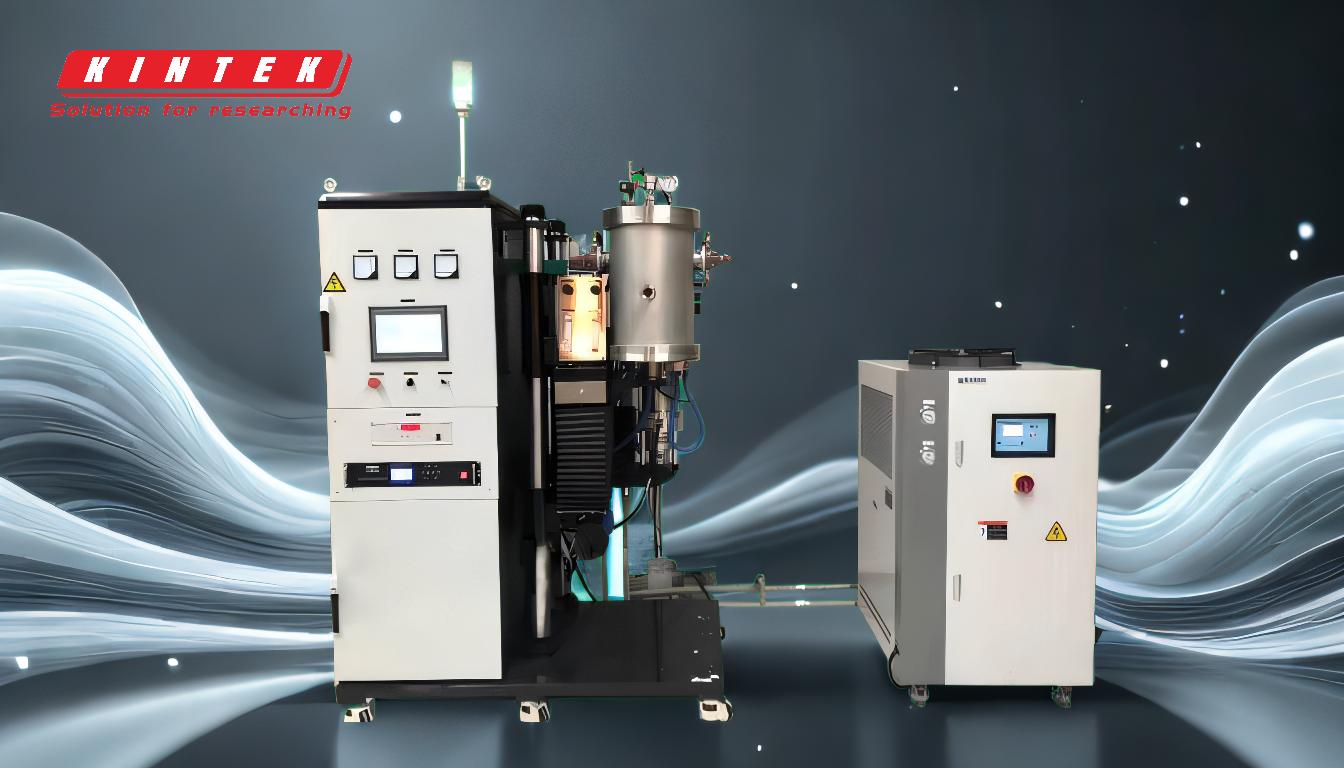
-
Microstructural Changes During Heat Treatment
- Heat treatment alters the microstructure of metals, including grain size, phase composition, and distribution of phases.
- For example, annealing refines the grain structure, making it more uniform, which can lead to a smoother surface.
- Conversely, quenching can create a martensitic structure, which is harder but may result in a rougher surface due to increased brittleness and residual stresses.
-
Effect of Hardness on Surface Roughness
- Hardness is a key factor influencing surface roughness.
- Softer materials (e.g., after annealing) are easier to machine or polish, resulting in a smoother surface.
- Harder materials (e.g., after quenching or tempering) are more difficult to machine and may exhibit higher surface roughness due to tool wear or micro-cracking during finishing processes.
-
Residual Stresses and Surface Roughness
- Heat treatment can introduce residual stresses in the material.
- Rapid cooling (quenching) often leads to high residual stresses, which can cause warping or micro-cracking, increasing surface roughness.
- Stress-relieving treatments (e.g., tempering) can reduce these stresses and improve surface finish.
-
Cooling Rate and Its Impact
- The cooling rate during heat treatment is critical.
- Slow cooling (e.g., in annealing) allows for a more uniform microstructure and reduces surface roughness.
- Fast cooling (e.g., in quenching) can lead to uneven microstructural changes and increased surface roughness.
-
Specific Heat Treatment Methods and Surface Roughness
- Annealing: Typically reduces surface roughness by softening the material and reducing internal stresses.
- Quenching: Often increases surface roughness due to the formation of hard, brittle phases and residual stresses.
- Tempering: Can improve surface roughness by relieving stresses and stabilizing the microstructure.
- Normalizing: Produces a more uniform grain structure, which can lead to a smoother surface compared to as-cast or as-forged conditions.
-
Practical Considerations for Equipment and Consumable Purchasers
- When selecting heat treatment processes, consider the desired surface finish and the material's final application.
- For applications requiring a smooth surface, annealing or tempering may be preferred.
- For applications requiring high hardness and wear resistance, quenching followed by tempering may be necessary, but additional finishing processes (e.g., grinding or polishing) may be required to achieve the desired surface roughness.
- Ensure that heat treatment equipment (e.g., furnaces, quenching systems) is capable of precise temperature and cooling rate control to achieve consistent results.
By understanding these factors, purchasers can make informed decisions about heat treatment processes and equipment to achieve the desired surface roughness for their specific applications.
Summary Table:
Factor | Impact on Surface Roughness |
---|---|
Microstructural Changes | Annealing refines grain structure, reducing roughness; quenching increases roughness. |
Hardness | Softer materials (e.g., after annealing) yield smoother surfaces; harder materials increase roughness. |
Residual Stresses | Rapid cooling (quenching) increases stresses and roughness; tempering reduces roughness. |
Cooling Rate | Slow cooling (e.g., annealing) reduces roughness; fast cooling (e.g., quenching) increases it. |
Heat Treatment Methods | Annealing reduces roughness; quenching increases it; tempering and normalizing improve finish. |
Achieve the perfect surface roughness for your materials—contact our experts today for tailored heat treatment solutions!