A medium frequency induction furnace operates by transforming three-phase power frequency alternating current into direct current, which is then converted into an adjustable current. This current passes through a capacitor and an induction coil, creating high-density magnetic lines of force. These magnetic lines interact with the metal material within the induction coil, inducing large eddy currents. The eddy currents, behaving like medium frequency currents, cause the free electrons in the metal to move, generating heat through resistance. This process efficiently heats the metal for melting or other thermal processes.
Key Points Explained:
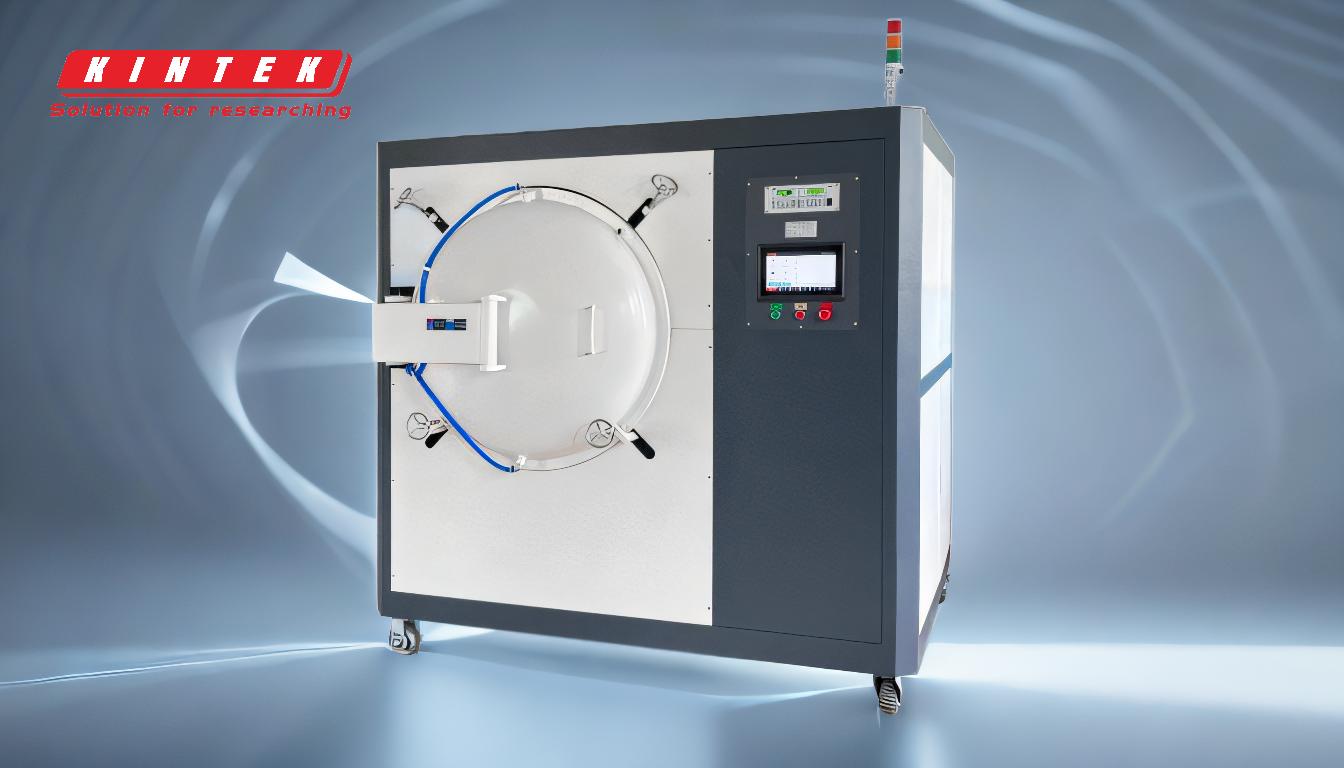
-
Conversion of Power:
- The induction furnace begins by converting three-phase power frequency alternating current (AC) into direct current (DC). This conversion is typically achieved using rectifiers, which are essential for stabilizing the power supply before further processing.
-
Transformation into Adjustable Current:
- The DC is then transformed into an adjustable current. This step is crucial as it allows for precise control over the heating process, enabling the furnace to handle different types of metals and varying sizes of loads.
-
Flow Through Capacitor and Induction Coil:
- The adjustable current flows through a capacitor and an induction coil. The capacitor helps in managing the power factor and stabilizing the current, while the induction coil is the core component where the magnetic field is generated.
-
Generation of High-Density Magnetic Lines of Force:
- As the current passes through the induction coil, it generates high-density magnetic lines of force. These magnetic lines are essential for the induction heating process, as they interact with the metal material placed within the coil.
-
Induction of Eddy Currents:
- The high-density magnetic lines cut through the metal material inside the induction coil, inducing large eddy currents. These eddy currents are loops of electrical current induced within the metal due to the changing magnetic field.
-
Heat Generation Through Resistance:
- The eddy currents, which have properties similar to medium frequency current, cause the free electrons in the metal to flow. This electron movement generates heat due to the electrical resistance of the metal. The heat is then used for melting or other thermal processes.
-
Efficiency and Control:
- The use of IGBT induction furnace technology enhances the efficiency and control of the heating process. IGBTs (Insulated Gate Bipolar Transistors) allow for precise control over the current and frequency, leading to more efficient energy use and better temperature regulation.
-
Applications:
- Induction furnaces are widely used in metal melting, heat treatment, and other industrial processes where precise and efficient heating is required. The ability to control the heating process makes them suitable for a variety of metals and alloys.
By understanding these key points, one can appreciate the sophisticated technology behind induction furnaces and their critical role in modern industrial processes. The integration of IGBT induction furnace technology further enhances their performance, making them indispensable in metal processing industries.
Summary Table:
Key Process | Description |
---|---|
Power Conversion | Converts three-phase AC to DC using rectifiers for stable power supply. |
Adjustable Current Transformation | DC is transformed into adjustable current for precise heating control. |
Capacitor and Induction Coil | Current flows through a capacitor and induction coil to generate magnetic fields. |
Magnetic Lines of Force | High-density magnetic lines interact with metal, inducing eddy currents. |
Heat Generation | Eddy currents cause electron movement, generating heat through resistance. |
Efficiency and Control | IGBT technology ensures precise current and frequency control for optimal heating. |
Applications | Used in metal melting, heat treatment, and other industrial processes. |
Discover how an induction furnace can revolutionize your metal processing—contact our experts today!