Magnetic field heating of metals, commonly known as induction heating, is a process where an alternating magnetic field induces electrical currents (eddy currents) within a metal, causing it to heat up due to electrical resistance. This method is widely used in industrial applications for heating, melting, and hardening metals. The process is efficient, precise, and contactless, making it ideal for applications requiring localized heating or high temperatures. The key to this phenomenon lies in the interaction between the magnetic field and the metal's conductive properties, as well as the material's resistance to the induced currents.
Key Points Explained:
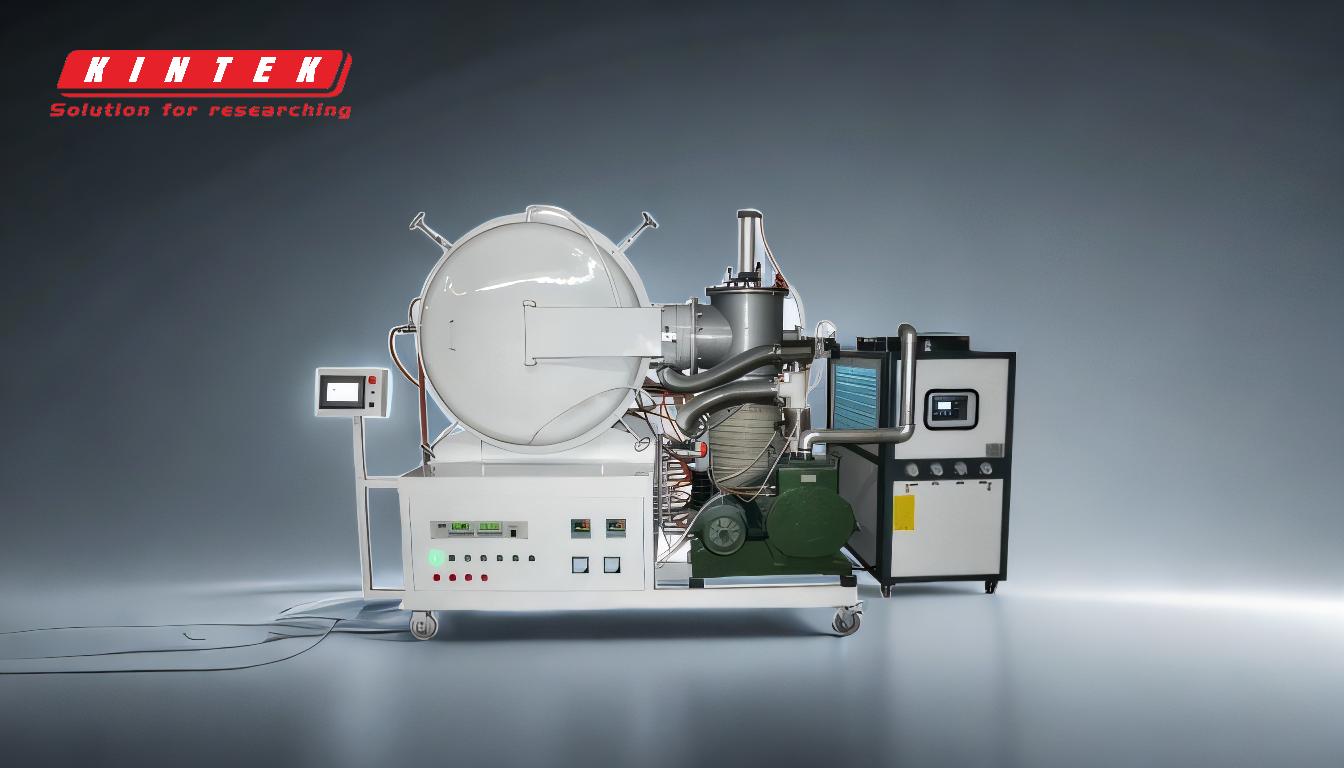
-
Principle of Induction Heating:
- Induction heating relies on Faraday's Law of Electromagnetic Induction, which states that a changing magnetic field induces an electric current in a conductor.
- When an alternating current (AC) passes through a coil, it generates a rapidly alternating magnetic field around the coil.
- This magnetic field penetrates the metal object placed within or near the coil, inducing eddy currents within the metal.
-
Eddy Currents and Joule Heating:
- Eddy currents are circular electric currents induced within the metal due to the changing magnetic field.
- These currents encounter resistance as they flow through the metal, leading to Joule heating (also known as resistive heating).
- The heat generated is proportional to the square of the current and the electrical resistance of the metal.
-
Skin Effect:
- The skin effect refers to the tendency of alternating currents to flow near the surface of a conductor.
- In induction heating, this means that the eddy currents and resulting heat are concentrated near the surface of the metal.
- The depth of heating penetration depends on the frequency of the alternating current: higher frequencies result in shallower penetration, while lower frequencies allow deeper heating.
-
Factors Influencing Induction Heating:
- Electrical Conductivity: Metals with higher electrical conductivity (e.g., copper, aluminum) require stronger magnetic fields or higher frequencies to achieve significant heating.
- Magnetic Permeability: Ferromagnetic materials (e.g., iron, steel) heat more efficiently due to their higher magnetic permeability, which enhances the magnetic field's interaction with the material.
- Frequency of the Alternating Current: The choice of frequency depends on the application. High frequencies (kHz to MHz) are used for surface heating, while low frequencies (50-60 Hz) are suitable for bulk heating.
-
Applications of Induction Heating:
- Metal Hardening: Induction heating is used to selectively harden the surface of metal components, such as gears and shafts, without affecting the core.
- Melting and Casting: Induction furnaces are used to melt metals for casting, offering precise temperature control and high efficiency.
- Brazing and Soldering: Induction heating provides localized heating for joining metals, ensuring clean and strong bonds.
- Annealing and Tempering: These processes involve heating and cooling metals to alter their mechanical properties, and induction heating offers precise control over the temperature profile.
-
Advantages of Induction Heating:
- Efficiency: Induction heating is highly efficient because the heat is generated directly within the metal, minimizing energy loss.
- Precision: The process allows for localized and controlled heating, reducing the risk of overheating or damaging surrounding areas.
- Speed: Induction heating can achieve high temperatures rapidly, making it suitable for high-speed production processes.
- Cleanliness: Since no flames or external heat sources are used, the process is clean and reduces the risk of contamination.
-
Limitations of Induction Heating:
- Material Dependency: The effectiveness of induction heating depends on the material's electrical and magnetic properties. Non-conductive or non-magnetic materials cannot be heated using this method.
- Equipment Cost: Induction heating systems can be expensive to install and maintain, especially for high-power applications.
- Depth Limitations: The skin effect limits the depth of heating, making it less suitable for applications requiring uniform heating throughout thick materials.
In summary, magnetic field heating of metals through induction is a versatile and efficient process that leverages electromagnetic principles to generate heat within conductive materials. Its applications span various industries, offering precise, rapid, and clean heating solutions. However, its effectiveness is influenced by material properties and the design of the induction system.
Summary Table:
Aspect | Details |
---|---|
Principle | Faraday's Law of Electromagnetic Induction induces eddy currents in metals. |
Key Factors | Electrical conductivity, magnetic permeability, and AC frequency. |
Applications | Metal hardening, melting, brazing, annealing, and tempering. |
Advantages | Efficient, precise, fast, and clean heating process. |
Limitations | Material dependency, equipment cost, and depth limitations. |
Discover how induction heating can optimize your industrial processes—contact our experts today!