Magnetron sputtering is a widely used physical vapor deposition (PVD) technique for depositing thin films of materials such as metals, plastics, and ceramics onto substrates. It operates in a vacuum or low-pressure environment, utilizing a combination of electric and magnetic fields to create a high-density plasma. The process involves bombarding a target material (cathode) with high-energy ions, causing atoms to be ejected from the target surface. These ejected atoms then travel to the substrate, where they condense to form a thin, uniform, and dense film. The magnetic field plays a crucial role in trapping electrons near the target surface, increasing ionization efficiency and sustaining the plasma. This method is favored for its low deposition temperature, high deposition rates, and ability to produce high-quality coatings.
Key Points Explained:
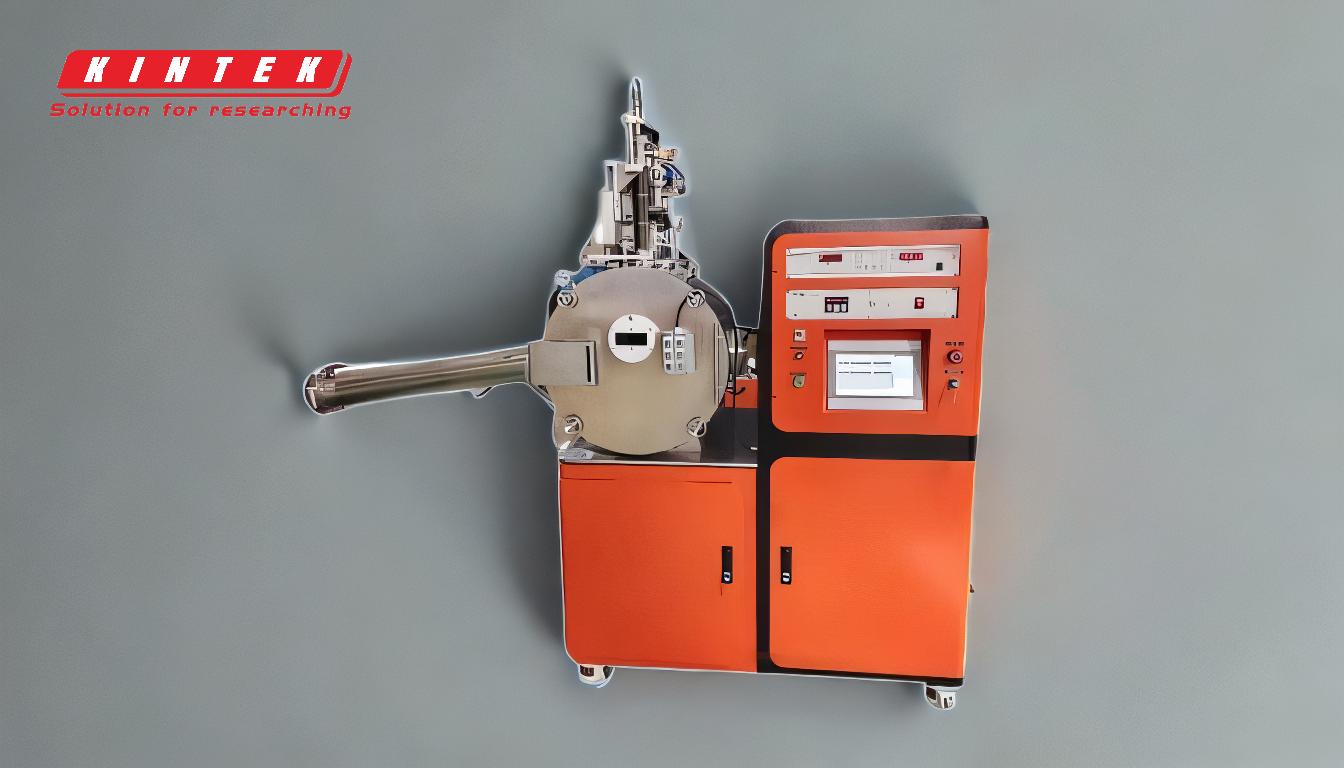
-
Basic Principle of Magnetron Sputtering:
- Magnetron sputtering is a PVD process where a target material is bombarded by high-energy ions in a vacuum or low-pressure environment.
- The process involves the ejection of atoms from the target surface, which then travel to the substrate and form a thin film.
-
Role of Electric and Magnetic Fields:
- A negative voltage is applied to the target (cathode), attracting positive ions from the plasma.
- The magnetic field, generated by the magnetron, traps electrons near the target surface, increasing their residence time and enhancing collisions with gas atoms (e.g., argon).
- This increases ionization and sustains the plasma, leading to a higher density of ions available for sputtering.
-
Ion Bombardment and Sputtering:
- Positive ions (e.g., Ar⁺) are accelerated toward the target by the electric field.
- When these ions strike the target surface, they transfer kinetic energy, causing atoms on the target surface to be ejected (sputtered).
- The sputtered atoms are neutral and move toward the substrate, where they condense to form a thin film.
-
Plasma Generation and Maintenance:
- The plasma is generated by applying electrical energy to ionize the inert gas (e.g., argon) in the chamber.
- Secondary electrons emitted from the target collide with gas atoms, ionizing them and maintaining the plasma.
- The magnetic field ensures that electrons follow a circular trajectory, increasing their chances of ionizing gas atoms.
-
Advantages of Magnetron Sputtering:
- Low Deposition Temperature: Ideal for coating temperature-sensitive substrates.
- High Deposition Rates: Faster than many other PVD techniques.
- Uniform and Dense Films: Produces high-quality, uniform coatings over large areas.
- Versatility: Can deposit a wide range of materials, including metals, ceramics, and plastics.
-
Process Steps:
- Setup: Place the target material (cathode) and substrate in a vacuum chamber filled with inert gas (e.g., argon).
- Plasma Generation: Apply a high voltage to ionize the gas and create a plasma.
- Ion Bombardment: Positive ions accelerate toward the target, ejecting atoms from its surface.
- Film Deposition: Sputtered atoms travel to the substrate and condense to form a thin film.
- Magnetic Field Control: The magnetic field ensures efficient ionization and sustained plasma.
-
Applications:
- Industrial Coatings: Used for wear-resistant, corrosion-resistant, and decorative coatings.
- Semiconductors: Deposits thin films for microelectronics and solar cells.
- Optics: Creates anti-reflective and reflective coatings for lenses and mirrors.
- Medical Devices: Provides biocompatible coatings for implants and surgical tools.
-
Key Components:
- Magnetron: Generates the magnetic field and houses the target material.
- Vacuum Chamber: Provides the low-pressure environment necessary for the process.
- Power Supply: Supplies the high voltage needed to ionize the gas and sustain the plasma.
- Substrate Holder: Holds the substrate in place during deposition.
By combining electric and magnetic fields, magnetron sputtering achieves efficient and high-quality thin film deposition, making it a cornerstone of modern coating technologies.
Summary Table:
Aspect | Details |
---|---|
Process | Physical vapor deposition (PVD) using electric and magnetic fields. |
Key Components | Magnetron, vacuum chamber, power supply, substrate holder. |
Advantages | Low deposition temperature, high deposition rates, uniform and dense films. |
Applications | Industrial coatings, semiconductors, optics, medical devices. |
Key Steps | Plasma generation, ion bombardment, film deposition, magnetic field control. |
Interested in magnetron sputtering for your applications? Contact us today to learn more!