Vacuum arc remelting (VAR) is a specialized secondary melting process used to produce high-purity and homogeneous metal ingots. It operates under vacuum conditions, utilizing an electric arc to melt a starting electrode, which then drips into a molten pool and solidifies into the final ingot. This process eliminates contamination from external air, reduces impurities, and enhances the mechanical properties of the metal. VAR is particularly valuable in industries requiring ultra-clean and fatigue-resistant materials, such as aerospace, medical, and energy sectors.
Key Points Explained:
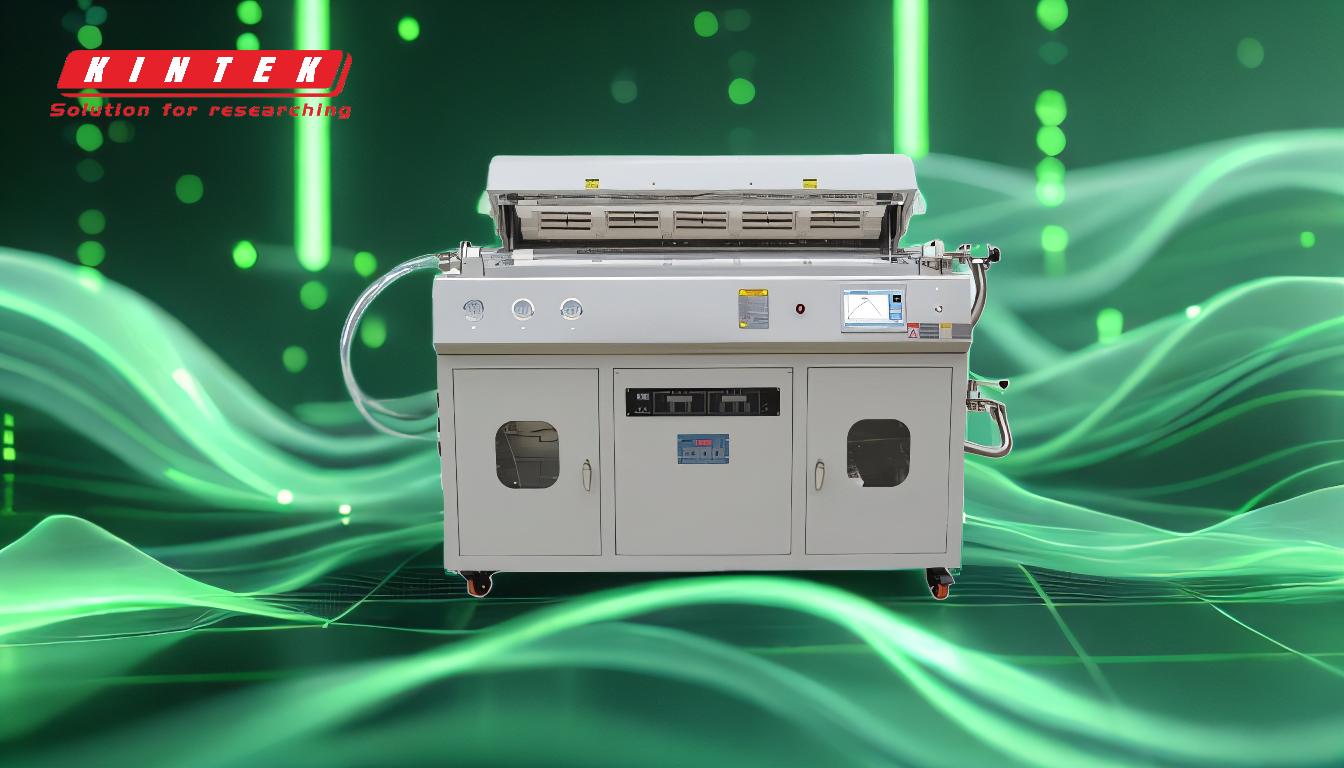
-
Process Overview:
- VAR is a secondary melting process designed to meet stringent cleanliness and homogeneity requirements.
- It involves remelting a starting electrode under vacuum using an electric arc.
- The electrode gradually melts, forming a molten pool that solidifies into a high-quality ingot.
-
Vacuum Environment:
- The vacuum environment prevents contamination from external air, ensuring a cleaner final product.
- It also helps in reducing gas content and volatile impurities, which are critical for achieving high-purity metals.
-
Heat Source:
- The electric arc serves as the primary heat source, providing precise control over the melting process.
- This controlled heat input ensures uniform melting and solidification, leading to improved material properties.
-
Applications:
- VAR is widely used in industries that demand high-performance materials, such as aerospace (for turbine blades and engine components), medical (for implants and surgical tools), and energy (for nuclear and power generation components).
- The process enhances fatigue resistance, mechanical strength, and overall material reliability.
-
Advantages:
- Improved Purity: The vacuum environment eliminates impurities, resulting in cleaner metals.
- Enhanced Homogeneity: Uniform melting and solidification lead to consistent material properties.
- Superior Mechanical Properties: VAR-processed materials exhibit better fatigue resistance and strength, making them ideal for critical applications.
-
Comparison with Other Processes:
- Unlike conventional melting and casting processes, VAR offers superior control over material purity and microstructure.
- It is often used when standard production methods cannot meet the required specifications for cleanliness and homogeneity.
-
Challenges:
- VAR requires specialized equipment and precise control, making it more expensive and complex than conventional methods.
- The process is slower due to the need for careful monitoring and control of the melting and solidification stages.
By understanding these key points, equipment and consumable purchasers can better evaluate the suitability of VAR for their specific needs, particularly in applications where material purity and performance are critical.
Summary Table:
Key Aspect | Description |
---|---|
Process Overview | Remelts a starting electrode under vacuum using an electric arc. |
Vacuum Environment | Prevents contamination, reduces impurities, and ensures high-purity metals. |
Heat Source | Electric arc provides precise control for uniform melting and solidification. |
Applications | Aerospace (turbine blades), medical (implants), and energy (nuclear components). |
Advantages | Improved purity, enhanced homogeneity, and superior mechanical properties. |
Challenges | High cost, specialized equipment, and slower process due to precise control. |
Discover how vacuum arc remelting can elevate your material quality—contact our experts today!