Graphene preparation using Chemical Vapor Deposition (CVD) is a highly promising method for producing high-quality graphene on large areas. CVD involves the decomposition of hydrocarbon gases on a metallic substrate, typically copper or nickel, at high temperatures. This process allows for the controlled growth of graphene layers, making it suitable for industrial applications. The method is widely used due to its scalability, reproducibility, and ability to produce graphene with excellent electrical and mechanical properties. Below is a detailed explanation of the CVD process for graphene preparation.
Key Points Explained:
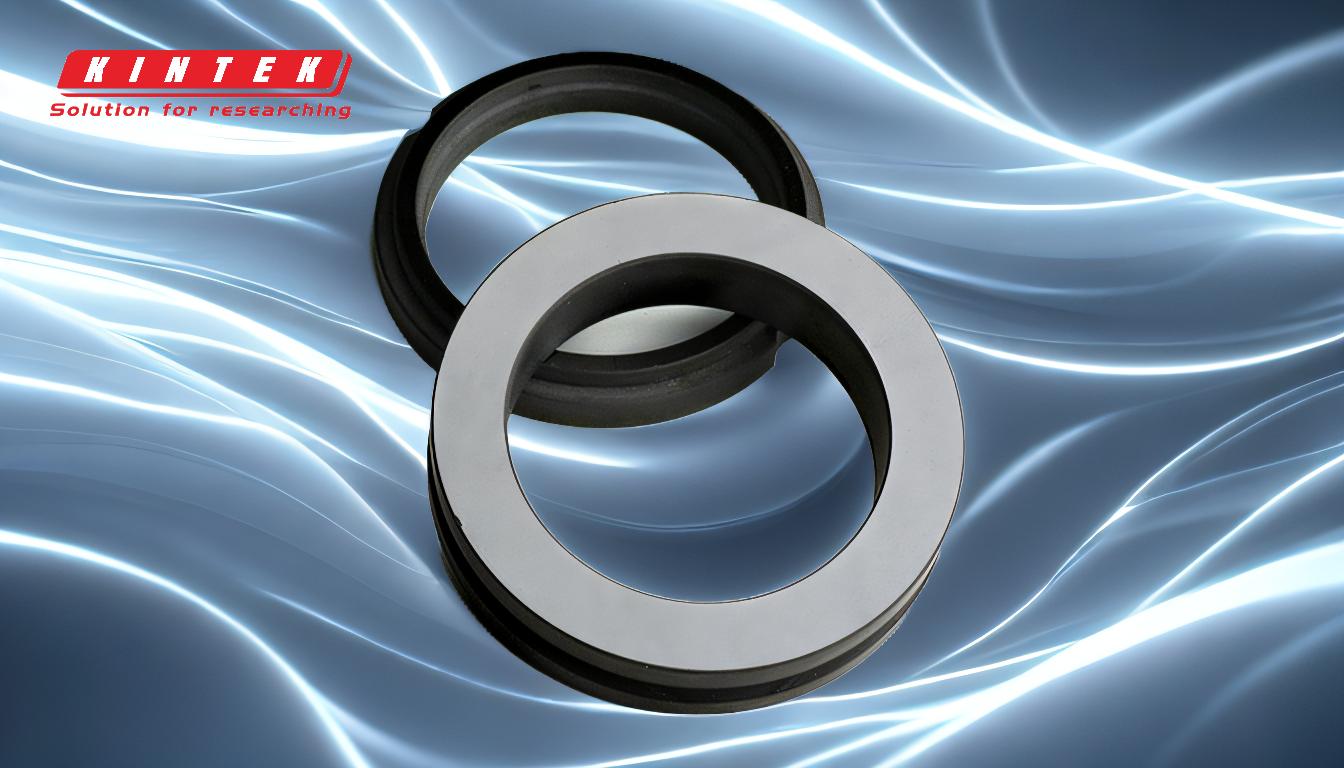
-
Overview of CVD for Graphene Production
- CVD is a bottom-up synthesis method where graphene is grown on a substrate by decomposing hydrocarbon gases.
- It is the most promising technique for producing high-quality graphene on large scales, making it ideal for industrial applications.
- The process involves heating a metallic substrate (e.g., copper or nickel) in a controlled environment and introducing hydrocarbon gases like methane or ethylene.
-
Steps in the CVD Process
- Substrate Preparation: A metal substrate, typically copper or nickel, is cleaned and placed in a CVD chamber. Copper is preferred due to its low carbon solubility, which allows for the growth of single-layer graphene.
- Heating and Annealing: The substrate is heated to high temperatures (around 1000°C) in the presence of hydrogen gas to remove surface oxides and create a smooth surface for graphene growth.
- Introduction of Hydrocarbon Gas: A hydrocarbon gas, such as methane, is introduced into the chamber. The gas decomposes at high temperatures, releasing carbon atoms that adsorb onto the substrate.
- Graphene Growth: Carbon atoms diffuse on the substrate surface and form a hexagonal lattice structure, leading to the growth of graphene.
- Cooling and Transfer: The chamber is cooled, and the graphene layer is transferred from the metallic substrate to a target material, such as silicon dioxide or flexible polymers, using techniques like wet transfer or roll-to-roll transfer.
-
Advantages of CVD for Graphene Production
- Scalability: CVD can produce graphene on large areas, making it suitable for industrial applications.
- High Quality: The graphene produced by CVD exhibits excellent electrical, thermal, and mechanical properties.
- Controlled Growth: The process allows for precise control over the number of graphene layers and their quality.
- Versatility: CVD-grown graphene can be transferred to various substrates, enabling its use in diverse applications.
-
Applications of CVD-Grown Graphene
- Electronics: CVD graphene is used in transistors, sensors, and flexible electronics due to its high conductivity and transparency.
- Energy Storage: It is employed in supercapacitors and batteries for its high surface area and conductivity.
- Sensors: Graphene's sensitivity to environmental changes makes it ideal for biosensors, gas sensors, and pressure sensors.
- Composites: CVD graphene is incorporated into polymers and other materials to enhance their mechanical and electrical properties.
-
Challenges and Future Directions
- Cost: The high cost of CVD equipment and substrates can be a barrier to widespread adoption.
- Transfer Process: Transferring graphene from the metallic substrate to other materials without damaging it remains a challenge.
- Defect Control: Minimizing defects during the growth process is crucial for achieving consistent quality.
- Research Focus: Ongoing research aims to optimize the CVD process, reduce costs, and develop new applications for CVD-grown graphene.
In summary, CVD is a highly effective method for producing high-quality graphene on large scales, making it a cornerstone of graphene research and industrial applications. Its scalability, controlled growth, and versatility ensure its continued importance in advancing graphene-based technologies.
Summary Table:
Aspect | Details |
---|---|
Process | Decomposition of hydrocarbon gases on metallic substrates (e.g., copper, nickel). |
Key Steps | Substrate preparation, heating, hydrocarbon introduction, growth, transfer. |
Advantages | Scalability, high quality, controlled growth, versatility. |
Applications | Electronics, energy storage, sensors, composites. |
Challenges | High cost, transfer process, defect control, ongoing research. |
Discover how CVD can revolutionize your graphene production—contact our experts today!