The sintering process duration varies significantly depending on the materials, techniques, and specific requirements of the final product. Generally, sintering can take anywhere from a few milliseconds to over 24 hours. The process itself may only take seconds, but post-form sintering steps can extend the total time to several hours. Factors such as temperature, heating rate, pressure, particle size, composition, and the sintering atmosphere (e.g., air, vacuum, or inert gases) play crucial roles in determining the sintering time. High-temperature sintering can enhance material properties like tensile strength and impact energy, but it also requires precise control over the sintering environment. For many applications, the sintering process typically ranges from 15 to 20 hours, depending on the material and desired density of the final part.
Key Points Explained:
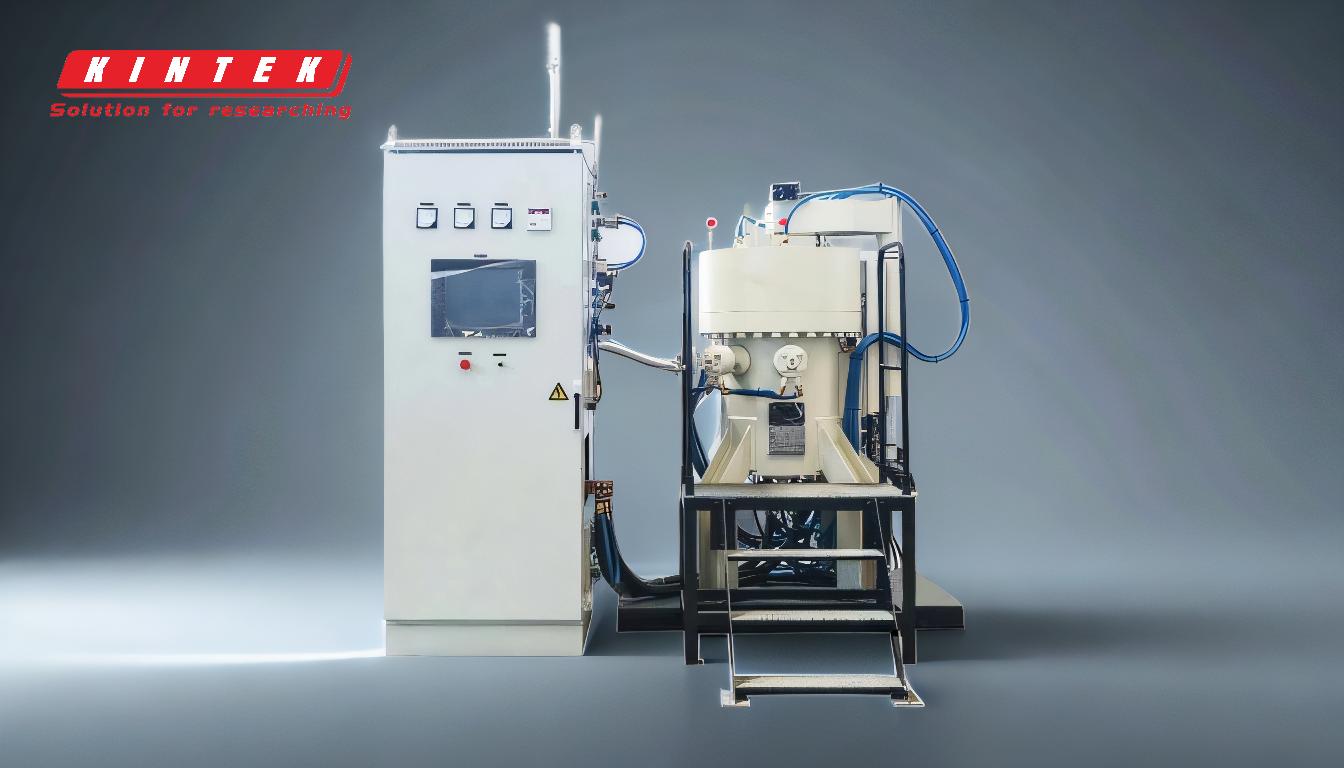
-
Range of Sintering Times:
- Sintering can take anywhere from a few milliseconds to over 24 hours.
- The process itself may only take seconds, but post-form sintering steps can extend the total time to several hours.
-
Factors Influencing Sintering Time:
- Temperature: Determines sintering kinetics and material properties. Higher temperatures can speed up the process but must be carefully controlled to avoid material degradation.
- Heating Rate: Affects densification. A faster heating rate can reduce sintering time but may lead to uneven densification.
- Pressure: Enhances particle rearrangement and eliminates porosity, which can shorten the sintering time.
- Particle Size and Composition: Smaller particles and homogeneous compositions promote better densification, potentially reducing sintering time.
-
Sintering Atmosphere:
- The atmosphere (e.g., air, vacuum, or argon/nitrogen) can significantly impact the sintering process. Inert atmospheres are often used to prevent oxidation and other undesirable reactions, which can affect the sintering time and final material properties.
-
Material and Density Requirements:
- The sintering furnace temperature and time depend on the material being used and the required density of the final part. Different materials have different sintering requirements, and achieving higher densities may require longer sintering times.
-
Typical Sintering Durations:
- For many industrial applications, the sintering process typically takes anywhere from 15 to 20 hours. This duration can vary based on the specific material, desired properties, and the type of sintering furnace used (e.g., belt conveyor, push, or batch furnace).
-
Post-Form Sintering:
- While the initial sintering process may be quick, post-form sintering steps can take several hours. These steps are crucial for achieving the final desired properties and dimensions of the sintered part.
-
Impact on Material Properties:
- High-temperature sintering can increase tensile strength, bending fatigue strength, and impact energy. However, achieving these properties often requires precise control over the sintering environment and can extend the overall sintering time.
In summary, the sintering time is highly variable and depends on a multitude of factors, including material properties, desired outcomes, and process conditions. Understanding these factors is crucial for optimizing the sintering process to achieve the desired material properties efficiently.
Summary Table:
Factor | Impact on Sintering Time |
---|---|
Temperature | Higher temps speed up sintering but require precise control to avoid material degradation. |
Heating Rate | Faster heating reduces time but may cause uneven densification. |
Pressure | Enhances particle rearrangement, shortening sintering time. |
Particle Size | Smaller particles promote faster densification. |
Sintering Atmosphere | Inert gases prevent oxidation, affecting time and final properties. |
Material/Density | Denser materials or higher density requirements increase sintering time. |
Typical Duration | 15–20 hours for many industrial applications, depending on material and furnace type. |
Need help optimizing your sintering process? Contact our experts today for tailored solutions!