The lifespan of a hot air furnace typically ranges between 15 to 30 years, with some units lasting over 40 years under exceptional circumstances. The longevity of a furnace largely depends on factors such as proper sizing, correct installation, and regular maintenance. Annual maintenance is crucial to ensure the furnace operates efficiently and lasts beyond the 15-year mark. Understanding these factors can help purchasers make informed decisions about their heating systems.
Key Points Explained:
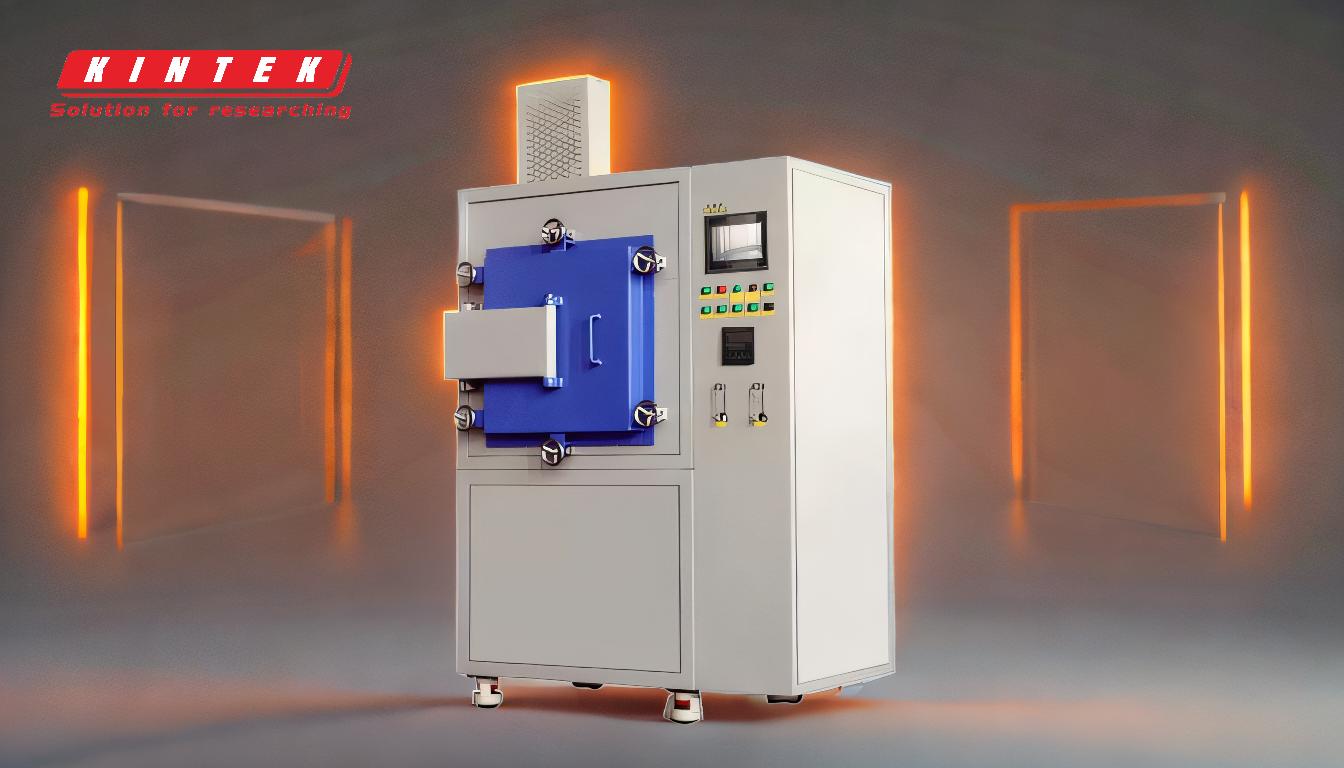
-
Average Lifespan of a Hot Air Furnace:
- The typical lifespan of a hot air furnace ranges from 15 to 30 years.
- In rare cases, a furnace can last over 40 years, but this is not common.
-
Factors Influencing Furnace Longevity:
- Proper Sizing: A furnace that is correctly sized for the space it needs to heat will operate more efficiently and have a longer lifespan.
- Correct Installation: Proper installation by a qualified technician ensures that the furnace operates as intended, reducing the risk of premature failure.
- Regular Maintenance: Annual maintenance is essential to keep the furnace running smoothly. This includes cleaning, inspecting, and servicing the unit to prevent wear and tear.
-
Importance of Annual Maintenance:
- Regular maintenance can significantly extend the life of a furnace, often allowing it to last well beyond 15 years.
- Maintenance tasks typically include cleaning or replacing filters, checking for leaks, and ensuring all components are functioning correctly.
-
Purchaser Considerations:
- When purchasing a furnace, consider the brand reputation and warranty offered. Some brands are known for their durability and longevity.
- Ensure that the furnace is professionally installed and that you have a plan for regular maintenance.
By understanding these key points, purchasers can make informed decisions that will help them get the most out of their investment in a hot air furnace.
Summary Table:
Aspect | Details |
---|---|
Average Lifespan | 15–30 years (can exceed 40 years with exceptional care) |
Key Factors | Proper sizing, correct installation, regular maintenance |
Maintenance Importance | Annual maintenance extends lifespan beyond 15 years |
Purchaser Tips | Choose reputable brands, ensure professional installation, plan maintenance |
Ready to maximize your furnace's lifespan? Contact our experts today for professional advice and maintenance services!