Annealing is a heat treatment process used to alter the physical and sometimes chemical properties of a material, typically metals, to increase ductility, reduce hardness, and improve machinability. There are several types of annealing processes, each tailored to specific materials and desired outcomes. The primary types include Black Annealing, Blue Annealing, Box Annealing, Bright Annealing, Cycle Annealing, Flame Annealing, Full Annealing, Graphitizing, Intermediate Annealing, Isothermal Annealing, Process Annealing, Quench Annealing, and Spheroidizing. These processes differ in terms of temperature, cooling rate, and the specific goals they aim to achieve, such as stress relief, softening, or microstructure modification.
Key Points Explained:
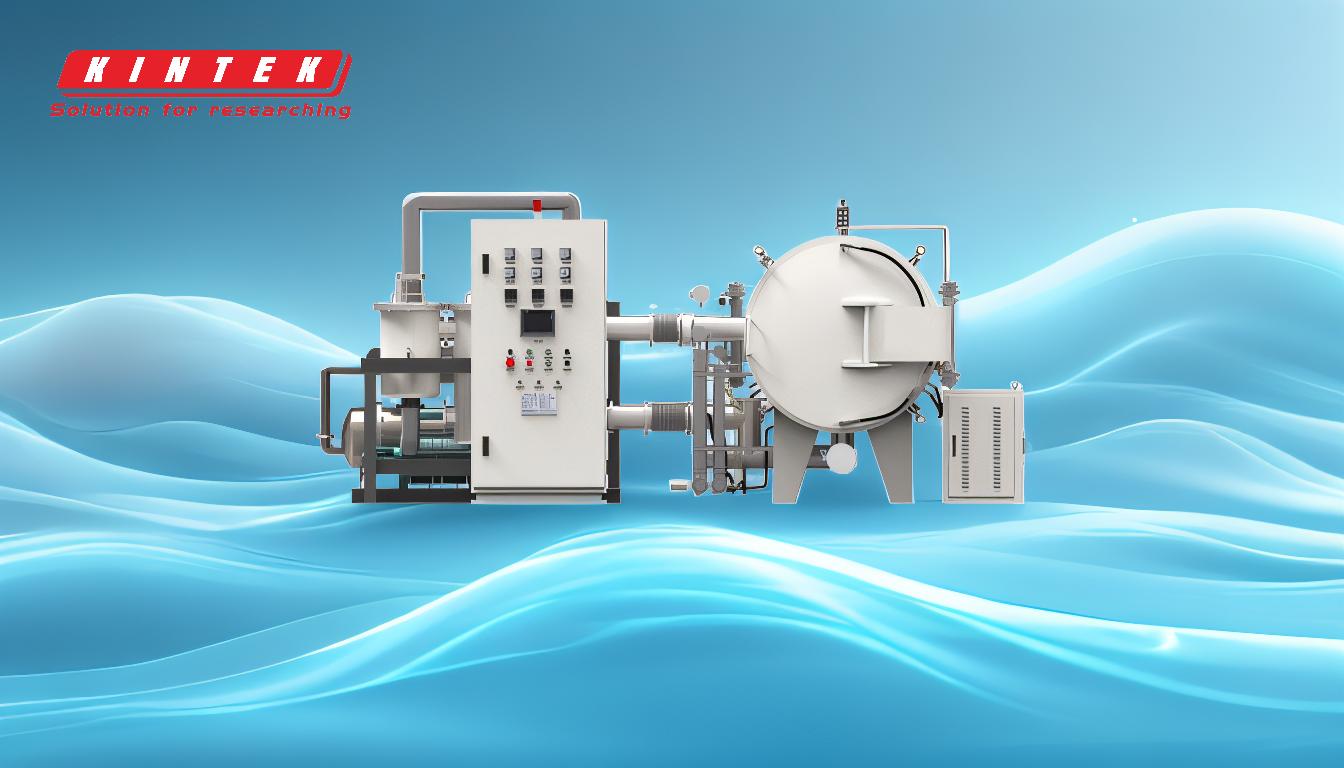
-
Black Annealing:
- Description: Black annealing is typically used for steel and involves heating the metal in the presence of a reducing atmosphere to prevent oxidation. The process results in a black oxide layer on the surface of the metal.
- Application: This method is often used for low-carbon steel sheets and wires, where surface finish is not a critical factor.
-
Blue Annealing:
- Description: Blue annealing is similar to black annealing but is performed at a lower temperature, resulting in a blue oxide layer on the surface.
- Application: This process is commonly used for stainless steel to improve its corrosion resistance and surface finish.
-
Box Annealing:
- Description: Box annealing involves placing the metal in a sealed container or box to protect it from oxidation during heating. The metal is heated to a specific temperature and then slowly cooled.
- Application: This method is often used for batch processing of steel coils, ensuring uniform heating and cooling.
-
Bright Annealing:
- Description: Bright annealing is performed in a controlled atmosphere or vacuum to prevent oxidation, resulting in a bright, clean surface finish.
- Application: This process is commonly used for stainless steel and other metals where a high-quality surface finish is required.
-
Cycle Annealing:
- Description: Cycle annealing involves repeated heating and cooling cycles to achieve specific material properties.
- Application: This method is used for materials that require precise control over their microstructure, such as certain alloys.
-
Flame Annealing:
- Description: Flame annealing uses a direct flame to heat the metal to the required temperature, followed by slow cooling.
- Application: This process is often used for localized annealing of large or complex-shaped components.
-
Full Annealing:
- Description: Full annealing involves heating the metal to a temperature above its upper critical temperature, holding it at that temperature, and then slowly cooling it in the furnace.
- Application: This process is used to achieve maximum softness and ductility in metals, making it suitable for subsequent forming operations.
-
Graphitizing:
- Description: Graphitizing is a specialized annealing process used to convert carbon in cast iron into graphite, improving machinability and reducing brittleness.
- Application: This method is specific to cast iron and is used to enhance its mechanical properties.
-
Intermediate Annealing:
- Description: Intermediate annealing is performed between cold working operations to restore ductility and reduce hardness.
- Application: This process is commonly used in the manufacturing of wires, tubes, and sheets that undergo multiple cold-forming steps.
-
Isothermal Annealing:
- Description: Isothermal annealing involves heating the metal to a specific temperature, holding it at that temperature for a set period, and then cooling it at a controlled rate.
- Application: This method is used for materials that require a uniform microstructure, such as certain steels and alloys.
-
Process Annealing:
- Description: Process annealing is a lower-temperature annealing process used to relieve internal stresses in cold-worked metals without significantly altering their microstructure.
- Application: This process is often used in the production of steel sheets and wires to improve their formability.
-
Quench Annealing:
- Description: Quench annealing involves heating the metal to a high temperature and then rapidly cooling it (quenching) to achieve specific material properties.
- Application: This method is used for materials that require a combination of hardness and toughness, such as certain tool steels.
-
Spheroidizing:
- Description: Spheroidizing is an annealing process that results in the formation of spheroidal carbides in the microstructure, improving machinability and reducing hardness.
- Application: This process is commonly used for high-carbon steels and tool steels to enhance their workability.
Conclusion:
Understanding the different types of annealing processes is crucial for selecting the appropriate method based on the material and desired outcome. Each process has specific applications and benefits, making it essential to choose the right one to achieve the desired material properties. Whether the goal is to improve ductility, reduce hardness, or enhance machinability, there is an annealing process tailored to meet those needs.
Summary Table:
Annealing Type | Description | Application |
---|---|---|
Black Annealing | Heated in a reducing atmosphere, resulting in a black oxide layer. | Low-carbon steel sheets and wires. |
Blue Annealing | Similar to black annealing but at lower temperatures, forming a blue oxide layer. | Stainless steel for improved corrosion resistance. |
Box Annealing | Metal is sealed in a container to prevent oxidation, ensuring uniform heating. | Batch processing of steel coils. |
Bright Annealing | Performed in a controlled atmosphere or vacuum for a clean, bright surface. | Stainless steel and metals requiring high-quality finishes. |
Cycle Annealing | Repeated heating and cooling cycles for precise microstructure control. | Alloys needing specific material properties. |
Flame Annealing | Direct flame heating followed by slow cooling. | Localized annealing of large or complex components. |
Full Annealing | Heated above critical temperature, then slowly cooled for maximum softness. | Metals requiring high ductility for forming operations. |
Graphitizing | Converts carbon in cast iron to graphite, improving machinability. | Cast iron for enhanced mechanical properties. |
Intermediate Annealing | Restores ductility between cold-working operations. | Wires, tubes, and sheets undergoing multiple cold-forming steps. |
Isothermal Annealing | Heated to a specific temperature, held, and cooled at a controlled rate. | Steels and alloys requiring uniform microstructure. |
Process Annealing | Relieves internal stresses in cold-worked metals without altering microstructure. | Steel sheets and wires for improved formability. |
Quench Annealing | Rapid cooling after high-temperature heating for hardness and toughness. | Tool steels requiring a balance of hardness and toughness. |
Spheroidizing | Forms spheroidal carbides, improving machinability and reducing hardness. | High-carbon and tool steels for enhanced workability. |
Need help selecting the right annealing process for your materials? Contact our experts today for tailored solutions!