Electric arc furnaces (EAFs) are significantly more efficient than traditional blast furnaces, particularly in terms of energy consumption and environmental impact. According to the International Energy Agency (IEA), producing 1 tonne of steel with an EAF requires only one-tenth of the energy needed for a blast furnace. This efficiency is due to the direct heating method and the ability to recycle scrap metal, which reduces raw material consumption. However, EAFs are more expensive to operate compared to fuel-fired furnaces, and they require careful energy management to maintain efficiency. Despite these challenges, EAFs are widely used in steel recycling due to their flexibility and environmental benefits.
Key Points Explained:
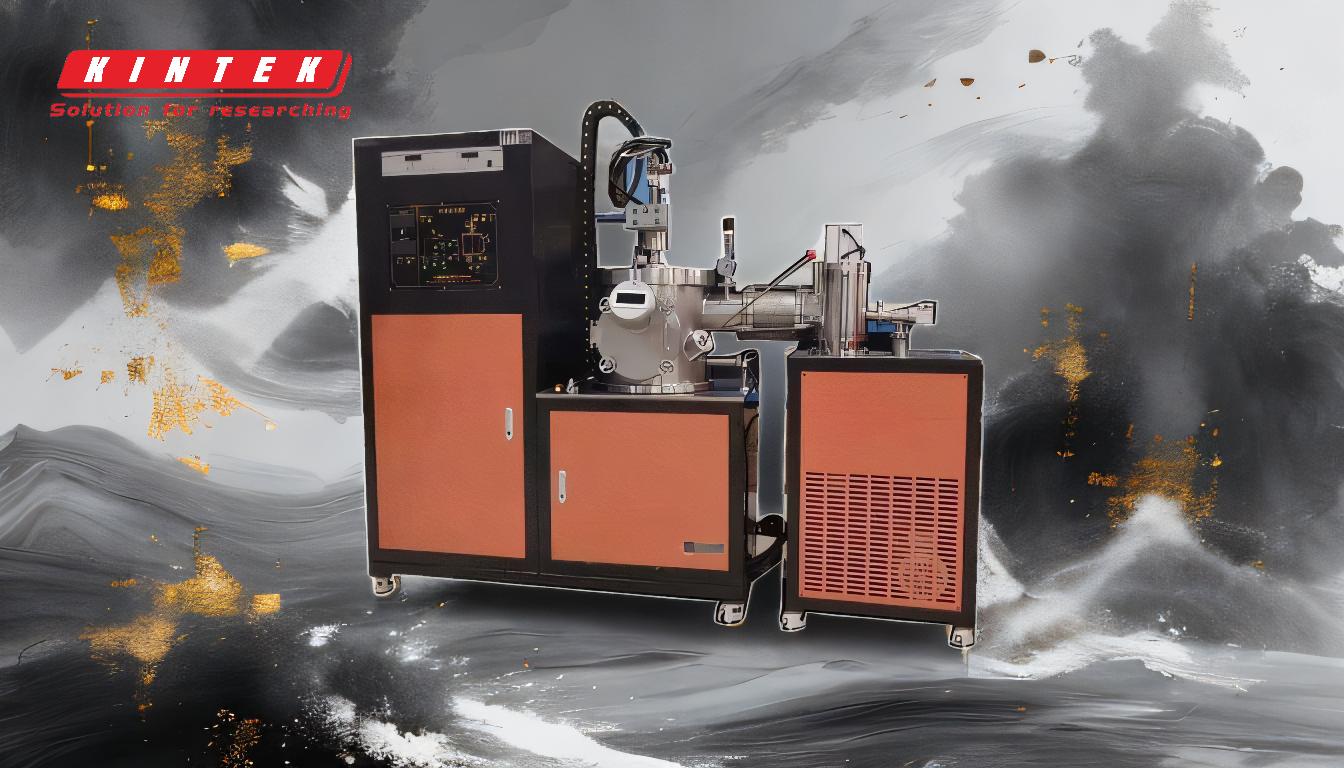
-
Energy Efficiency:
- Electric arc furnaces are highly energy-efficient compared to blast furnaces. The IEA report highlights that EAFs require only one-tenth of the energy to produce 1 tonne of steel. This is because EAFs use electricity to generate heat directly, whereas blast furnaces rely on combustion processes that are less efficient.
-
Environmental Benefits:
- EAFs do not release flue gases, making them more environmentally friendly. This is a significant advantage over blast furnaces, which emit large amounts of CO2 and other pollutants. The ability to recycle scrap metal further reduces the environmental impact by minimizing the need for raw materials.
-
Types of Electric Arc Furnaces:
- There are two main types of EAFs: direct arc furnaces and indirect arc furnaces. Direct arc furnaces allow for faster heating as the arc is struck directly between the electrode and the charge. Indirect arc furnaces transfer heat through radiation and conduction, which can be less efficient but still effective for certain applications.
-
Operational Costs:
- While EAFs are more energy-efficient, they are more expensive to operate than fuel-fired furnaces. This is due to the high cost of electricity and the need for sophisticated energy management systems to maintain efficiency.
-
Power Consumption:
- EAFs consume a significant amount of power, which can strain electrical systems. This necessitates careful planning and management of energy consumption to ensure that the furnace operates efficiently without overloading the electrical grid.
-
Flexibility and Recycling:
- One of the key advantages of EAFs is their flexibility. They can be started and stopped as needed, making them ideal for steel recycling operations. EAFs can achieve 100% scrap metal recycling, which not only reduces waste but also lowers the overall cost of steel production.
-
Comparison with Induction Furnaces:
- Induction furnaces are also more efficient than traditional open-hearth furnaces. They heat up quickly due to high-frequency power requirements, leading to higher thermal efficiency, better yield, and reduced melting time. However, EAFs are generally preferred for large-scale steel production due to their ability to handle larger volumes of material.
In summary, electric arc furnaces offer significant advantages in terms of energy efficiency, environmental impact, and flexibility. However, they come with higher operational costs and require careful management of energy consumption. These factors make EAFs a preferred choice for steel recycling and other applications where efficiency and environmental considerations are paramount.
Summary Table:
Aspect | Electric Arc Furnaces (EAFs) | Blast Furnaces |
---|---|---|
Energy Efficiency | 10x more efficient (1/10th energy per tonne of steel) | Less efficient due to combustion processes |
Environmental Impact | No flue gases, reduced CO2 emissions, and supports 100% scrap metal recycling | High CO2 emissions and pollution |
Operational Costs | Higher due to electricity costs and energy management systems | Lower operational costs compared to EAFs |
Flexibility | Can be started and stopped as needed, ideal for recycling | Less flexible, suited for continuous production |
Power Consumption | High power consumption, requires careful energy management | Lower power consumption but less efficient overall |
Ready to explore how electric arc furnaces can transform your steel production? Contact us today for expert advice!