Physical vapor deposition (PVD) is a process used to deposit thin films of material onto a substrate. It involves the transformation of a solid material into a vapor phase, which then condenses onto the substrate to form a thin film. The process typically consists of four main steps: excitation of the material to form a vapor, introduction of a reactive gas, formation of a compound between the vapor and the gas, and deposition of the compound onto the substrate. This method is widely used in various industries, including electronics, optics, and coatings, due to its ability to produce high-quality, durable films.
Key Points Explained:
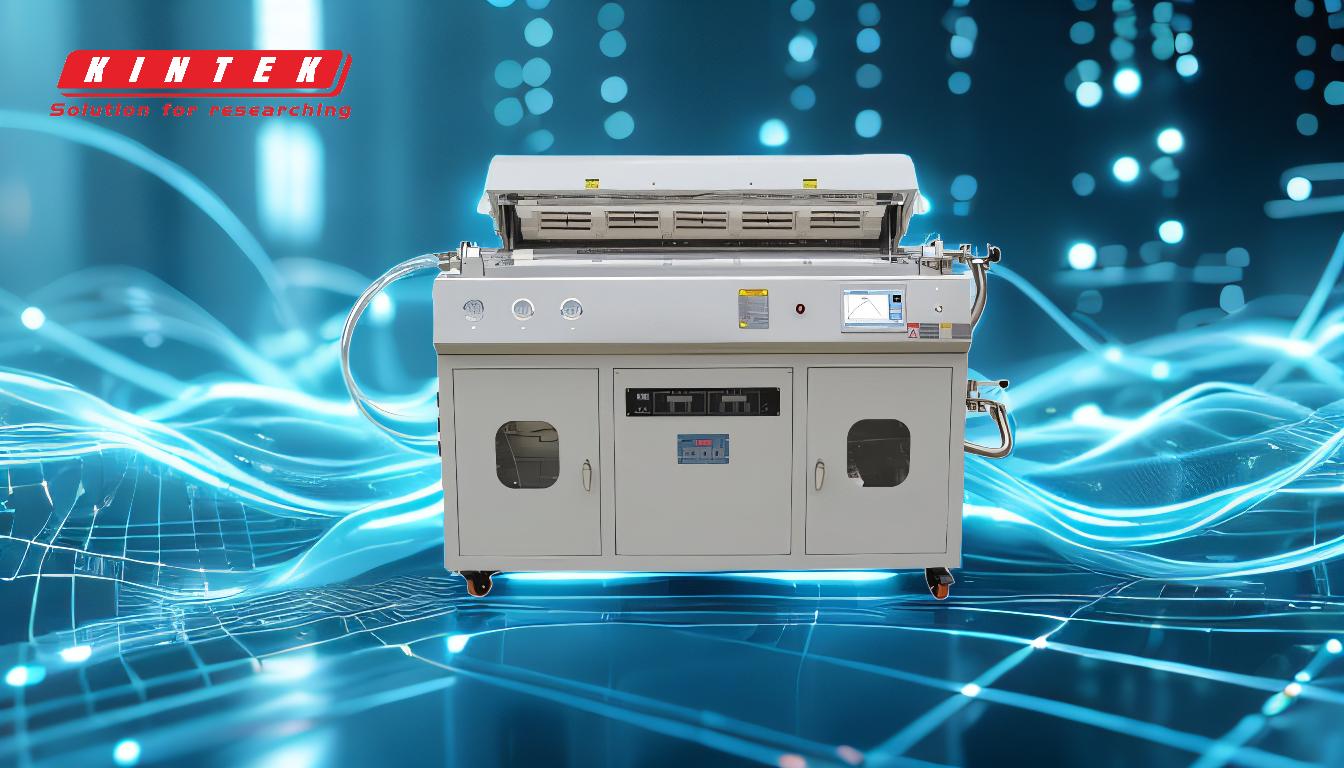
-
Excitation of the Material to Form a Vapor:
- The first step in the PVD process involves the excitation of the material to be deposited. This is typically achieved through the use of a high-energy plasma, which heats the material to a point where it vaporizes. The plasma can be generated using various methods, such as sputtering or arc evaporation. The vaporized material is then ready to be transported to the substrate.
-
Introduction of a Reactive Gas:
- Once the material is in the vapor phase, a reactive gas is introduced into the chamber. This gas is chosen based on the desired properties of the final film. For example, if a nitride film is desired, nitrogen gas might be used. The reactive gas interacts with the vaporized material to form a compound.
-
Formation of a Compound:
- The reactive gas reacts with the vaporized material to form a compound. This compound is typically in the form of a solid, which is then ready to be deposited onto the substrate. The specific compound formed depends on the materials and gases used in the process.
-
Deposition of the Compound onto the Substrate:
- The final step in the PVD process is the deposition of the compound onto the substrate. This is typically achieved through condensation, where the vaporized compound cools and solidifies on the substrate surface. The result is a thin, uniform film that adheres strongly to the substrate. The properties of the film, such as its thickness, composition, and structure, can be controlled by adjusting the process parameters, such as the temperature, pressure, and gas flow rates.
-
Comparison with Chemical Vapor Deposition (CVD):
- While PVD and CVD are both used to deposit thin films, they differ in the way the material is transported to the substrate. In CVD, the material is transported in the form of a gas, which then reacts on the substrate surface to form a solid film. In contrast, PVD involves the direct vaporization of a solid material, which then condenses onto the substrate. This difference in the transport mechanism can lead to differences in the properties of the deposited films, such as their purity, density, and adhesion.
-
Applications of PVD:
- PVD is used in a wide range of applications, including the deposition of wear-resistant coatings on cutting tools, decorative coatings on consumer goods, and functional coatings on electronic components. The ability to control the properties of the deposited film makes PVD a versatile and valuable process in many industries.
By following these steps and understanding the key principles behind PVD, one can effectively deposit high-quality thin films for various applications. The process requires careful control of the deposition conditions to ensure the desired film properties are achieved.
Summary Table:
Step | Description |
---|---|
1. Excitation | Vaporize solid material using high-energy plasma (e.g., sputtering or arc evaporation). |
2. Reactive Gas Introduction | Introduce a reactive gas (e.g., nitrogen) to form a compound with the vapor. |
3. Compound Formation | React the vaporized material with the gas to form a solid compound. |
4. Deposition | Condense the compound onto the substrate to form a thin, uniform film. |
Applications | Wear-resistant coatings, decorative coatings, and functional electronic films. |
Ready to explore PVD for your applications? Contact our experts today to get started!