Brazing and welding are both effective methods for joining aluminum, but they differ significantly in terms of strength, process, and application. While aluminum brazing uses a filler metal to bond components without melting the base material, welding involves melting the base metals to create a fusion joint. Brazed joints are strong and often comparable to the base metals, but they are generally not as strong as welded joints, which achieve a metallurgical bond. The choice between brazing and welding depends on factors like the application, required strength, and material properties.
Key Points Explained:
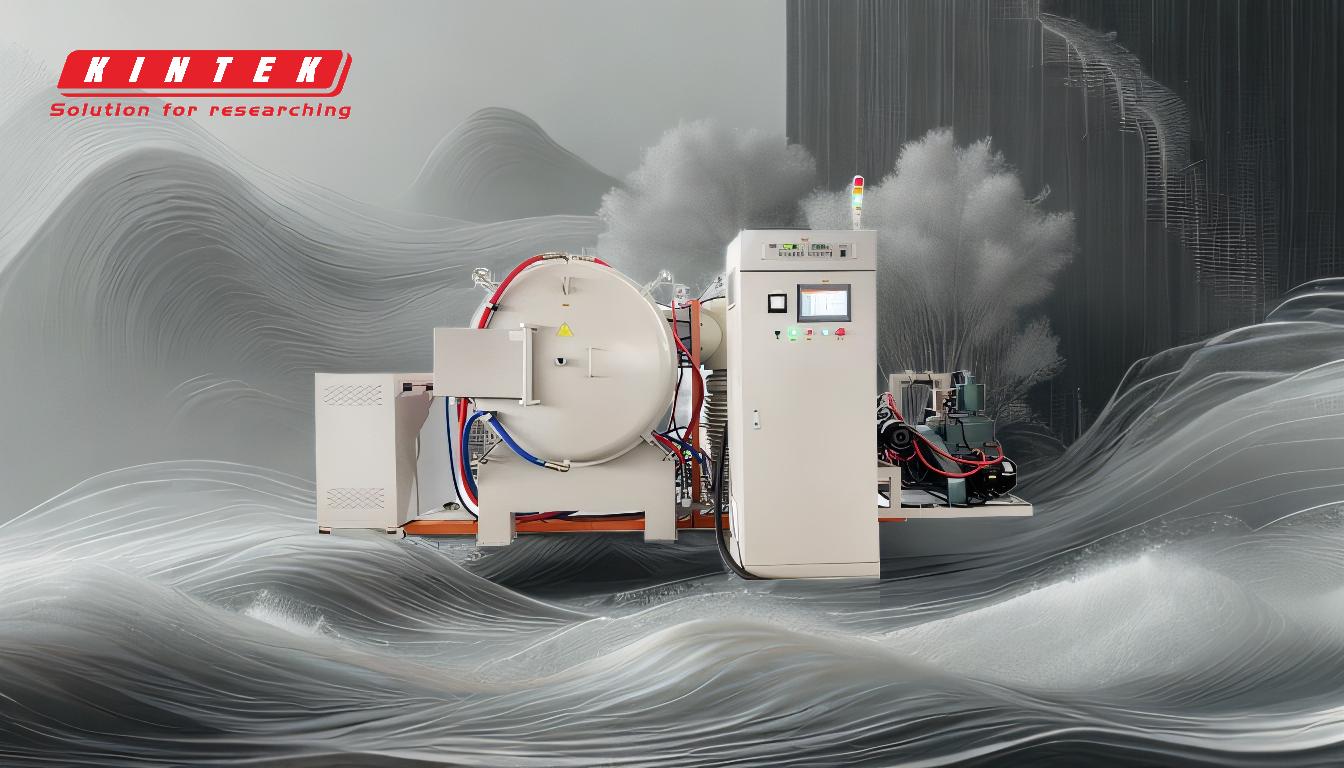
-
Definition and Process Differences:
- Brazing: Brazing involves using a filler metal with a melting point above 840°F to join aluminum components without melting the base material. The filler metal flows into the joint by capillary action, creating a strong bond.
- Welding: Welding melts the base metals to form a fusion joint, creating a metallurgical bond that is typically stronger than brazed joints.
-
Strength Comparison:
- Brazed joints are strong and can often match the strength of the base metals, but they are generally not as strong as welded joints. Welded joints achieve a deeper and more integral bond due to the fusion of the base materials.
-
Applications and Suitability:
- Brazing: Preferred in industries like cookware, automotive, and HVAC systems where high strength is not the primary requirement, and the process is less likely to distort thin or delicate components.
- Welding: Used in applications requiring maximum strength, such as structural components, aerospace, and heavy machinery.
-
Advantages of Brazing:
- Lower thermal distortion compared to welding.
- Suitable for joining dissimilar metals.
- Easier to automate and control in mass production.
-
Advantages of Welding:
- Higher joint strength due to metallurgical bonding.
- Better suited for high-stress applications.
- Can be used for thicker materials.
-
Key Considerations for Choice:
- Strength Requirements: If maximum strength is needed, welding is the better choice.
- Material Thickness: Welding is more suitable for thicker materials, while brazing works well for thinner or delicate parts.
- Production Environment: Brazing is often preferred for high-volume production due to its ease of automation.
In summary, while aluminum brazing provides strong and reliable joints, it is generally not as strong as aluminum welding. The choice between the two methods depends on the specific requirements of the application, including strength, material properties, and production considerations.
Summary Table:
Aspect | Brazing | Welding |
---|---|---|
Process | Uses filler metal without melting base material | Melts base metals to create a fusion joint |
Joint Strength | Strong, often matches base metals but generally weaker than welding | Stronger due to metallurgical bonding |
Applications | Cookware, automotive, HVAC systems | Structural components, aerospace, heavy machinery |
Advantages | Lower thermal distortion, suitable for dissimilar metals, easy automation | Higher joint strength, better for high-stress applications, thicker materials |
Key Considerations | Strength requirements, material thickness, production environment | Strength requirements, material thickness, production environment |
Need help deciding between brazing and welding for your aluminum projects? Contact our experts today for personalized advice!