Calcination is not typically done in a blast furnace. Instead, it is primarily carried out in specialized furnaces like reverberatory furnaces or rotary kilns, which are designed to provide controlled heating conditions below the melting point of the material. Calcination involves heating materials in the absence or limited supply of air to induce thermal decomposition, remove volatile substances, or cause phase transitions. While small-scale roasting, which requires minimal oxygen, can occur in a blast furnace, calcination is distinct and usually requires different equipment. The blast furnace is more commonly associated with smelting processes, where high temperatures and specific chemical reactions are used to extract metals from ores.
Key Points Explained:
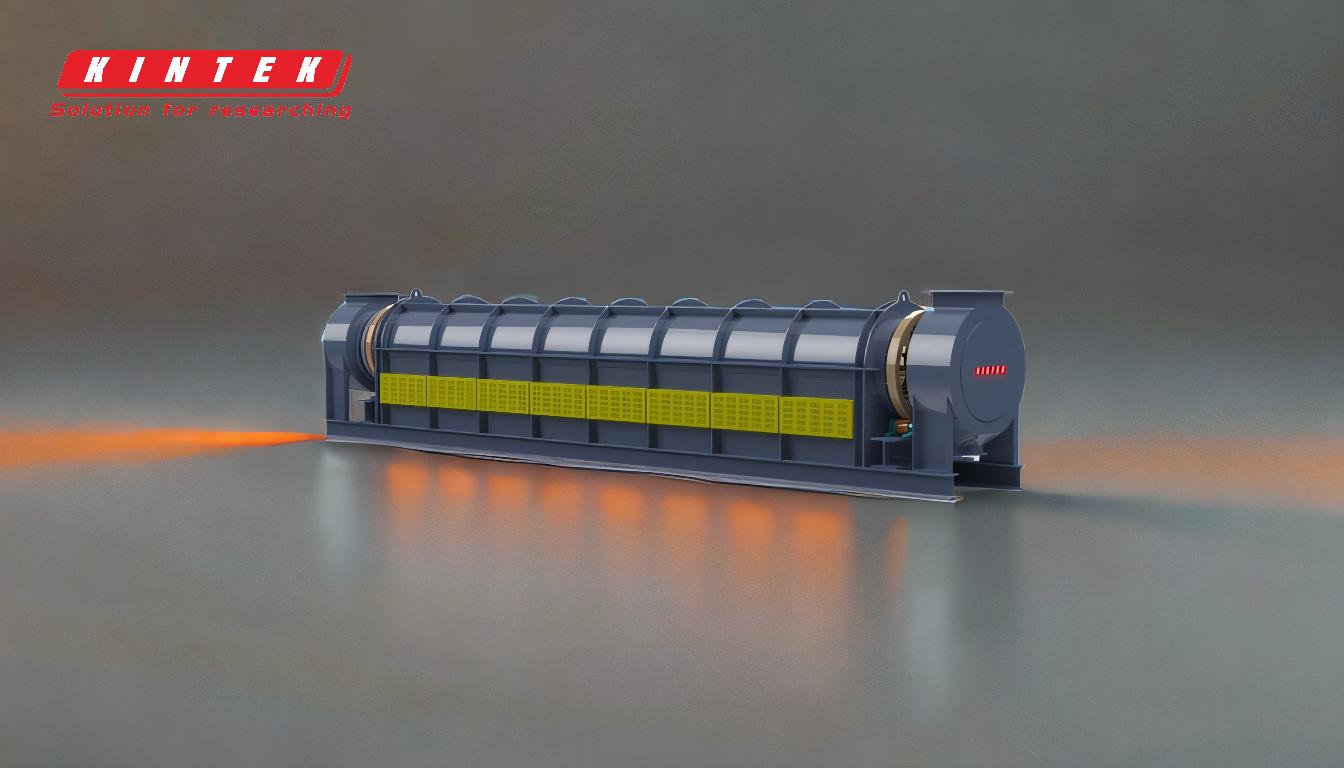
-
Definition of Calcination:
- Calcination is a heat treatment process that involves heating solid materials, such as ores, below their melting point in the absence or limited supply of air or oxygen. This process induces thermal decomposition, removes volatile fractions, or causes phase transitions.
-
Typical Equipment for Calcination:
- Calcination is usually performed in specialized equipment like reverberatory furnaces or rotary kilns. These furnaces are designed to provide controlled heating conditions and are suitable for processes requiring precise temperature regulation.
- Reverberatory furnaces, for example, have a horizontal 'S' shape and can operate with or without oxygen, depending on the specific requirements of the process.
-
Blast Furnace and Calcination:
- A blast furnace is primarily used for smelting, a process that involves high temperatures and chemical reactions to extract metals from ores. It is not typically used for calcination.
- While small-scale roasting (a process similar to calcination but requiring minimal oxygen) can occur in a blast furnace, calcination itself is distinct and generally requires different equipment.
-
Purpose of Calcination:
- The primary purpose of calcination is to remove volatile impurities or induce chemical dissociation in materials. For example, in the production of lime from limestone, calcination drives off carbon dioxide, leaving behind lime in a powdered form.
-
Examples of Calcination:
- A classic example of calcination is the conversion of limestone (CaCO₃) to lime (CaO). When limestone is heated, it undergoes thermal decomposition, releasing carbon dioxide (CO₂) and forming lime.
- Other materials, such as dolomite and magnesite, are also calcined to achieve specific chemical or physical properties.
-
Rotary Kilns for Calcination:
- Rotary kilns are commonly used for calcination, especially for materials with particle sizes of 60 mm or less. These kilns provide uniform heating and are efficient for producing high-quality, consistent products.
-
Contrast with Roasting:
- Roasting is a similar process but typically involves heating ores in the presence of excess air or oxygen. It is often used to oxidize sulfide ores, whereas calcination focuses on thermal decomposition or the removal of volatile substances.
-
Key Differences Between Calcination and Blast Furnace Processes:
- Calcination is a thermal decomposition process that occurs below the melting point of the material, while blast furnace processes involve smelting, which occurs at much higher temperatures and often involves chemical reduction.
- Calcination is typically carried out in reverberatory furnaces or rotary kilns, whereas blast furnaces are used for iron production and other metal extraction processes.
In summary, calcination is not performed in a blast furnace. Instead, it is conducted in specialized equipment designed for controlled heating and thermal decomposition. The blast furnace is reserved for smelting and other high-temperature processes, making it unsuitable for the precise requirements of calcination.
Summary Table:
Key Point | Details |
---|---|
Definition of Calcination | Thermal decomposition below melting point, often in absence of air/oxygen. |
Typical Equipment | Reverberatory furnaces, rotary kilns. |
Blast Furnace Use | Primarily for smelting, not calcination. |
Purpose of Calcination | Remove volatile impurities or induce chemical dissociation. |
Example | Conversion of limestone (CaCO₃) to lime (CaO). |
Rotary Kilns | Ideal for uniform heating of materials ≤60 mm. |
Contrast with Roasting | Roasting uses excess air; calcination focuses on thermal decomposition. |
Need the right furnace for your calcination process? Contact our experts today to find the perfect solution!