PVD (Physical Vapor Deposition) coatings can indeed be shiny, depending on the specific material and process used. These coatings are known for their ability to replicate the original finish of materials with minimal effort, often resulting in a metallic luster that does not require additional polishing. The reflectivity and shine of PVD coatings are influenced by factors such as the substrate material, coating thickness, and the specific PVD technology employed. While PVD coatings are primarily valued for their functional properties like hardness, wear resistance, and corrosion resistance, their aesthetic qualities, including shine, make them suitable for applications where appearance is important.
Key Points Explained:
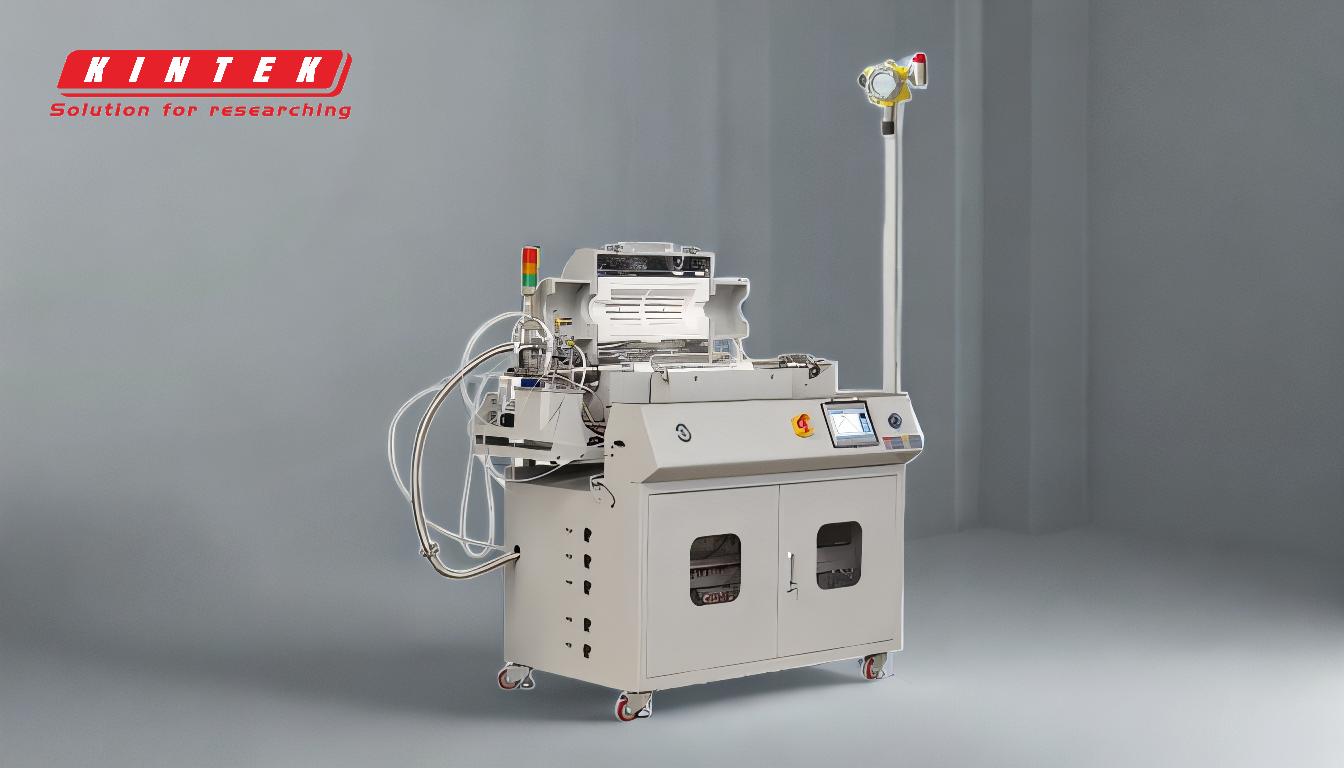
-
Shininess of PVD Coatings:
- PVD coatings can produce a shiny, metallic luster depending on the material and process used.
- The coatings reflect the surface of the substrate well, often eliminating the need for additional polishing to achieve a good finish.
- The shine is a result of the high purity and uniformity of the coating, which enhances the reflective properties of the surface.
-
Factors Influencing Shine:
- Substrate Material: The underlying material plays a significant role in determining the final appearance of the coating. For example, coatings on metals like stainless steel or titanium tend to have a more pronounced shine.
- Coating Thickness: PVD coatings are extremely thin (0.5–5 μm), but their uniformity and adhesion contribute to a consistent and reflective surface.
- PVD Technology: Different PVD methods (e.g., sputtering, evaporation) can influence the texture and reflectivity of the coating. Some technologies are better suited for achieving a high-gloss finish.
-
Aesthetic and Functional Balance:
- While PVD coatings are often chosen for their functional properties (e.g., hardness, wear resistance, corrosion resistance), their ability to enhance the appearance of a product is an added benefit.
- The adjustability of product appearance through PVD coatings makes them suitable for industries where both performance and aesthetics are important, such as automotive, jewelry, and consumer electronics.
-
Limitations in Shine:
- PVD coatings may have limitations in achieving uniform shine on complex geometries, such as the back and sides of tools, due to low air pressure during the deposition process.
- The shine is also influenced by the cleaning requirements of the substrate. High cleaning standards are necessary to ensure optimal adhesion and reflectivity.
-
Applications of Shiny PVD Coatings:
- Automotive: Used for decorative trims and functional components like engine parts, where a combination of durability and appearance is required.
- Jewelry: PVD coatings are applied to create scratch-resistant, shiny finishes on watches, rings, and other accessories.
- Consumer Electronics: Used for smartphone casings, laptop exteriors, and other devices to provide a durable, reflective surface.
In summary, PVD coatings are capable of producing a shiny, reflective finish, making them suitable for applications where both functionality and aesthetics are important. The shine is influenced by factors such as the substrate material, coating thickness, and PVD technology, and while there are some limitations, the overall aesthetic quality of PVD coatings is a significant advantage in many industries.
Summary Table:
Aspect | Details |
---|---|
Shininess | PVD coatings produce a metallic luster, often eliminating the need for polishing. |
Factors Influencing Shine | Substrate material, coating thickness, and PVD technology. |
Aesthetic Applications | Automotive trims, jewelry, and consumer electronics. |
Functional Benefits | Hardness, wear resistance, and corrosion resistance. |
Limitations | Uniform shine may be challenging on complex geometries. |
Explore how PVD coatings can enhance your product's appearance and performance—contact us today!