Quenching and annealing are two distinct heat treatment processes used in metallurgy, each with specific purposes and methodologies. Quenching involves rapidly cooling a metal workpiece to achieve certain mechanical properties, such as increased hardness, while annealing involves heating and then slowly cooling the metal to relieve internal stresses, improve ductility, and refine the grain structure. Quenching is not part of annealing; rather, they are separate processes that can be used sequentially or independently depending on the desired outcome for the metal.
Key Points Explained:
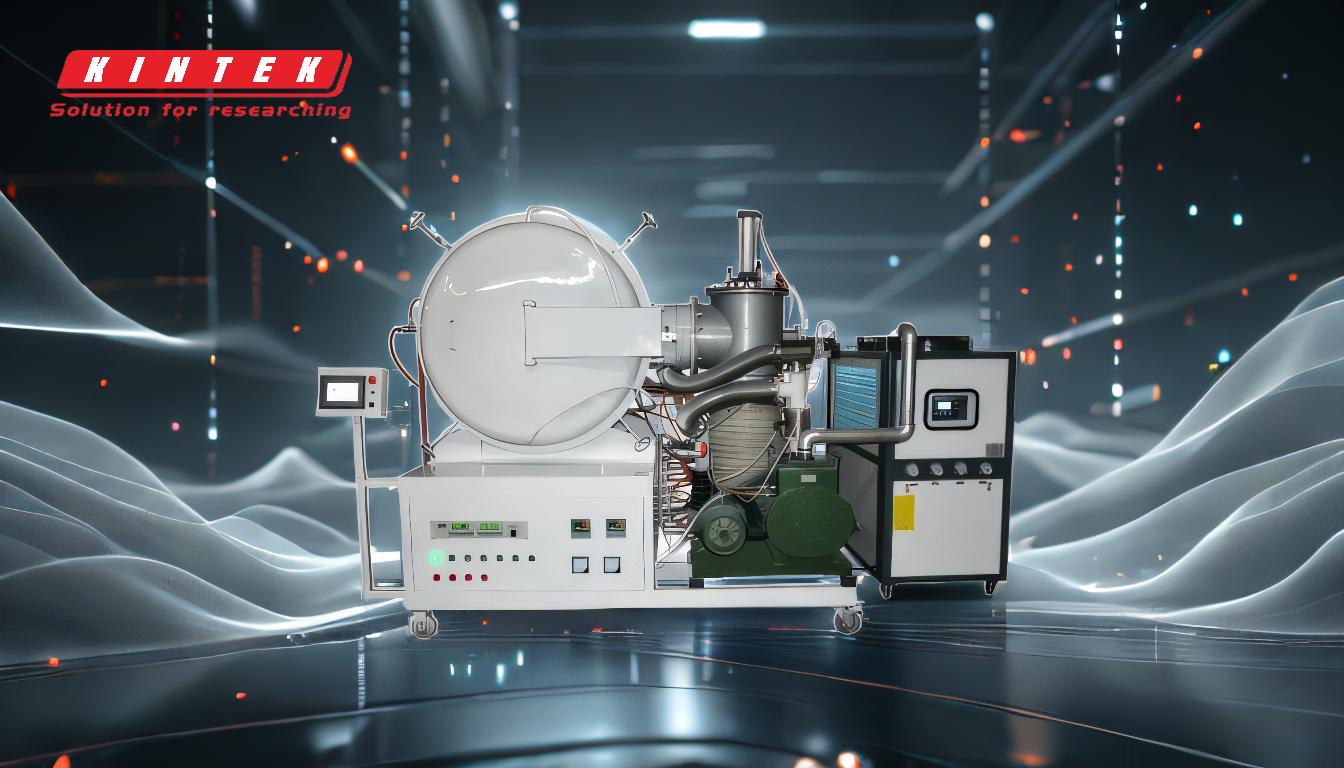
-
Definition of Quenching:
- Quenching is a heat treatment process where a metal workpiece is heated to a specific temperature and then rapidly cooled, typically by immersing it in a liquid medium such as water, oil, or polymer. This rapid cooling locks the metal's microstructure in a hardened state, increasing its hardness and strength. However, quenching can also make the metal more brittle.
-
Definition of Annealing:
- Annealing is a heat treatment process that involves heating a metal to a specific temperature, holding it at that temperature for a period, and then allowing it to cool slowly, usually in the furnace or in air. The purpose of annealing is to soften the metal, improve its ductility, and reduce internal stresses, making it easier to machine or form.
-
Purpose of Quenching vs. Annealing:
- Quenching: The primary goal is to increase the hardness and strength of the metal. It is often used after heating the metal to a high temperature (austenitizing) to transform its microstructure into a harder form (martensite).
- Annealing: The primary goal is to soften the metal, improve its ductility, and relieve internal stresses. It is often used to make the metal more workable or to prepare it for further processing.
-
Cooling Rates:
- Quenching: Involves rapid cooling, which is essential to achieve the desired hardness. The cooling rate is critical and must be controlled to avoid cracking or distortion.
- Annealing: Involves slow cooling, which allows the metal to achieve a more stable and softer microstructure. The slow cooling rate is key to achieving the desired properties.
-
Sequential Use of Quenching and Annealing:
- In some cases, quenching and annealing can be used sequentially. For example, a metal might be quenched to achieve high hardness and then annealed to reduce brittleness and improve toughness. This combination is often used in processes like tempering, where the metal is quenched and then reheated to a lower temperature to achieve a balance between hardness and ductility.
-
Equipment and Process Differences:
- Quenching: Requires a quenching medium (e.g., water, oil) and often involves moving the workpiece quickly from the furnace to the quenching tank. The process is rapid and requires precise control of cooling rates.
- Annealing: Typically involves slow cooling within the furnace or in still air. The process is slower and more controlled, with the focus on achieving a uniform temperature and cooling rate.
-
Microstructural Changes:
- Quenching: Results in a transformation of the metal's microstructure to martensite, which is hard but brittle.
- Annealing: Results in a more refined and uniform grain structure, which is softer and more ductile.
In summary, quenching and annealing are complementary but distinct processes in metallurgy. Quenching is not part of annealing; rather, they serve different purposes and are used based on the desired properties of the metal. Understanding the differences between these processes is crucial for selecting the appropriate heat treatment method for a given application.
Summary Table:
Aspect | Quenching | Annealing |
---|---|---|
Purpose | Increases hardness and strength | Softens metal, improves ductility, and relieves internal stresses |
Cooling Rate | Rapid cooling (e.g., water, oil) | Slow cooling (e.g., in furnace or air) |
Microstructure | Transforms to martensite (hard but brittle) | Refines grain structure (soft and ductile) |
Equipment | Requires quenching medium and rapid transfer | Typically involves furnace cooling or air cooling |
Sequential Use | Often followed by tempering to balance hardness and ductility | Used independently or to prepare metal for further processing |
Need expert advice on heat treatment processes? Contact us today to enhance your metallurgical outcomes!