Atmosphere furnaces are specialized heating devices designed for applications requiring precise thermal control and protection from oxidation or contamination. They are widely used in industries like metallurgy, materials science, and research laboratories. These furnaces create a controlled environment by introducing specific gases (e.g., hydrogen, nitrogen, argon) or maintaining a vacuum, ensuring that the materials being processed are not exposed to unwanted chemical reactions. Key components include heating chambers, temperature control systems, and gas supply mechanisms. Atmosphere furnaces are ideal for processes like annealing, tempering, and hardening, offering uniform heating, rapid cooling, and clean finishes. They are robust, versatile, and capable of handling large-scale manufacturing and experimentation.
Key Points Explained:
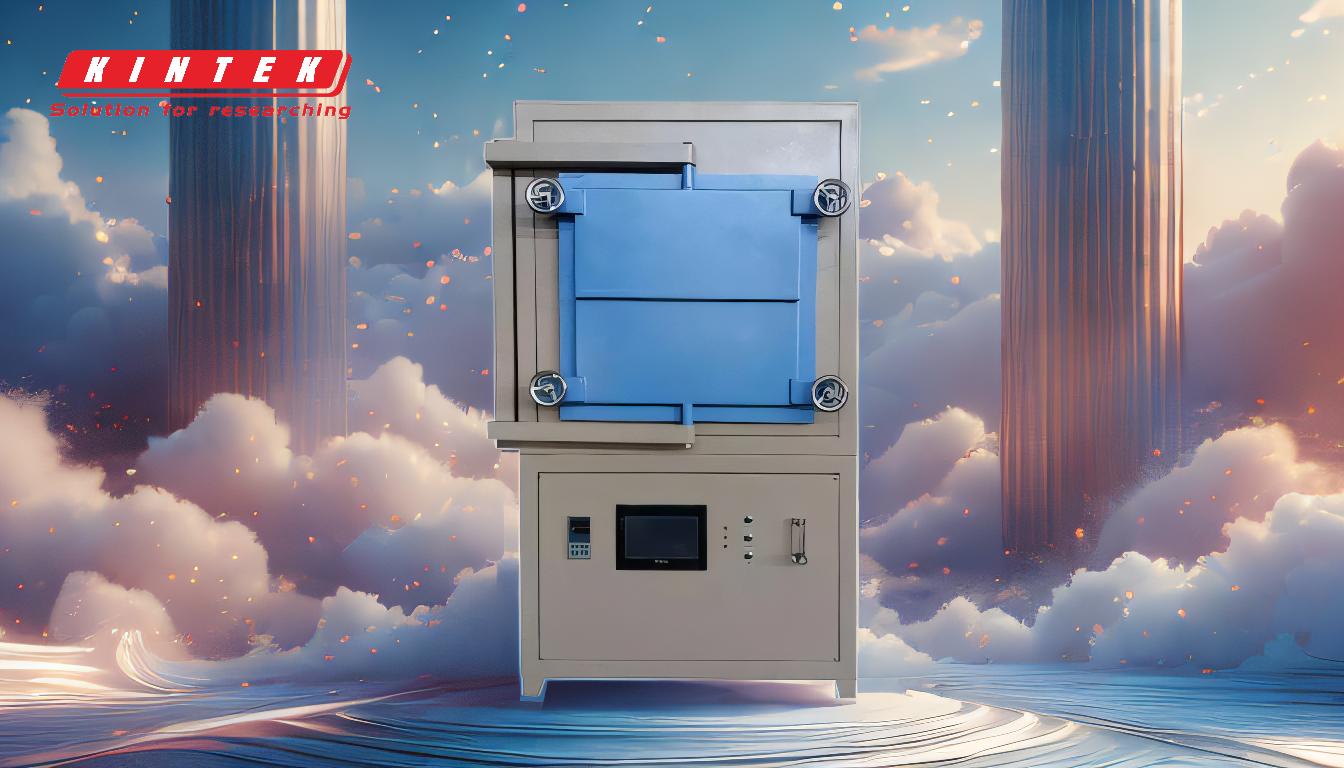
-
Definition and Purpose of Atmosphere Furnaces:
- Atmosphere furnaces are designed to provide precise heating and thermal control while protecting materials from oxidation or contamination.
- They are used in applications where maintaining a specific environment (e.g., inert, reactive, or vacuum) is critical for achieving desired material properties.
- Common industries include metallurgy, materials science, and research laboratories.
-
Key Components:
- Heating Chamber: Constructed with high-temperature-resistant materials to withstand extreme heat.
- Heating Elements: Use electric resistance heaters or gas burners to generate and distribute heat uniformly.
- Temperature Control System: Monitors and regulates heat to ensure consistent thermal homogeneity.
- Gas Supply System: Introduces controlled atmospheres (e.g., hydrogen, nitrogen, argon) into the furnace.
- Atmosphere Control System: Governs the precise composition of gases within the furnace to create the desired environment.
-
Types of Atmospheres:
- Inert Atmospheres: Use gases like nitrogen, argon, or helium to prevent oxidation and contamination.
- Reactive Atmospheres: Use gases like hydrogen to facilitate specific chemical reactions during processing.
- Vacuum Atmospheres: Maintain low pressure (down to 1 Torr) to eliminate air and prevent unwanted reactions.
-
Applications:
- Metallurgy: Used for annealing, tempering, and hardening metals to enhance mechanical properties and eliminate impurities.
- Materials Science: Ideal for processing materials that require clean finishes and precise thermal control.
- Research and Development: Suitable for large-scale sample manufacturing and experimentation with varying atmospheric requirements.
-
Key Features:
- Uniform Heating: Ensures consistent thermal distribution across the workload.
- Rapid Heating and Cooling: Enhances processing efficiency and material quality.
- High-Purity Environments: Reduces oxidation and contamination, especially in hydrogen atmosphere furnaces.
- Robust Construction: Features double-shell chambers, fan cooling, and high-temperature-resistant seals for durability and safety.
- Digital PID Controllers: Provide higher temperature accuracy and user-friendly operation.
-
Advantages:
- Precision: Offers full control over thermal process parameters for optimal results.
- Versatility: Capable of handling a wide range of materials and processes.
- Durability: Long service life heating elements and rugged construction ensure reliable performance even at constant high temperatures.
- Sealing and Vacuum Capabilities: High-temperature-resistant seals and vacuum systems enhance environmental control.
-
Comparison with Other Furnaces:
- Box Furnaces: Atmosphere furnaces share similarities but offer additional atmospheric control features.
- Tube Furnaces: While tube furnaces provide better vacuum effects, atmosphere furnaces are more versatile for large-scale applications and varied atmospheric requirements.
In summary, atmosphere furnaces are essential tools for industries and research requiring precise thermal processing in controlled environments. Their ability to create inert, reactive, or vacuum atmospheres makes them indispensable for applications like metallurgy, materials science, and large-scale experimentation. With features like uniform heating, rapid cooling, and robust construction, they ensure high-quality results and long-term reliability.
Summary Table:
Aspect | Details |
---|---|
Purpose | Precise heating and oxidation/contamination protection in controlled environments. |
Key Components | Heating chamber, heating elements, temperature control, gas supply system. |
Types of Atmospheres | Inert (nitrogen, argon), reactive (hydrogen), vacuum (down to 1 Torr). |
Applications | Metallurgy (annealing, tempering), materials science, R&D experimentation. |
Key Features | Uniform heating, rapid cooling, high-purity environments, robust construction. |
Advantages | Precision, versatility, durability, sealing, and vacuum capabilities. |
Ready to enhance your thermal processing? Contact us today to find the perfect atmosphere furnace for your needs!