Batch furnaces are closed-process machines designed for heat-treating a batch of components at a time. They are well-suited for cleanroom standards, inert atmosphere applications, and processes requiring precise control over temperature and atmosphere. Unlike continuous furnaces, batch furnaces process multiple components simultaneously, making them ideal for low-volume production, large-sized parts, or specialized heat treatments like deep case carburizing. They are less complex, easier to maintain, and cost-effective compared to continuous furnaces. However, they require fixtures like baskets or racks for loading and involve more manual handling. Common applications include annealing, hardening, sintering, and atmosphere processing, making them versatile tools in both industrial and laboratory settings.
Key Points Explained:
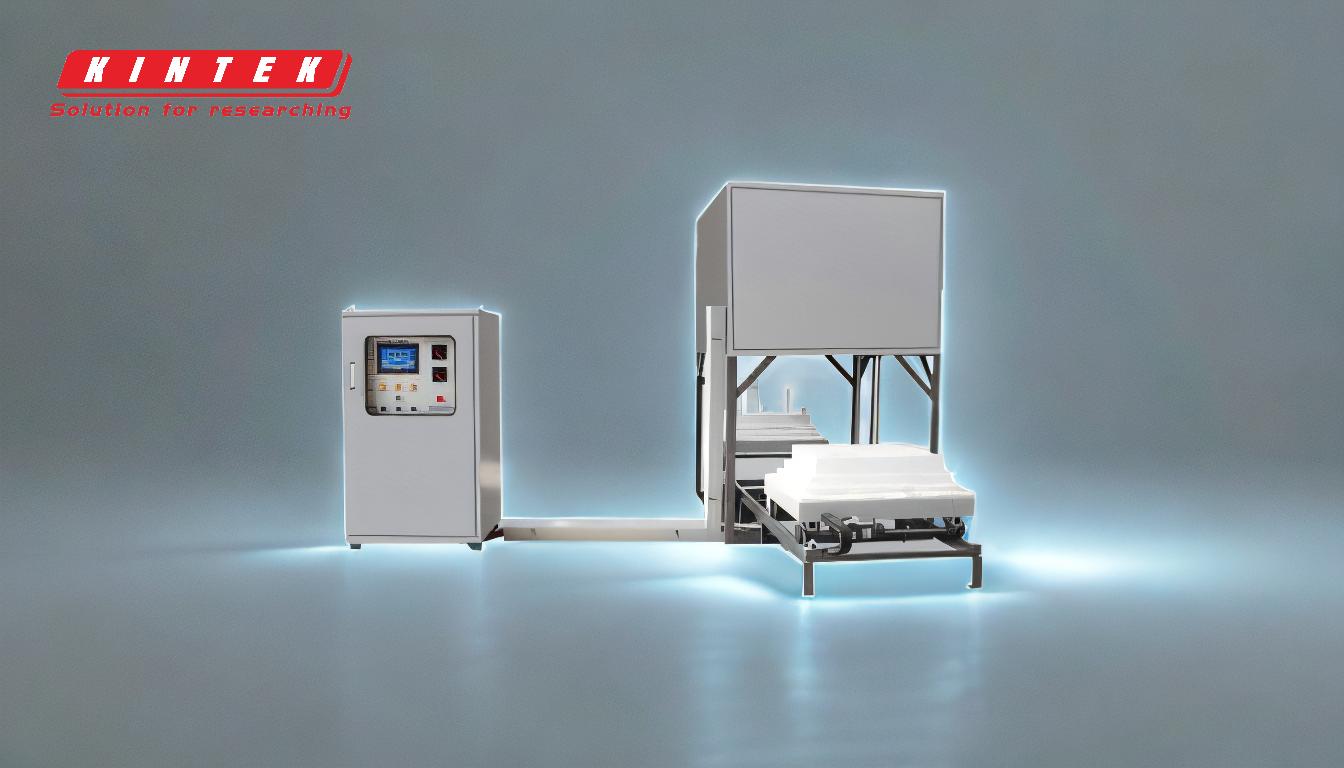
-
Definition and Operation of Batch Furnaces:
- Batch furnaces are closed-process machines that heat-treat components in batches rather than continuously.
- They operate by charging and discharging the workload as a single unit or batch, ensuring a sealed environment during the heating process.
- This design makes them suitable for cleanroom standards and inert atmosphere applications, where contamination must be minimized.
-
Comparison with Continuous Furnaces:
- Batch Furnaces: Process multiple components at once, making them ideal for low-volume production, large parts, or specialized treatments. They are less complex, easier to maintain, and cost-effective.
- Continuous Furnaces: Operate at a constant temperature, with items moving through the furnace at a constant speed. They are more complex, expensive, and require frequent maintenance but are energy-efficient for high-volume production.
-
Applications of Batch Furnaces:
- Industrial Applications: Used for processes like annealing, hardening, sintering, tempering, and atmosphere processing. They are also suitable for aging, baking, brazing, curing, drying, and heat treatment of metals.
- Laboratory Applications: Versatile tools for annealing, solvent removal, sterilizing, evaporation, polymer curing, and polyimide baking.
-
Advantages of Batch Furnaces:
- Cost-Effectiveness: Lower initial and maintenance costs compared to continuous furnaces.
- Flexibility: Can handle varying batch sizes, part weights, and heat treatment requirements.
- Precision: Ideal for processes requiring controlled atmospheres and precise temperature management.
-
Limitations of Batch Furnaces:
- Manual Handling: Requires fixtures like baskets or racks for loading, increasing manual labor.
- Work-in-Process: More effort is needed to organize batches for loading compared to continuous furnaces.
-
Technical Operation:
- The furnace heats from room temperature to a predetermined maximum temperature at a specified rate.
- It holds the temperature for a specified time and then cools at a controlled rate.
- Each batch can differ in weight, size, material grade, and heat treatment requirements, offering flexibility in processing.
-
Suitability for Specific Tasks:
- Ideal for low-volume production, large or heavy parts, and specialized heat treatments like deep case carburizing.
- Can operate with or without a controlled atmosphere, depending on the application.
-
Versatility in Industrial and Laboratory Settings:
- Used in both industrial and laboratory environments for a wide range of thermal processing tasks.
- Suitable for research, testing, and production applications requiring precise thermal control.
By understanding these key points, a purchaser can evaluate whether a batch furnace is the right choice for their specific needs, considering factors like production volume, part size, and required heat treatment processes.
Summary Table:
Feature | Batch Furnaces | Continuous Furnaces |
---|---|---|
Operation | Heat-treats components in batches | Operates continuously with items moving at a constant speed |
Suitability | Ideal for low-volume production, large parts, and specialized treatments | Best for high-volume production |
Complexity | Less complex, easier to maintain | More complex, requires frequent maintenance |
Cost | Cost-effective with lower initial and maintenance costs | Higher initial and maintenance costs |
Applications | Annealing, hardening, sintering, tempering, and atmosphere processing | High-volume industrial processes |
Manual Handling | Requires fixtures like baskets or racks, increasing manual labor | Minimal manual handling |
Ready to enhance your heat treatment process? Contact us today to find the perfect batch furnace for your needs!