Sintering is a versatile manufacturing process used to create high-density, strong, and durable products by compacting and heating materials below their melting points. It is widely applied in industries such as automotive, aerospace, electronics, and filtration. Sintered products include metals, ceramics, plastics, and composites, and they are used for components like gears, bearings, electrical contacts, and filters. The process is particularly beneficial for materials with high melting points and for producing custom shapes using modern techniques like 3D printing. Sintering enhances material properties such as strength, density, and wear resistance, making it indispensable in advanced manufacturing.
Key Points Explained:
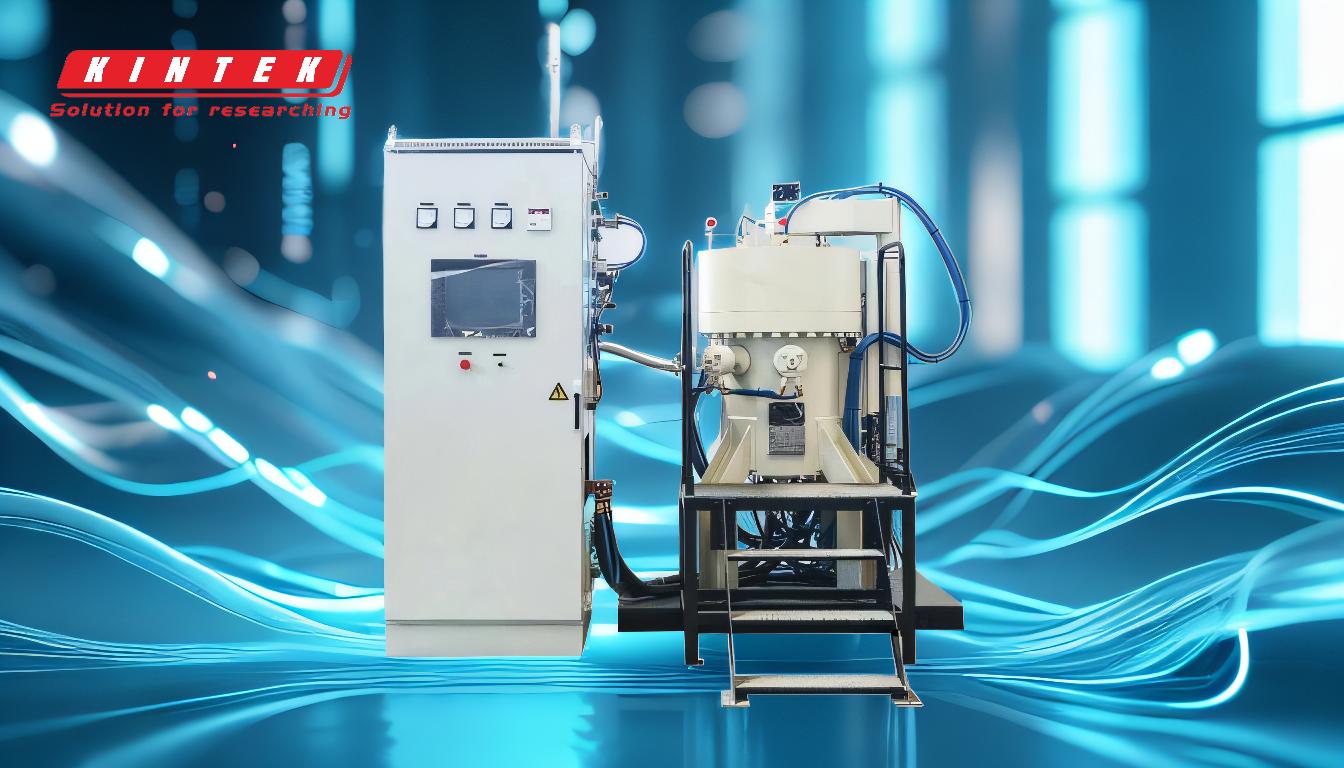
-
Definition and Process of Sintering:
- Sintering involves compacting powdered materials into a "green body" and heating them at high temperatures below their melting points. This process bonds particles together, reducing porosity and increasing density and strength.
- The two main methods are cold pressing followed by sintering and hot pressing sintering, each suited for specific materials and applications.
-
Applications in Metal Products:
- Sintered metals are used in a wide range of industrial components, including:
- Armatures: Found in motors and generators.
- Bearing retainers: Used to maintain bearing alignment.
- Brackets: Structural supports in machinery.
- Cams and gears: Essential for mechanical motion control.
- Electrical contacts: Critical for conductivity in electronic devices.
- These components benefit from the enhanced strength, wear resistance, and dimensional stability provided by sintering.
- Sintered metals are used in a wide range of industrial components, including:
-
Applications in Ceramics and Glass:
- Sintering is crucial for producing ceramics, porcelain, and glass with high strength and low porosity.
- Modern techniques like isostatic pressing, slipcasting, and tapecasting are used to create green bodies for sintering, enabling complex shapes and high precision.
-
Applications in Filtration and Plastics:
- Sintered materials are used in filters (e.g., pe filters) for their controlled porosity and durability.
- Sintered plastics are employed in applications requiring lightweight, strong, and wear-resistant components.
-
Advantages of Sintering:
- Cost-effective: Sintering uses less energy compared to melting processes.
- Customizability: Enables the production of complex shapes and custom designs, especially with 3D printing.
- Material versatility: Suitable for metals, ceramics, and composites with high melting points.
-
Modern Techniques and Innovations:
- 3D printing: Combines sintering with additive manufacturing to create custom metal forms and intricate designs.
- Isostatic pressing: Ensures uniform density and strength in sintered products.
- Extruding and tapecasting: Used for producing green bodies with precise dimensions.
-
Industrial Significance:
- Sintering is indispensable in industries like automotive (bearings, gears), aerospace (lightweight components), and electronics (contacts, insulators).
- Its ability to enhance material properties makes it a cornerstone of advanced manufacturing.
By leveraging sintering, manufacturers can produce high-performance, durable, and cost-effective components tailored to specific industrial needs.
Summary Table:
Category | Applications |
---|---|
Metals | Armatures, bearing retainers, brackets, cams, gears, electrical contacts |
Ceramics & Glass | High-strength ceramics, porcelain, glass with low porosity |
Filtration | Filters (e.g., PE filters) with controlled porosity |
Plastics | Lightweight, strong, and wear-resistant components |
Advantages | Cost-effective, customizable, versatile for high-melting-point materials |
Modern Techniques | 3D printing, isostatic pressing, extruding, tapecasting |
Unlock the potential of sintered products for your industry—contact us today to learn more!