Advanced heat treatment techniques have evolved significantly, driven by technological advancements and the need for precise control over material properties. These techniques include the use of advanced equipment like vacuum furnaces, gas-pumped furnaces, and oxygen probes, as well as the integration of process simulators for recipe development. Key methods such as annealing, case hardening, precipitation strengthening, tempering, and quenching have been refined to achieve specific outcomes like stress relief, hardening, or softening of materials. Additionally, specialized processes like austempering, marquenching, and magnetic annealing are used to enhance material resilience and magnetic properties. These advancements ensure better control over metallurgical outcomes and improved material performance.
Key Points Explained:
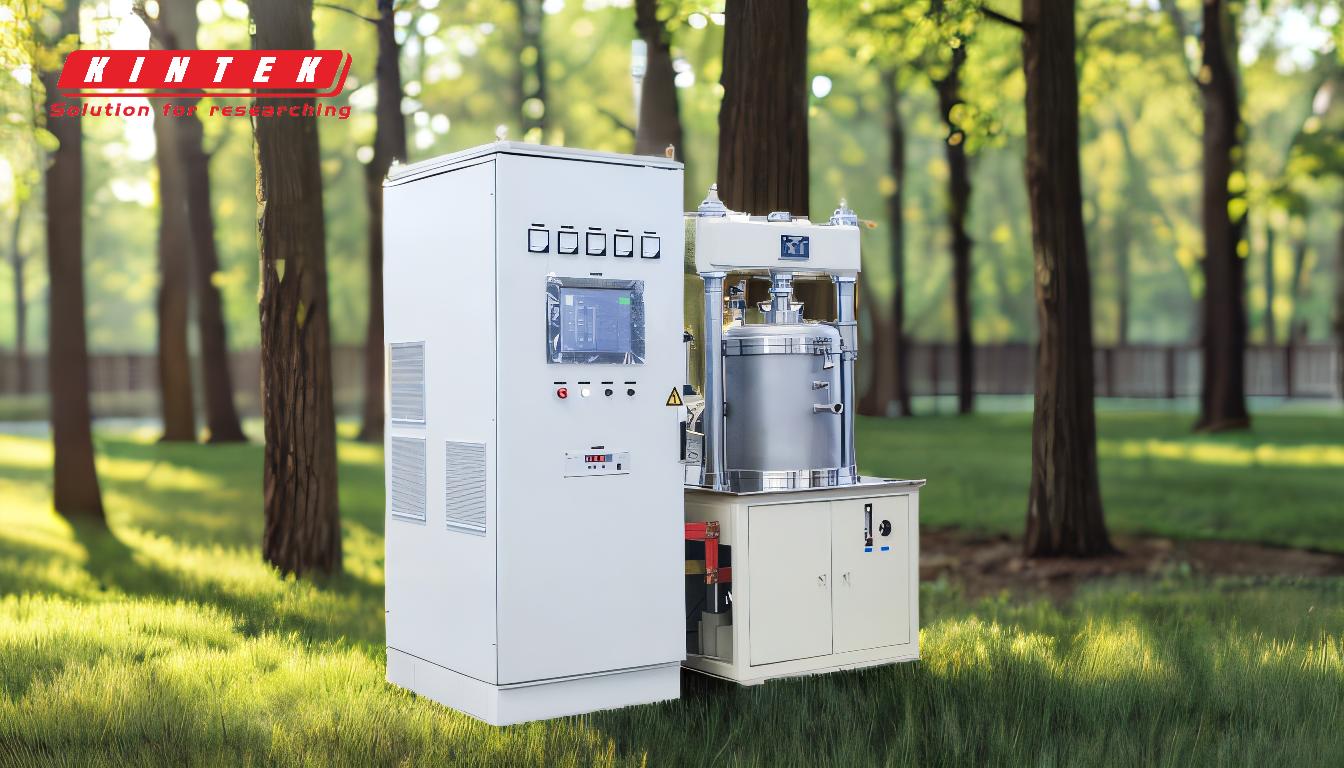
-
Technological Advancements in Heat Treatment:
- Oxygen Probes: These are critical for monitoring and controlling the atmosphere within heat treatment furnaces, ensuring optimal conditions for processes like carburizing and nitriding.
- Process Simulators: Used for recipe development, these tools allow for precise control and optimization of heat treatment parameters, reducing trial and error in industrial settings.
- Vacuum and Gas-Pumped Furnaces: These advanced furnaces use controlled atmospheres with gases like carbon, nitrogen, argon, and carbon dioxide to achieve specific metallurgical outcomes, such as preventing oxidation and ensuring uniform heating.
-
Common Heat Treatment Techniques:
- Annealing: Used to soften metals or plastics, relieve internal stresses, and improve ductility. It involves heating the material to a specific temperature and then slowly cooling it.
- Case Hardening: A surface hardening technique that increases the hardness of the outer layer while maintaining a tough core. Methods include carburizing and nitriding.
- Precipitation Strengthening: Enhances the strength of alloys by forming fine particles within the material, which impede dislocation movement.
- Tempering: Reduces brittleness in hardened steels by reheating them to a lower temperature, improving toughness and ductility.
- Quenching: Rapidly cools heated metal to achieve high hardness, often followed by tempering to balance hardness and toughness.
-
Specialized Heat Treatment Processes:
- Austempering and Marquenching: These are quenching processes that produce materials with high strength and resilience, often used for springs and other components requiring durability.
- Magnetic Annealing: Used to alter the magnetic permeability of materials, making them suitable for applications in electronics and magnetic shielding.
- Stress Relieving: A process to remove internal stresses from materials caused by machining, forming, or welding, improving dimensional stability and reducing the risk of cracking.
-
Applications of Advanced Heat Treatment:
- Through-Hardening: Used to harden the entire cross-section of a component, suitable for parts requiring uniform hardness.
- Induction and Flame Hardening: Localized hardening techniques used to harden specific areas of a part, such as gear teeth or bearing surfaces.
- Homogenization of Plastic Parts: Annealing is used to relieve stresses in plastic injection-molded parts, improving their dimensional stability and performance.
-
Benefits of Advanced Heat Treatment:
- Improved Material Properties: Advanced techniques allow for precise control over hardness, toughness, ductility, and other material properties.
- Enhanced Durability: Processes like case hardening and austempering increase the wear resistance and lifespan of components.
- Customization: Process simulators and controlled atmospheres enable tailored heat treatment solutions for specific applications.
These advanced techniques and tools have revolutionized the heat treatment industry, enabling manufacturers to achieve superior material performance and meet the demands of modern engineering applications.
Summary Table:
Category | Key Techniques/Equipment | Benefits |
---|---|---|
Technological Advancements | Oxygen Probes, Process Simulators, Vacuum & Gas-Pumped Furnaces | Precise control, optimized parameters, uniform heating, and oxidation prevention |
Common Techniques | Annealing, Case Hardening, Precipitation Strengthening, Tempering, Quenching | Stress relief, hardening, softening, and improved toughness |
Specialized Processes | Austempering, Marquenching, Magnetic Annealing, Stress Relieving | Enhanced resilience, magnetic properties, and dimensional stability |
Applications | Through-Hardening, Induction & Flame Hardening, Homogenization of Plastic Parts | Uniform hardness, localized hardening, and improved performance |
Benefits | Improved Material Properties, Enhanced Durability, Customization | Superior material performance and tailored solutions |
Transform your material performance with advanced heat treatment techniques—contact our experts today!