Hot forming and cold forming are two distinct manufacturing processes, each with its own set of advantages and disadvantages. Hot forming involves heating materials to high temperatures to make them more malleable, while cold forming shapes materials at or near room temperature, often resulting in stronger, more durable products. The choice between these methods depends on the specific requirements of the application, including material properties, desired product characteristics, and production efficiency.
Key Points Explained:
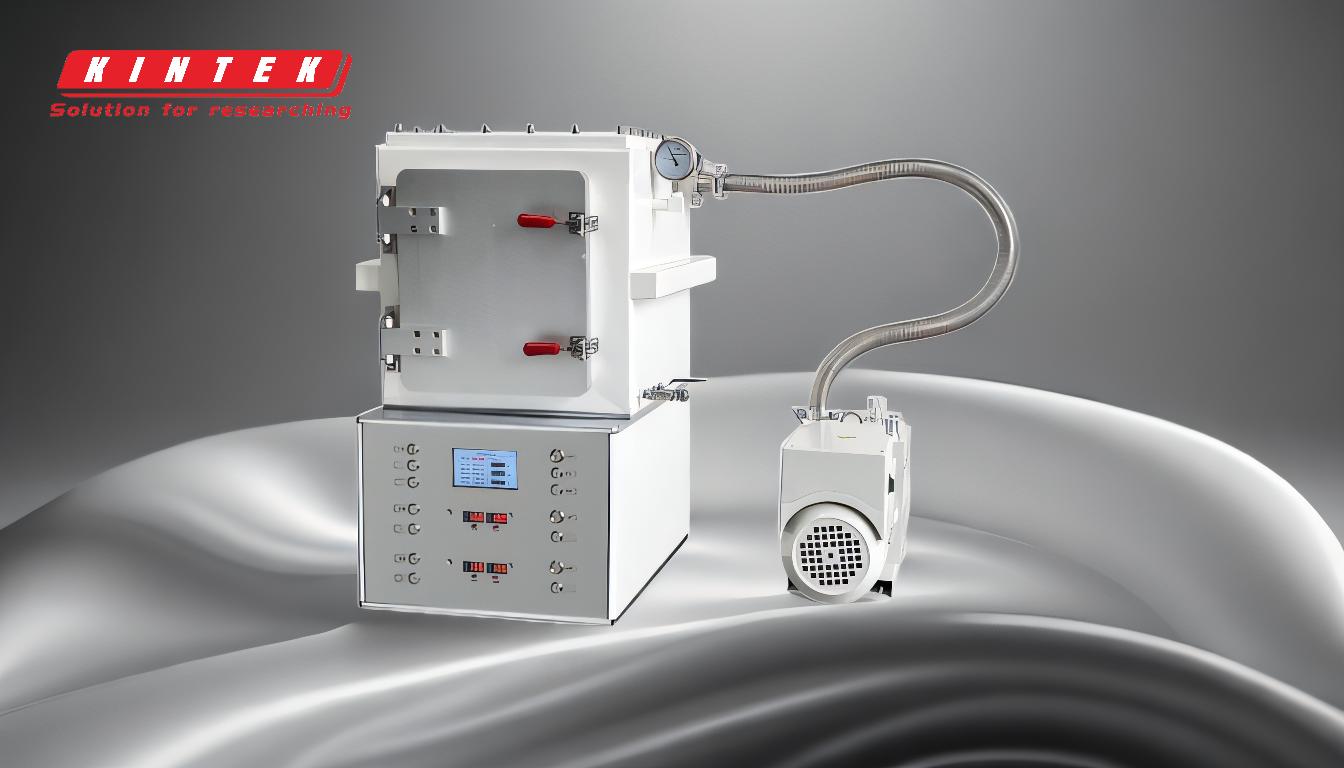
-
Advantages of Hot Forming:
- Increased Malleability: Heating materials reduces their yield strength, making them easier to shape and form into complex geometries without cracking.
- Lower Force Requirements: The reduced strength of heated materials means that less force is needed during the forming process, which can extend the life of the forming equipment.
- Enhanced Sintering Activity: In processes like direct hot pressing, fine metal powders can be sintered more effectively due to the high temperatures, leading to improved material properties.
-
Disadvantages of Hot Forming:
- Energy Consumption: The need to heat materials to high temperatures can lead to significant energy consumption, increasing the overall cost of production.
- Material Limitations: Not all materials are suitable for hot forming, as some may degrade or undergo undesirable phase changes at high temperatures.
- Dimensional Control: High temperatures can cause materials to expand, making it more challenging to maintain precise dimensional tolerances.
-
Advantages of Cold Forming:
- Improved Strength and Durability: Cold forming often results in work hardening, which increases the strength and durability of the final product.
- Better Surface Finish: Since cold forming does not involve heating, the surface finish of the product is often smoother and more consistent.
- Energy Efficiency: Cold forming processes typically require less energy compared to hot forming, as there is no need to heat the materials.
-
Disadvantages of Cold Forming:
- Higher Force Requirements: Cold forming requires more force to shape materials, which can lead to increased wear and tear on the forming equipment.
- Limited Complexity: Cold forming is generally less suitable for creating complex shapes, as the materials are less malleable at lower temperatures.
- Material Limitations: Some materials may become too brittle or difficult to form at room temperature, limiting the applicability of cold forming.
-
Applications and Industry Use:
- Hot Forming: Commonly used in industries such as furniture manufacturing, wooden door factories, and wood-based panel processing, where high temperatures are necessary to achieve the desired material properties.
- Cold Forming: Utilized in furniture production, wood industry, decoration, plastics, and other industries for high-quality component production, where strength and surface finish are critical.
In summary, the choice between hot forming and cold forming depends on the specific requirements of the application, including material properties, desired product characteristics, and production efficiency. Each method has its own set of advantages and disadvantages, and understanding these can help in selecting the most appropriate forming process for a given application.
Summary Table:
Aspect | Hot Forming | Cold Forming |
---|---|---|
Malleability | High (easier to shape complex geometries) | Low (less suitable for complex shapes) |
Force Requirements | Lower force needed, reducing equipment wear | Higher force required, increasing equipment wear |
Energy Efficiency | Less energy-efficient due to heating | More energy-efficient (no heating required) |
Material Suitability | Limited to materials that can withstand high temperatures | Limited to materials that don’t become brittle at room temperature |
Surface Finish | May require post-processing for smoothness | Smoother and more consistent surface finish |
Applications | Furniture manufacturing, wooden doors, wood-based panels | Furniture production, wood industry, decoration, plastics |
Need help choosing the right forming process for your application? Contact our experts today!