Brazing and soldering are both metal-joining techniques, but brazing offers distinct advantages in terms of strength, versatility, and application. Brazing creates joints that are as strong as the base metals, making it ideal for industries requiring durable connections, such as automotive, HVAC, and cookware. Unlike soldering, brazing does not melt the base metals, allowing for precise tolerances and the joining of dissimilar metals or complex parts. Additionally, brazing minimizes thermal distortion, making it suitable for high-volume production and applications where structural integrity is critical.
Key Points Explained:
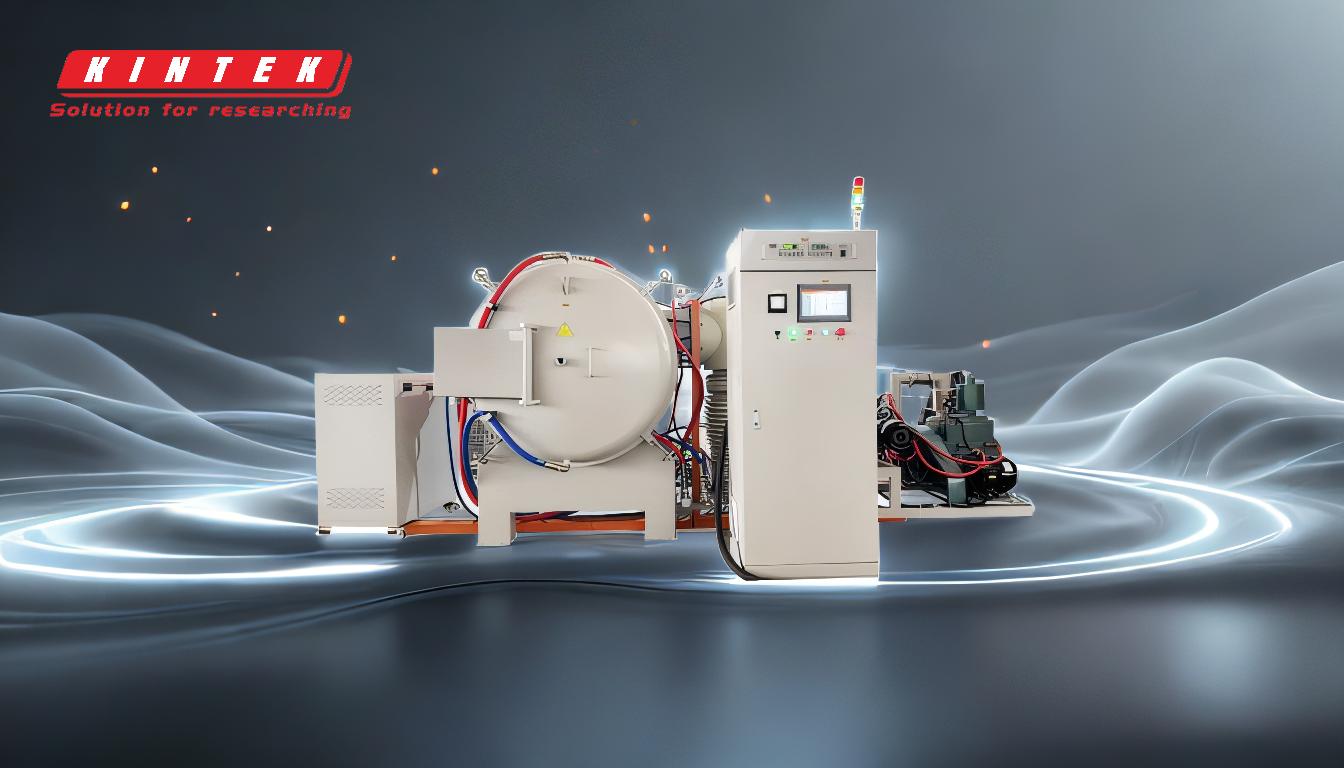
-
Stronger Joints Compared to Soldering:
- Brazed joints are as strong as the base metals themselves, offering superior mechanical strength compared to soldered joints. This makes brazing ideal for applications where durability and reliability are paramount, such as in automotive, HVAC, and cookware industries.
-
Base Metals Remain Unmelted:
- Unlike welding, brazing does not melt the base metals. This allows for:
- Close Tolerances: Precise joining without altering the dimensions of the base materials.
- Reduced Thermal Distortion: Minimized warping or deformation, which is especially important for delicate or complex components.
- Unlike welding, brazing does not melt the base metals. This allows for:
-
Versatility in Joining Dissimilar Materials:
- Brazing can join a wide range of materials, including:
- Dissimilar Metals: Such as copper to steel or aluminum to stainless steel.
- Nonmetals: Certain ceramics and composites can also be brazed.
- This versatility makes brazing a cost-effective solution for complex assemblies.
- Brazing can join a wide range of materials, including:
-
Suitability for High-Volume Production:
- Brazing is highly efficient for mass production due to:
- Consistent Quality: Uniform joints with minimal defects.
- Automation Potential: Easily integrated into automated manufacturing processes.
- This makes it a preferred choice for industries requiring high throughput, such as automotive and electronics.
- Brazing is highly efficient for mass production due to:
-
Wide Range of Applications:
- Brazing is used across various industries, including:
- Cookware: For durable and heat-resistant joints.
- Automotive: For critical components like radiators and air conditioning systems.
- HVAC Systems: For reliable and leak-free connections.
- Its adaptability to different materials and environments underscores its practicality.
- Brazing is used across various industries, including:
-
Cost-Effectiveness:
- Brazing is often more economical than welding or other joining methods because:
- Lower Energy Consumption: Requires less heat compared to welding.
- Reduced Post-Processing: Minimal cleanup or finishing is needed.
- These factors contribute to lower overall production costs.
- Brazing is often more economical than welding or other joining methods because:
In summary, brazing stands out as a superior metal-joining technique due to its strength, precision, versatility, and cost-effectiveness. Its ability to join dissimilar materials and complex parts without compromising the integrity of the base metals makes it a preferred choice for industries requiring durable and reliable connections.
Summary Table:
Advantage | Description |
---|---|
Stronger Joints | Brazed joints match the strength of base metals, ideal for durability-critical applications. |
Base Metals Remain Unmelted | Precise tolerances and reduced thermal distortion for delicate or complex parts. |
Versatility | Joins dissimilar metals and nonmetals like ceramics and composites. |
High-Volume Production | Consistent quality and automation potential for industries like automotive. |
Wide Applications | Used in cookware, automotive, and HVAC systems for reliable connections. |
Cost-Effectiveness | Lower energy consumption and reduced post-processing for economical production. |
Ready to enhance your metal-joining processes? Contact us today to learn more about brazing solutions!