Dual extruders in 3D printing offer significant advantages, particularly in enabling multi-material and multi-color printing. Unlike single extruders, which require manual filament changes to achieve similar effects, dual extruders streamline the process, allowing for more complex, detailed, and visually appealing prints. This capability is especially beneficial for creating intricate designs, functional prototypes, and artistic models. Below, we explore the key advantages of dual extruders in detail.
Key Points Explained:
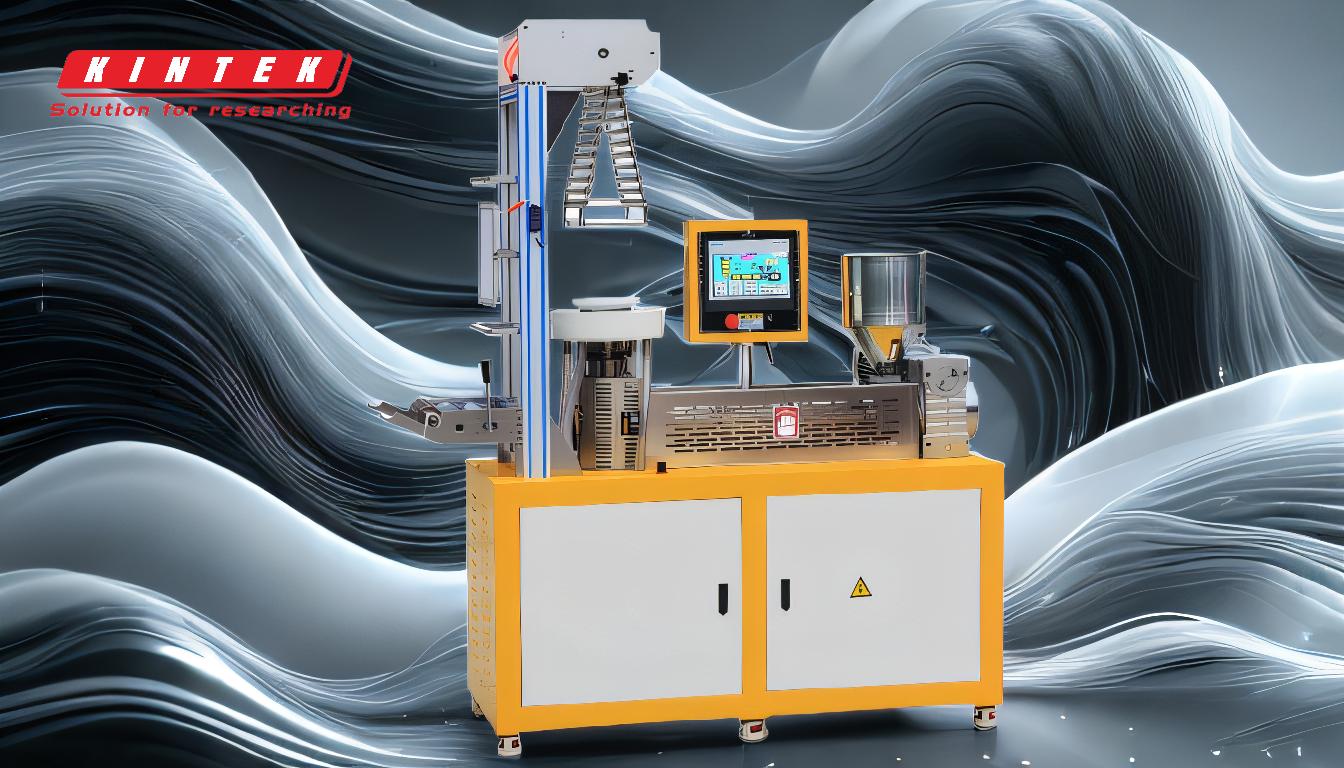
-
Multi-Material Printing:
- Dual extruders enable the use of two different materials simultaneously. This is particularly useful for creating functional prototypes that require both rigid and flexible components, such as a phone case with a soft grip and a hard shell.
- For example, one extruder can use PLA for structural parts, while the other uses custom PTFE for flexible hinges or grips. This eliminates the need for post-processing assembly and ensures better integration of materials.
-
Multi-Color Printing:
- With dual extruders, you can print objects in two distinct colors without manually changing filaments. This is ideal for creating visually striking models, such as logos, figurines, or architectural designs.
- Unlike single extruders, where color changes are cumbersome and time-consuming, dual extruders automate the process, resulting in smoother transitions and cleaner designs.
-
Support Material Integration:
- Dual extruders allow one extruder to print the main object while the other prints dissolvable support material (e.g., PVA or HIPS). This is especially useful for complex geometries with overhangs or internal cavities.
- The ability to use dissolvable supports ensures that the final print is cleaner and requires less manual post-processing, saving time and effort.
-
Increased Efficiency:
- Dual extruders reduce downtime by eliminating the need for manual filament changes. This is particularly advantageous for large-scale or batch printing, where time is a critical factor.
- The ability to switch between materials or colors seamlessly also minimizes errors and improves overall print quality.
-
Enhanced Design Flexibility:
- Dual extruders open up new possibilities for creative and functional designs. For instance, you can combine conductive and non-conductive materials to create embedded circuits or sensors directly within a 3D-printed object.
- This flexibility is invaluable for industries like electronics, robotics, and medical devices, where multi-material integration is often required.
-
Improved Print Quality:
- By using one extruder for the main material and another for support or secondary material, dual extruders reduce the risk of contamination or imperfections caused by material residue.
- This results in higher-quality prints with smoother surfaces and more precise details.
-
Cost-Effectiveness for Advanced Projects:
- While dual extruder printers may have a higher upfront cost, they can save money in the long run by reducing material waste and minimizing the need for additional tools or post-processing equipment.
- For businesses or hobbyists working on advanced projects, the investment in a dual extruder printer often pays off through improved efficiency and expanded capabilities.
In summary, dual extruders provide a range of advantages, from enabling multi-material and multi-color printing to improving efficiency and design flexibility. These benefits make dual extruders an excellent choice for users looking to push the boundaries of 3D printing, whether for professional applications or creative endeavors.
Summary Table:
Advantage | Description |
---|---|
Multi-Material Printing | Use two materials simultaneously, ideal for functional prototypes. |
Multi-Color Printing | Print in two colors without manual filament changes for striking designs. |
Support Material Integration | Print dissolvable supports for cleaner, post-processing-free results. |
Increased Efficiency | Eliminate downtime from manual filament changes, perfect for large-scale prints. |
Enhanced Design Flexibility | Combine materials like conductive and non-conductive for advanced applications. |
Improved Print Quality | Reduce contamination and imperfections for smoother, detailed prints. |
Cost-Effectiveness | Save on material waste and post-processing tools over time. |
Ready to elevate your 3D printing projects? Contact us today to learn more about dual extruder printers!