Press forging and drop forging are two common metalworking techniques, each with its own set of advantages and disadvantages. Press forging, in particular, offers several benefits over drop forging, making it a preferred choice in many industrial applications. These advantages include faster production times, cost efficiency, improved material strength, and enhanced metallurgical properties. Below, we will explore these benefits in detail to understand why press forging is often favored over drop forging.
Key Points Explained:
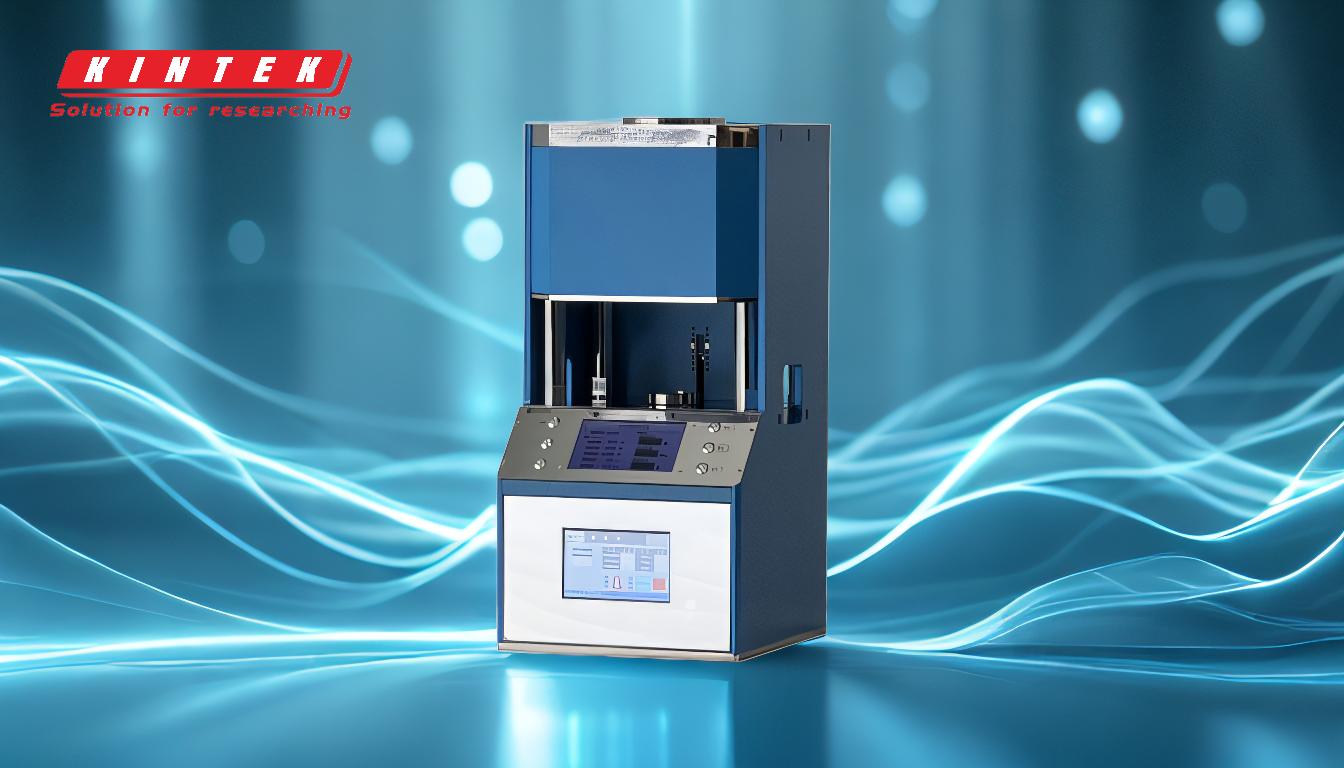
-
Faster Production Times:
- Explanation: Press forging is generally quicker than drop forging because it applies continuous pressure to the workpiece, allowing for faster deformation. This is in contrast to drop forging, which relies on repeated hammering or pressing actions, each requiring time to reset and reposition.
- Impact: The increased speed of press forging can lead to higher production rates, making it more suitable for high-volume manufacturing environments.
-
Cost Efficiency:
- Explanation: The quicker production times of press forging translate into lower labor costs and reduced energy consumption. Additionally, press forging often requires less material waste, as the process is more controlled and precise.
- Impact: These factors contribute to overall cost savings, making press forging a more economical option for many manufacturers.
-
Improved Material Strength:
- Explanation: Press forging produces a grain flow that follows the contours of the final piece, enhancing its strength and durability. This is achieved through the continuous application of pressure, which compresses the grain structure and reduces stress concentrations in critical areas such as corners and fillets.
- Impact: The improved grain flow and reduced stress concentrations result in a stronger final product that is better able to withstand mechanical loads and stresses.
-
Enhanced Metallurgical Properties:
- Explanation: Press forging minimizes metallurgical defects such as porosity and alloy segregation. The controlled and uniform application of pressure ensures a more homogeneous microstructure, which improves the piece's response to heat treatment.
- Impact: The reduction in defects and improved microstructure lead to better mechanical properties, such as increased toughness and fatigue resistance, which are crucial for high-performance applications.
-
Reduced Machining Time:
- Explanation: The precision and control of press forging result in a workpiece that is closer to its final shape, requiring less machining to achieve the desired dimensions and surface finish.
- Impact: This reduction in machining time not only lowers production costs but also shortens the overall manufacturing cycle, allowing for quicker delivery times.
In summary, press forging offers several significant advantages over drop forging, including faster production times, cost efficiency, improved material strength, enhanced metallurgical properties, and reduced machining time. These benefits make press forging an attractive option for manufacturers looking to optimize their production processes and produce high-quality, durable components.
Summary Table:
Advantage | Explanation | Impact |
---|---|---|
Faster Production Times | Continuous pressure allows quicker deformation compared to repeated hammering. | Higher production rates, ideal for high-volume manufacturing. |
Cost Efficiency | Lower labor costs, reduced energy consumption, and less material waste. | Significant cost savings for manufacturers. |
Improved Material Strength | Grain flow follows contours, reducing stress concentrations in critical areas. | Stronger, more durable products that withstand mechanical loads. |
Enhanced Metallurgical Properties | Minimizes defects like porosity and ensures a homogeneous microstructure. | Better toughness, fatigue resistance, and heat treatment response. |
Reduced Machining Time | Workpiece closer to final shape, requiring less machining. | Lower production costs and faster delivery times. |
Ready to optimize your manufacturing process? Contact us today to learn more about press forging solutions!