A rotor furnace, also known as a rotating furnace, offers several advantages that make it a valuable tool in specific industrial and scientific applications. Its unique design and operational characteristics provide benefits such as uniform heating, precise temperature control, and the ability to handle specialized tasks like creating lenses and primary mirrors for optical telescopes. These features make it ideal for applications requiring high precision and consistency. Below, we explore the key advantages of a rotor furnace in detail.
Key Points Explained:
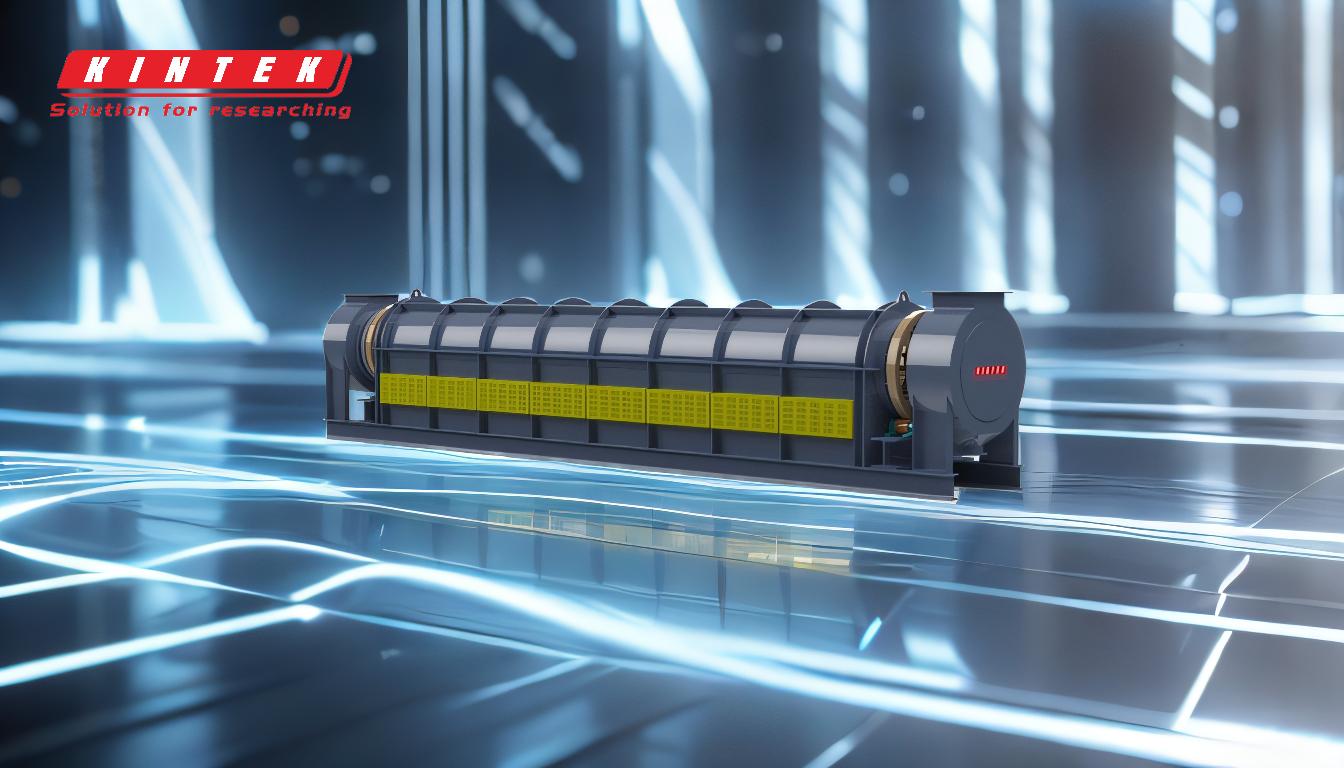
-
Uniform Heating and Temperature Control
- The rotating mechanism of the furnace ensures even distribution of heat, which is critical for processes requiring consistent thermal treatment. This uniformity is particularly beneficial for applications like glass or metal melting, where temperature gradients can lead to defects in the final product.
- Precise temperature control is achieved through advanced heating elements and monitoring systems, allowing for accurate adjustments to meet specific process requirements.
-
Specialized Applications
- One of the primary uses of a rotating furnace is in the production of lenses and primary mirrors for optical telescopes. The rotation allows for the creation of highly precise and symmetrical shapes, which are essential for optical clarity and performance.
- This capability makes the rotor furnace indispensable in fields like astronomy, where precision and quality are paramount.
-
Energy Efficiency
- The design of rotor furnaces often incorporates features that minimize energy consumption. For example, the rotating action can reduce the need for excessive heating by ensuring even heat distribution, thereby lowering operational costs.
- This efficiency aligns with modern industrial demands for environmentally friendly and cost-effective solutions.
-
Compact and Modular Design
- Rotor furnaces are often designed to be compact, making them suitable for small-scale or laboratory use. Their modular design allows for easy customization to meet specific application needs, such as varying chamber sizes or specialized heating elements.
- This flexibility makes them adaptable to a wide range of industries, from research and development to large-scale manufacturing.
-
Ease of Operation and Maintenance
- The simplicity of the rotating furnace design translates to ease of operation, reducing the need for highly specialized training. Automated controls and remote monitoring further enhance usability.
- Predictive maintenance features and robust construction contribute to a long service life, minimizing downtime and repair costs.
-
Versatility in Material Processing
- While the primary application of rotor furnaces is in optical manufacturing, their design allows for the processing of various materials, including metals, glass, and ceramics. This versatility makes them a valuable asset in industries requiring precise thermal treatment.
- The ability to handle multiple materials without compromising on quality or consistency is a significant advantage.
-
High-Quality and Repeatable Results
- The combination of uniform heating, precise temperature control, and specialized design ensures that rotor furnaces deliver high-quality results consistently. This repeatability is crucial for industries where product quality directly impacts performance and reliability.
- The guaranteed quality of output makes rotor furnaces a reliable choice for critical applications.
In summary, the rotor furnace stands out for its ability to deliver uniform heating, precise temperature control, and specialized processing capabilities. Its energy efficiency, compact design, and ease of operation further enhance its appeal across various industries. Whether used for creating optical components or processing advanced materials, the rotor furnace offers a combination of precision, reliability, and versatility that makes it a valuable tool in modern manufacturing and research.
Summary Table:
Advantages | Key Benefits |
---|---|
Uniform Heating | Ensures even heat distribution for consistent thermal treatment. |
Precise Temperature Control | Advanced systems for accurate adjustments and process-specific requirements. |
Specialized Applications | Ideal for creating optical components like telescope lenses and mirrors. |
Energy Efficiency | Reduces energy consumption and operational costs through efficient design. |
Compact and Modular Design | Adaptable for small-scale labs or large-scale manufacturing. |
Ease of Operation | Simple design with automated controls and remote monitoring. |
Versatility | Processes metals, glass, and ceramics with high precision and consistency. |
High-Quality Results | Delivers repeatable, reliable outcomes for critical applications. |
Unlock the potential of rotor furnaces for your applications—contact us today to learn more!