Spark Plasma Sintering (SPS) is an advanced sintering technology that offers numerous advantages over traditional sintering methods. It is particularly effective in fabricating ceramic, metallic, and composite materials with high density, fine grain size, and enhanced mechanical, electrical, and thermal properties. The key benefits of SPS include faster processing times, lower sintering temperatures, and precise control over sintering parameters. Additionally, SPS allows for multi-field coupling (electricity-mechanical-thermal), enabling the densification of a wide range of materials, from low melting point metals to ultra-high temperature ceramics. These advantages make SPS a versatile and efficient method for material fabrication.
Key Points Explained:
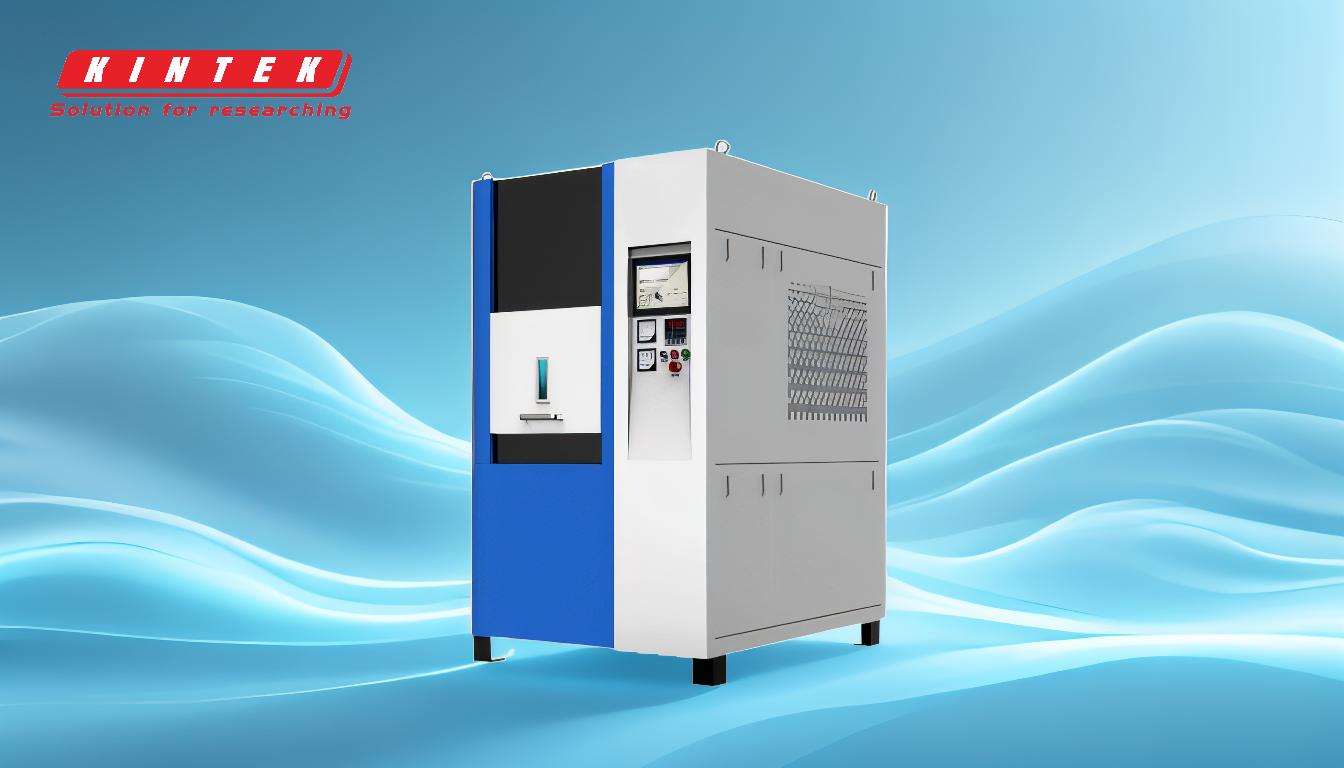
-
High Heating and Cooling Rates:
- SPS achieves significantly higher heating and cooling rates compared to traditional sintering methods. This results in shorter processing times, often reducing cycle times from hours or days to just minutes.
- The rapid heating and cooling help in maintaining fine grain sizes in the materials, which is crucial for enhancing mechanical properties such as strength and toughness.
-
Low Sintering Temperatures:
- SPS operates at lower sintering temperatures than conventional methods. This is beneficial for materials that are sensitive to high temperatures, as it minimizes the risk of thermal degradation or unwanted phase transformations.
- Lower temperatures also reduce energy consumption, making the process more cost-effective and environmentally friendly.
-
Short Holding Time:
- The holding time during sintering is significantly reduced in SPS. This not only speeds up the overall process but also helps in preserving the microstructure of the material, leading to better final properties.
- Short holding times are particularly advantageous for materials that are prone to grain growth or other microstructural changes during prolonged exposure to high temperatures.
-
Adjustable Sintering Pressure:
- SPS allows for precise control over the sintering pressure, which can be adjusted according to the specific requirements of the material being processed.
- This flexibility enables the densification of a wide range of materials, including those that are difficult to sinter using traditional methods.
-
Multi-Field Coupling (Electricity-Mechanical-Thermal):
- SPS utilizes a combination of electric fields, mechanical pressure, and thermal energy to achieve densification. This multi-field coupling enhances the sintering process, leading to improved material properties.
- The simultaneous application of these fields allows for better control over the sintering process, resulting in materials with superior mechanical, electrical, and thermal properties.
-
Enhanced Densification in Electrically Conductive Materials:
- The high pulsed current used in SPS is particularly effective in enhancing densification in electrically conductive materials. This results in materials with higher density and better overall properties.
- The pulsed current also helps in achieving uniform heating, which is crucial for obtaining consistent material properties throughout the sintered product.
-
Versatility in Material Processing:
- SPS is capable of processing a wide range of materials, from low melting point metals to ultra-high temperature ceramics. This versatility makes it a valuable tool in various industries, including aerospace, automotive, and electronics.
- The ability to sinter such a diverse range of materials opens up new possibilities for material design and application.
-
High-Precision Process Control:
- SPS offers high-precision control over sintering parameters, allowing for finely tuned processes that can be optimized for specific materials and desired outcomes.
- This level of control ensures that the final product meets the required specifications, making SPS a reliable method for producing high-quality materials.
In summary, Spark Plasma Sintering (SPS) provides a range of advantages that make it a superior choice for material fabrication. Its ability to achieve high heating and cooling rates, operate at lower temperatures, and offer precise control over sintering parameters results in materials with enhanced properties. The versatility and efficiency of SPS make it an invaluable technology in the field of material science and engineering.
Summary Table:
Key Advantage | Description |
---|---|
High Heating and Cooling Rates | Reduces cycle times to minutes, maintaining fine grain sizes for better strength. |
Low Sintering Temperatures | Minimizes thermal degradation and energy consumption, ideal for sensitive materials. |
Short Holding Time | Preserves microstructure, preventing grain growth and enhancing final properties. |
Adjustable Sintering Pressure | Enables densification of challenging materials with precise pressure control. |
Multi-Field Coupling | Combines electricity, mechanical pressure, and thermal energy for superior results. |
Enhanced Densification in Conductive Materials | Achieves higher density and uniform heating for consistent properties. |
Versatility in Material Processing | Processes metals, ceramics, and composites for diverse industrial applications. |
High-Precision Process Control | Ensures optimized sintering parameters for high-quality, tailored materials. |
Unlock the potential of Spark Plasma Sintering for your materials—contact our experts today!