Using an inert gas to prevent oxidation offers numerous benefits, particularly in industrial and laboratory settings where sensitive materials or processes are involved. Inert gases like nitrogen and argon create a non-reactive environment, effectively reducing or eliminating oxidation and other unwanted chemical reactions. This is crucial for preserving the integrity of materials, ensuring safety, and maintaining the quality of processes. Key advantages include slowing down oxidation processes, reducing contamination risks, preventing fire and explosion hazards, and enabling precise control over chemical reactions. Below, the key points are explained in detail.
Key Points Explained:
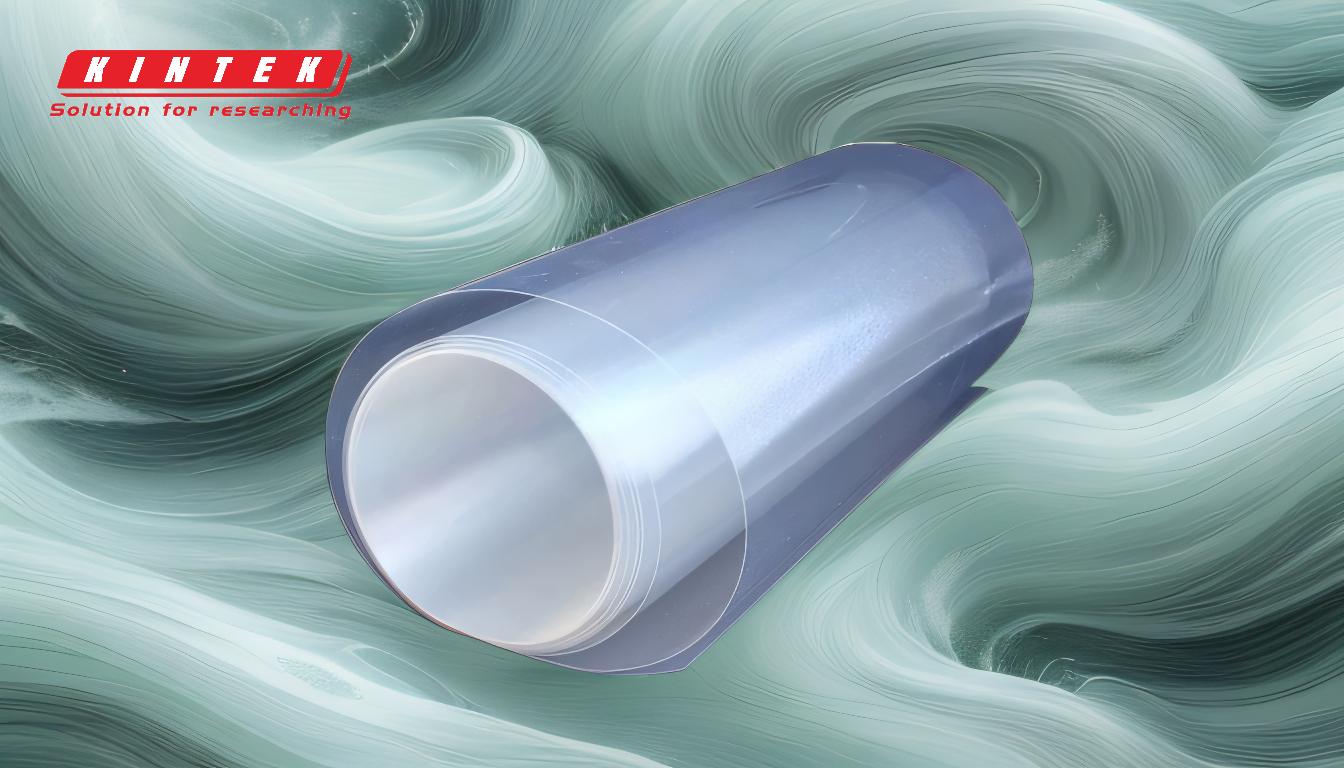
-
Prevention of Oxidation
- Inert gases like nitrogen and argon displace oxygen, which is the primary cause of oxidation.
- By creating an oxygen-free environment, inert gases protect materials that are sensitive to oxidation, such as metals, alloys, and certain chemicals.
- This is particularly important in heat treatment processes, where oxidation can degrade material properties like strength and durability.
-
Reduction of Reaction Rates
- Inert gases lower the oxidation potential and reaction rates by removing reactive gases like oxygen and moisture.
- This is beneficial in processes where controlled reactions are required, such as in the synthesis of chemicals or the processing of sensitive materials.
- Slowing down unwanted reactions ensures that the desired outcomes are achieved without interference.
-
Minimization of Contamination
- Inert atmospheres prevent contamination from airborne particles, moisture, and reactive gases.
- This is critical in industries like electronics manufacturing, where even trace amounts of contaminants can compromise product quality.
- By maintaining a clean environment, inert gases help ensure the purity and performance of materials and products.
-
Enhanced Safety
- Inert gases reduce the risk of fire and explosions by displacing flammable or reactive gases.
- They are commonly used to purge transfer lines and vessels, creating a safe environment for handling volatile substances.
- This safety measure is particularly important in the chemical industry, where reactive materials are frequently processed.
-
Creation of Controlled Environments
- Inert gases enable the creation of controlled atmospheres for precise chemical reactions and processes.
- For example, in semiconductor manufacturing, inert gases are used to prevent oxidation and ensure the integrity of delicate components.
- This level of control is essential for achieving consistent and high-quality results in advanced manufacturing processes.
-
Prevention of Hydrolysis and Other Reactions
- Inert gases protect materials from hydrolysis, a reaction that occurs with moisture in the air.
- This is particularly important for materials that are sensitive to water, such as certain polymers and chemicals.
- By eliminating moisture, inert gases help maintain the stability and shelf life of these materials.
-
Versatility in Applications
- Inert gases are used across a wide range of industries, including metallurgy, electronics, pharmaceuticals, and food packaging.
- Their non-reactive properties make them suitable for diverse applications, from heat treatment to preserving perishable goods.
- This versatility underscores their importance in modern industrial processes.
-
Cost-Effectiveness
- While inert gases may require an initial investment, their use can lead to cost savings by reducing material waste, improving process efficiency, and minimizing safety risks.
- For example, preventing oxidation in metals can extend their lifespan, reducing the need for frequent replacements.
- Additionally, avoiding contamination and unwanted reactions can save resources and improve overall productivity.
In summary, the use of inert gases to prevent oxidation provides significant benefits, including enhanced material integrity, improved safety, and greater process control. Their ability to create non-reactive environments makes them indispensable in industries where precision, quality, and safety are paramount. By leveraging the properties of inert gases, manufacturers and researchers can achieve better outcomes while minimizing risks and costs.
Summary Table:
Key Benefit | Description |
---|---|
Prevention of Oxidation | Displaces oxygen, protecting sensitive materials like metals and chemicals. |
Reduction of Reaction Rates | Lowers oxidation potential, ensuring controlled chemical reactions. |
Minimization of Contamination | Prevents airborne particles and moisture, ensuring material purity. |
Enhanced Safety | Reduces fire and explosion risks by displacing flammable gases. |
Controlled Environments | Enables precise chemical reactions, critical for advanced manufacturing. |
Prevention of Hydrolysis | Protects materials sensitive to moisture, maintaining stability and shelf life. |
Versatility in Applications | Used in metallurgy, electronics, pharmaceuticals, and food packaging industries. |
Cost-Effectiveness | Reduces material waste, improves efficiency, and minimizes safety risks. |
Learn how inert gases can optimize your processes—contact our experts today!