Heating elements, particularly electric heating elements, are critical components in various industrial and domestic heating systems. Their failure can lead to operational downtime and increased maintenance costs. The primary causes of failure include the formation of hot spots, oxidation and thermal stress, embrittlement due to grain growth, and contamination or corrosion. Understanding these factors can help in selecting the right materials and operational practices to extend the lifespan of heating elements.
Key Points Explained:
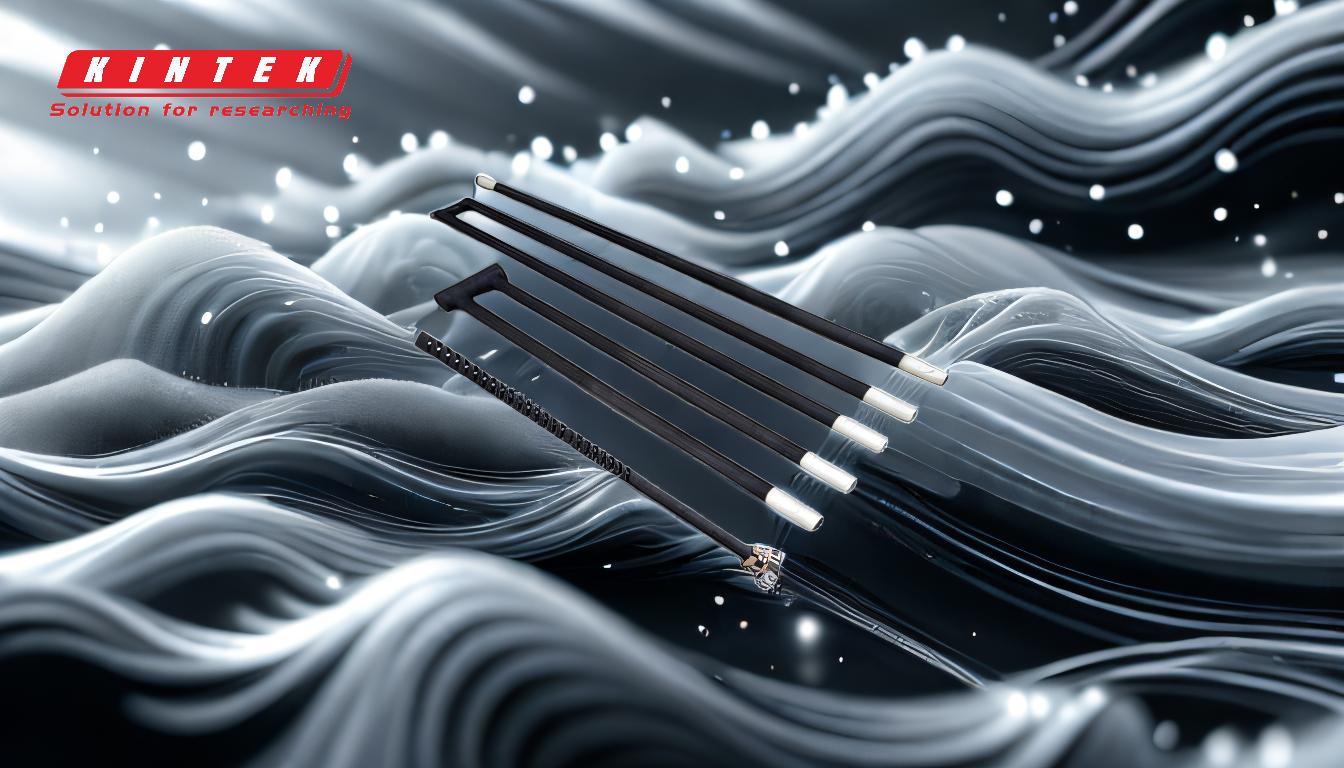
-
Formation of Hot Spots:
- Cause: Hot spots occur due to high local oxidation or shielding by supports, which leads to uneven heating.
- Impact: These hot spots can cause localized overheating, leading to breakdown and failure of the heating element.
- Prevention: Ensuring uniform heating and proper placement of supports can mitigate the formation of hot spots.
-
Oxidation and Thermal Stress:
- Cause: Continuous exposure to high temperatures causes oxidation, and the intermittency of operation leads to thermal stress.
- Impact: The repeated thermal cycling can cause flaking of the oxide layers, weakening the element over time.
- Prevention: Using materials with high oxidation resistance and minimizing thermal cycling can reduce this type of failure.
-
Embrittlement Due to Grain Growth:
- Cause: Prolonged exposure to high temperatures can lead to grain growth in the material of the heating element.
- Impact: This grain growth makes the element brittle and more susceptible to rupture under stress.
- Prevention: Selecting materials with better high-temperature stability and limiting the maximum operating temperature can help prevent embrittlement.
-
Contamination and Corrosion:
- Cause: Exposure to gases, fumes, or oils in the furnace environment can lead to contamination and corrosion.
- Impact: Contaminants can react with the heating element material, leading to corrosion and eventual failure.
- Prevention: Maintaining a clean furnace environment and using protective coatings or materials resistant to corrosion can extend the life of the heating element.
Understanding these key points can guide the selection and maintenance of electric heating elements, ensuring their reliable operation and longevity in various applications.
Summary Table:
Cause of Failure | Impact | Prevention |
---|---|---|
Formation of Hot Spots | Localized overheating leading to breakdown | Ensure uniform heating and proper placement of supports |
Oxidation and Thermal Stress | Flaking of oxide layers, weakening the element | Use oxidation-resistant materials and minimize thermal cycling |
Embrittlement Due to Grain Growth | Brittleness and susceptibility to rupture under stress | Select high-temperature stable materials and limit maximum operating temperature |
Contamination and Corrosion | Corrosion leading to failure | Maintain a clean furnace environment and use corrosion-resistant materials |
Ensure your heating elements operate reliably—contact our experts today for tailored solutions!