Producing graphene at scale presents several significant challenges, including achieving consistent quality, large-scale production, and cost-effectiveness. Key issues include controlling defects, grain size, and impurities, as well as ensuring homogeneity and reliability in the final product. Transfer processes, which are critical for integrating graphene into applications, remain a bottleneck. Additionally, the industry faces a mismatch between production capabilities and market demand, further complicating efforts to commercialize graphene. Addressing these challenges requires advancements in production techniques, particularly in methods like chemical vapor deposition (CVD), to enable the mass production of high-quality graphene suitable for industrial applications.
Key Points Explained:
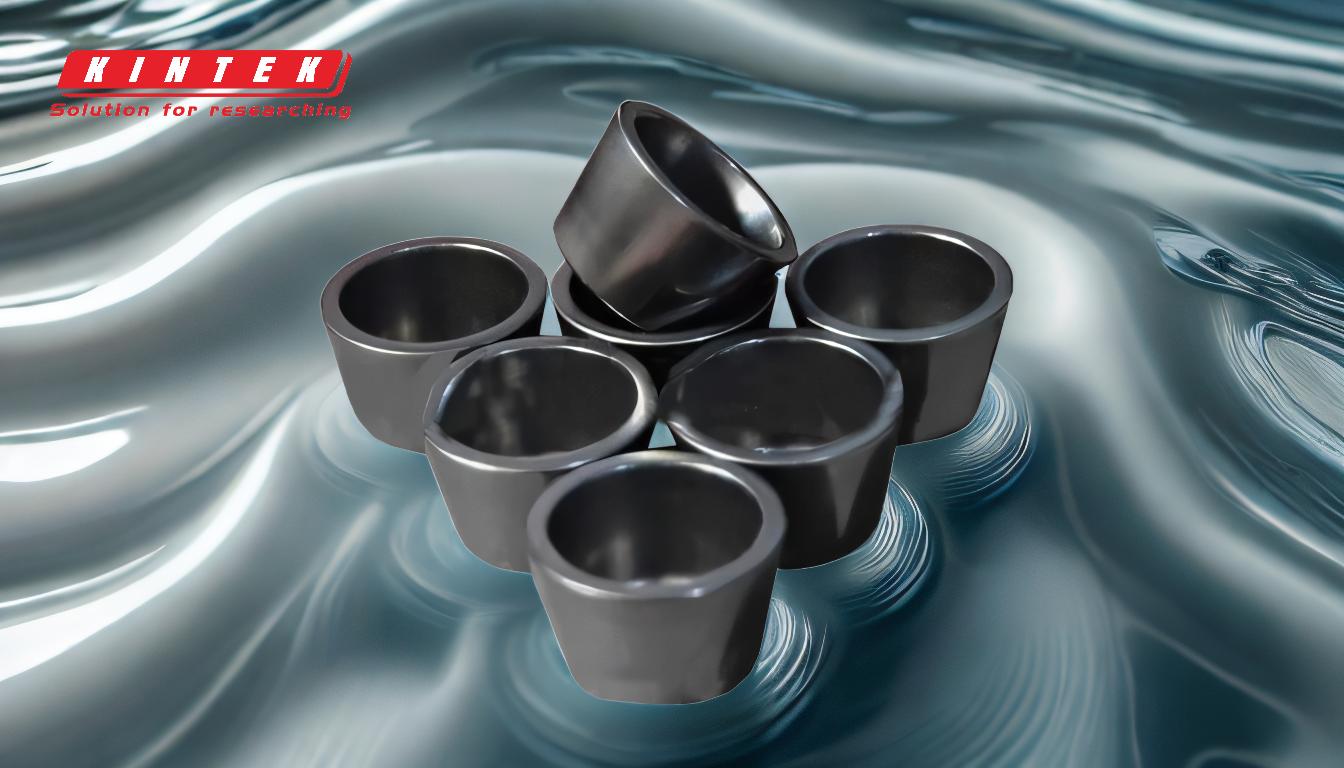
-
Achieving High-Quality Graphene at Scale:
- Defects and Contaminants: One of the primary challenges is producing graphene with minimal defects and contaminants. Current methods often result in graphene with varying levels of impurities, which can degrade its performance in applications.
- Grain Size: Large grain size is desirable for many applications, as it reduces the number of grain boundaries, which can negatively affect electrical and mechanical properties. However, controlling grain size during production is difficult, especially at scale.
-
Homogeneity and Consistency:
- Uniformity: Industrial production requires graphene that is homogeneous in terms of thickness, flake size, and quality. Achieving this uniformity across large batches is challenging due to the variability in production processes.
- Reliability: Consistent quality is critical for industrial applications, but current methods often produce graphene with inconsistent properties, making it difficult to guarantee performance.
-
Cost-Effectiveness:
- Production Costs: The cost of producing high-quality graphene remains high, particularly when using methods like CVD. Reducing production costs while maintaining quality is a significant hurdle for commercialization.
- Scalability: Many laboratory-scale methods are not easily scalable to industrial levels, limiting the ability to produce graphene in large quantities at a reasonable cost.
-
Transfer Processes:
- Integration Challenges: Transferring graphene from the substrate on which it is grown to the target application is a critical step. Current transfer processes are complex and can introduce defects or contaminants, making them a bottleneck in production.
- Damage and Impurities: During transfer, graphene can be damaged or contaminated, further reducing its quality and usability.
-
CVD-Specific Challenges:
- Polycrystalline Nature: CVD-produced graphene is typically polycrystalline, with domains ranging from micrometers to millimeters in size. Controlling the size and distribution of these domains is challenging but necessary for optimizing performance.
- Layer Control: Precise control over the number of graphene layers is essential for many applications. However, achieving this control consistently is difficult, particularly in large-scale production.
-
Market Alignment:
- Materials Push vs. Market Pull: Many manufacturers face a "materials push" scenario, where production capabilities outpace market demand. This misalignment complicates efforts to commercialize graphene and invest in scalable production methods.
- Application-Specific Requirements: Different applications require graphene with specific properties, further complicating production efforts. Tailoring production methods to meet these diverse needs is a significant challenge.
-
Technological Limitations:
- Limited Scalable Methods: While many methods for graphene production exist, few are suitable for large-scale industrial use. Developing scalable techniques that maintain high quality and low cost is a key area of research.
- Surface Area and Yield: Producing graphene with large surface areas and high yields is essential for industrial applications, but current methods often fall short in these areas.
In summary, the challenges in producing graphene are multifaceted, involving technical, economic, and market-related issues. Addressing these challenges requires continued innovation in production techniques, particularly in areas like defect control, scalability, and transfer processes, to unlock the full potential of graphene for industrial applications.
Summary Table:
Challenge | Key Issues |
---|---|
Quality Control | Defects, contaminants, grain size, and uniformity issues. |
Cost-Effectiveness | High production costs and limited scalability of methods like CVD. |
Transfer Processes | Integration challenges, damage, and impurities during transfer. |
Market Alignment | Mismatch between production capabilities and market demand. |
Technological Limitations | Limited scalable methods and challenges in surface area and yield. |
Discover how to overcome graphene production challenges—contact our experts today for tailored solutions!