Slow cooling, also known as annealing or controlled cooling, significantly impacts the mechanical properties of materials, particularly metals and alloys. The process involves reducing the cooling rate after heating, which allows for the formation of a more stable microstructure. This results in changes to properties such as hardness, tensile strength, ductility, and toughness. Slow cooling generally reduces hardness and tensile strength while increasing ductility and toughness, making the material more workable and less prone to cracking. The specific changes depend on the material composition, cooling rate, and initial microstructure.
Key Points Explained:
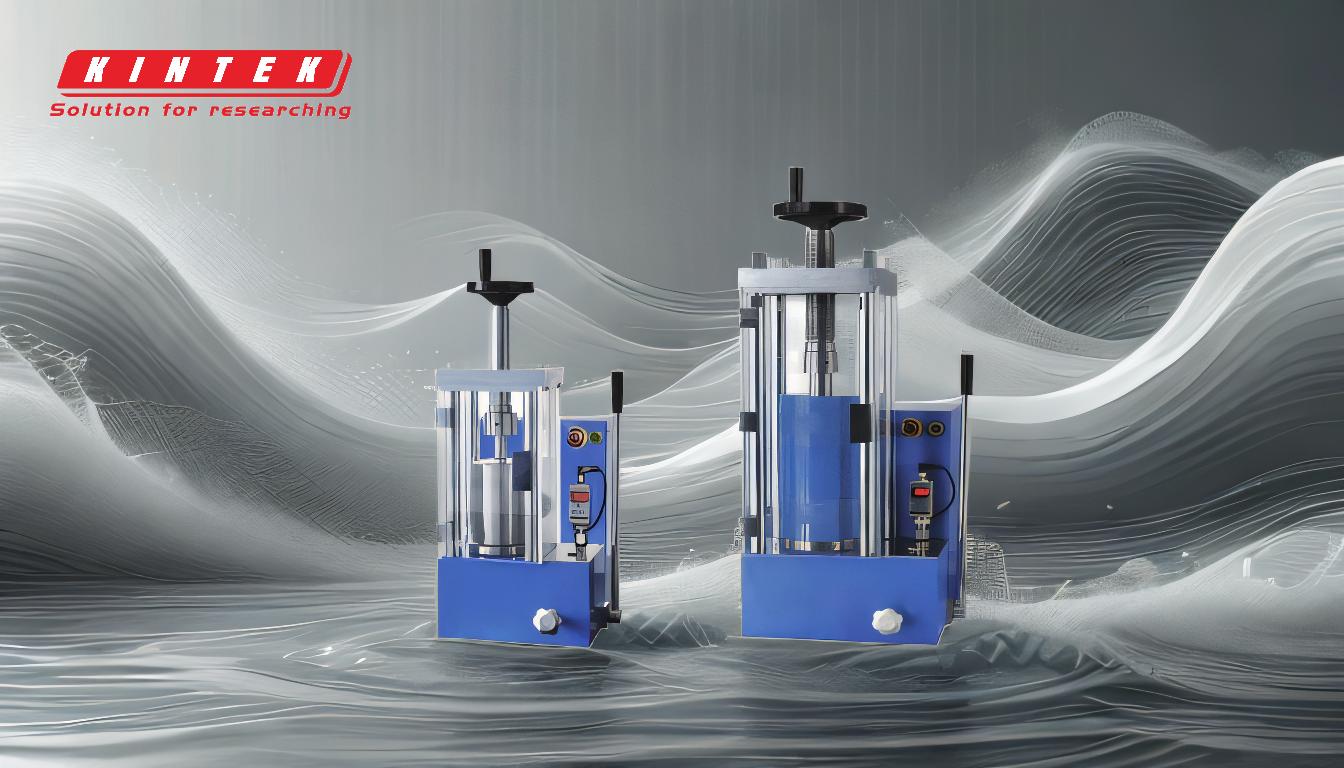
-
Reduction in Hardness and Tensile Strength
- Slow cooling allows atoms to rearrange into a more stable and less strained configuration, reducing internal stresses.
- This leads to a decrease in hardness and tensile strength because the material becomes softer and less resistant to deformation.
- For example, in steels, slow cooling transforms austenite into pearlite, which is softer than martensite formed during rapid cooling.
-
Increase in Ductility
- Ductility refers to a material's ability to deform plastically without fracturing.
- Slow cooling promotes the formation of larger, more equiaxed grains, which enhance ductility.
- This is particularly beneficial for materials that need to undergo further forming processes, such as rolling or forging.
-
Improved Toughness
- Toughness is the ability of a material to absorb energy and plastically deform without fracturing.
- Slow cooling reduces brittleness by minimizing the formation of hard, brittle phases like martensite.
- This makes the material more resistant to impact and fatigue, which is crucial for applications subjected to dynamic loads.
-
Microstructural Changes
- Slow cooling leads to the formation of coarse microstructures, such as pearlite in steels or larger grain sizes in other metals.
- These microstructures are more stable and less prone to cracking under stress.
- The specific microstructure depends on the material and cooling rate, but generally, slower cooling favors equilibrium phases.
-
Stress Relief and Dimensional Stability
- Slow cooling helps relieve residual stresses induced during manufacturing processes like casting or welding.
- This improves dimensional stability and reduces the likelihood of warping or distortion during subsequent machining or use.
-
Material-Specific Effects
- The impact of slow cooling varies by material. For example:
- Steels: Forms pearlite, which is softer and more ductile than martensite.
- Aluminum Alloys: Enhances precipitation hardening and improves workability.
- Titanium Alloys: Promotes the formation of alpha phase, increasing toughness and reducing brittleness.
- The impact of slow cooling varies by material. For example:
-
Applications and Trade-Offs
- Slow cooling is often used in annealing processes to improve machinability, formability, and weldability.
- However, it may not be suitable for applications requiring high hardness or wear resistance, where rapid cooling (quenching) is preferred.
- The choice of cooling rate depends on the desired balance between strength, ductility, and toughness for the specific application.
By understanding these changes, material engineers and purchasers can make informed decisions about cooling processes to achieve the desired mechanical properties for their applications.
Summary Table:
Property | Effect of Slow Cooling |
---|---|
Hardness | Reduces hardness, making the material softer. |
Tensile Strength | Decreases tensile strength due to reduced internal stresses. |
Ductility | Increases ductility, enhancing the material's ability to deform without fracturing. |
Toughness | Improves toughness, making the material more resistant to impact and fatigue. |
Microstructure | Forms stable, coarse microstructures like pearlite in steels. |
Stress Relief | Relieves residual stresses, improving dimensional stability. |
Material-Specific | Effects vary; e.g., steels form pearlite, aluminum alloys improve workability. |
Optimize your material properties with the right cooling process—contact our experts today for tailored solutions!