Heat treatment furnaces are classified based on several key factors, including the source of heat, working temperature, and the type of heat treatment they perform. These classifications help in selecting the right furnace for specific industrial applications. Heat sources can be resistance-based or fuel-based, with fuels further divided into solid, liquid, and gaseous types. Temperature classifications include low, medium, and high-temperature furnaces, each suited for different heat treatment processes. Additionally, furnaces are categorized by their structure and the specific heat treatment processes they are designed for, such as annealing, tempering, hardening, and carburizing.
Key Points Explained:
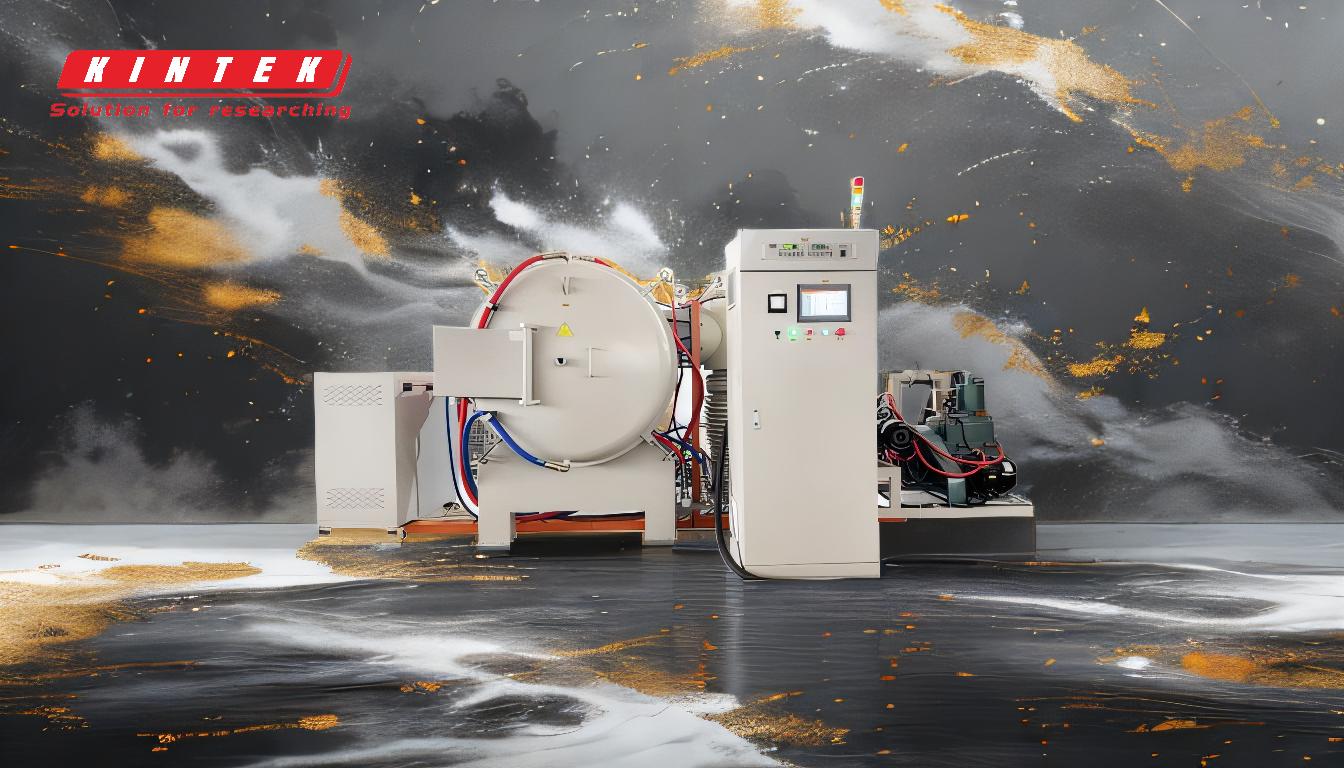
-
Classification by Heat Source:
- Resistance Furnaces: These use electrical resistance to generate heat and are known for precise temperature control. They are commonly used in applications requiring uniform heating.
-
Fuel Furnaces: These rely on combustion of fuels to produce heat. They are further classified based on the type of fuel used:
- Solid Fuels: Includes coal, pulverized coal, and coke. These are cost-effective but may produce more emissions.
- Liquid Fuels: Such as gasoline and kerosene. These offer better control over combustion compared to solid fuels.
- Gaseous Fuels: Includes coal gas and producer gas. These are cleaner and provide efficient heat distribution.
-
Classification by Working Temperature:
- Low Temperature Furnaces (<650°C): Used for processes like tempering and sub-critical annealing. These furnaces often employ forced air circulation or liquid baths (oil, lead, or salt) to achieve uniform heating.
- Medium Temperature Furnaces (650-1000°C): Suitable for processes like hardening, normalizing, and carburizing of carbon and low alloy steels. These furnaces are versatile and widely used in general-purpose heat treatment.
- High Temperature Furnaces (>1000°C): Designed for heat treatment of high-speed steels and other high-temperature cycles. These furnaces can operate up to 1400°C and are essential for specialized treatments.
-
Classification by Heat Treatment Process:
- Annealing Furnaces: These include roller hearth furnaces, pusher furnaces, box furnaces, pot/pit furnaces, conveyor belt furnaces, and integral-quench furnaces. Each type is designed to handle specific annealing processes, ensuring uniform heating and cooling.
- Tempering Furnaces: Used for tempering or sub-critical annealing, typically operating at temperatures between 0 to 700°C. These furnaces often use dry heat with forced air circulation or liquid baths.
- Carburizing or Carbonitriding Furnaces: These are specialized furnaces used for surface hardening processes. They introduce carbon or nitrogen into the surface of the metal to enhance its hardness and wear resistance.
-
Classification by Structure:
- Vertical Furnaces: These are designed with a vertical orientation, making them suitable for specific industrial processes where space is a constraint.
- Horizontal Furnaces: These have a horizontal orientation and are commonly used for continuous heat treatment processes.
- Single Chamber Furnaces: These have one chamber for both heating and cooling, making them suitable for batch processes.
- Three Chamber Furnaces: These have separate chambers for heating, cooling, and quenching, allowing for more complex heat treatment cycles.
-
Specialized Furnaces:
- Vacuum Resistance Furnaces: These are modern furnaces where the entire shell serves as the vacuum container. They are used for processes requiring a controlled atmosphere, such as endothermic treatments. They can be vertical, horizontal, single chamber, or three chamber types.
Understanding these classifications helps in selecting the appropriate furnace based on the specific heat treatment requirements, ensuring optimal performance and efficiency in industrial applications.
Summary Table:
Classification | Key Features | Applications |
---|---|---|
By Heat Source | Resistance (precise control), Fuel (solid, liquid, gaseous) | Uniform heating, cost-effective or efficient heat distribution |
By Temperature | Low (<650°C), Medium (650-1000°C), High (>1000°C) | Tempering, hardening, high-speed steel treatments |
By Heat Treatment Process | Annealing, Tempering, Carburizing | Uniform heating, surface hardening, wear resistance |
By Structure | Vertical, Horizontal, Single Chamber, Three Chamber | Space constraints, continuous processes, batch or complex cycles |
Specialized Furnaces | Vacuum Resistance (controlled atmosphere) | Endothermic treatments, high-precision processes |
Need help selecting the right heat treatment furnace? Contact our experts today for tailored solutions!