A plate and frame filter press is a crucial piece of equipment used in solid-liquid separation processes, particularly in industries like mining, chemical processing, and wastewater treatment. Its primary function is to separate solids from liquids using pressure filtration. The four main components of a plate and frame filter press are the frame, filter plates, manifold (piping and valves), and filter cloth. Each component plays a vital role in ensuring the efficiency and effectiveness of the filtration process. Understanding these components is essential for optimizing operations, maintenance, and troubleshooting in any filtration setup.
Key Points Explained:
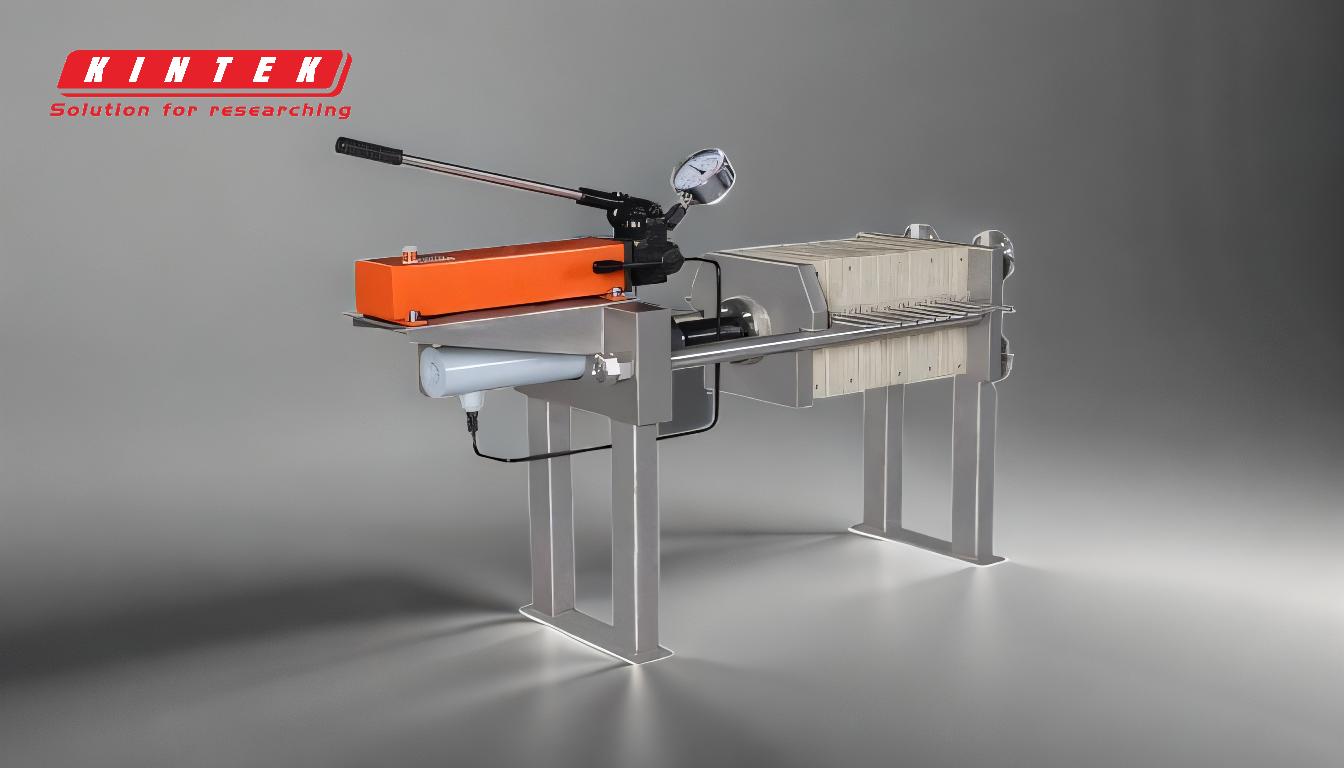
-
Frame
- The frame is the structural backbone of the filter press, providing stability and support to the entire system.
- It typically consists of two end plates connected by parallel beams or sidebars.
- The frame holds the filter plates and cloth in place and ensures proper alignment during operation.
- The size and strength of the frame depend on the scale of the filtration process and the pressure requirements.
- A robust frame is essential for maintaining the integrity of the filter press under high-pressure conditions.
-
Filter Plates
- Filter plates are the core components where the actual filtration occurs.
- They are usually made of materials like polypropylene, stainless steel, or cast iron, depending on the application and chemical compatibility.
- Each plate has a recessed surface or a chamber where the filter cloth is placed, creating a space for the slurry to be filtered.
- The plates are designed with holes or channels that allow the liquid (filtrate) to pass through while retaining the solids (filter cake).
- The arrangement of the plates can vary, such as plate-and-frame or recessed chamber designs, depending on the specific filtration needs.
-
Manifold (Piping and Valves)
- The manifold system includes the piping, valves, and other components that control the flow of the slurry, filtrate, and air or water used for cleaning.
- The slurry inlet valve directs the feed material into the filter press, while the filtrate outlet valve allows the filtered liquid to exit the system.
- Valves are also used for air or water flushing to clean the filter cloth and plates after each cycle.
- Proper design and maintenance of the manifold are critical for ensuring smooth operation and preventing leaks or blockages.
-
Filter Cloth
- The filter cloth is a key ingredient for optimizing filter press operations, as it directly influences the filtration efficiency and cake formation.
- It is made from materials like polyester, polypropylene, or nylon, chosen based on the chemical and thermal properties of the slurry.
- The cloth acts as a medium to trap solid particles while allowing the liquid to pass through.
- The selection of the right filter cloth depends on factors like particle size, slurry composition, and desired cake moisture content.
- Regular inspection and replacement of the filter cloth are necessary to maintain optimal performance and prevent clogging or tearing.
By understanding the roles and characteristics of these components, operators can make informed decisions about equipment selection, maintenance, and process optimization. For more detailed information on filter presses, you can explore the topic of lab filter press.
Summary Table:
Component | Role | Key Features |
---|---|---|
Frame | Provides structural support and stability | Made of durable materials; holds filter plates and cloth in place |
Filter Plates | Core filtration component; separates solids from liquids | Made of polypropylene, stainless steel, or cast iron; recessed surface for slurry |
Manifold | Controls flow of slurry, filtrate, and cleaning agents | Includes piping and valves; ensures smooth operation and prevents blockages |
Filter Cloth | Traps solid particles while allowing liquid to pass through | Made of polyester, polypropylene, or nylon; chosen based on slurry properties |
Optimize your filtration process with the right plate and frame filter press—contact our experts today for personalized solutions!