Thermal cracking is a process used in the petroleum industry to break down large hydrocarbon molecules into smaller, more valuable ones by applying heat. This process is crucial for producing lighter fractions such as gasoline, diesel, and other petrochemicals. The conditions for thermal cracking are influenced by several factors, including temperature, pressure, residence time, and the type of feedstock. Understanding these conditions is essential for optimizing the process and achieving desired product yields. Below, we will explore the key factors that influence thermal cracking and how they interact to produce the desired outcomes.
Key Points Explained:
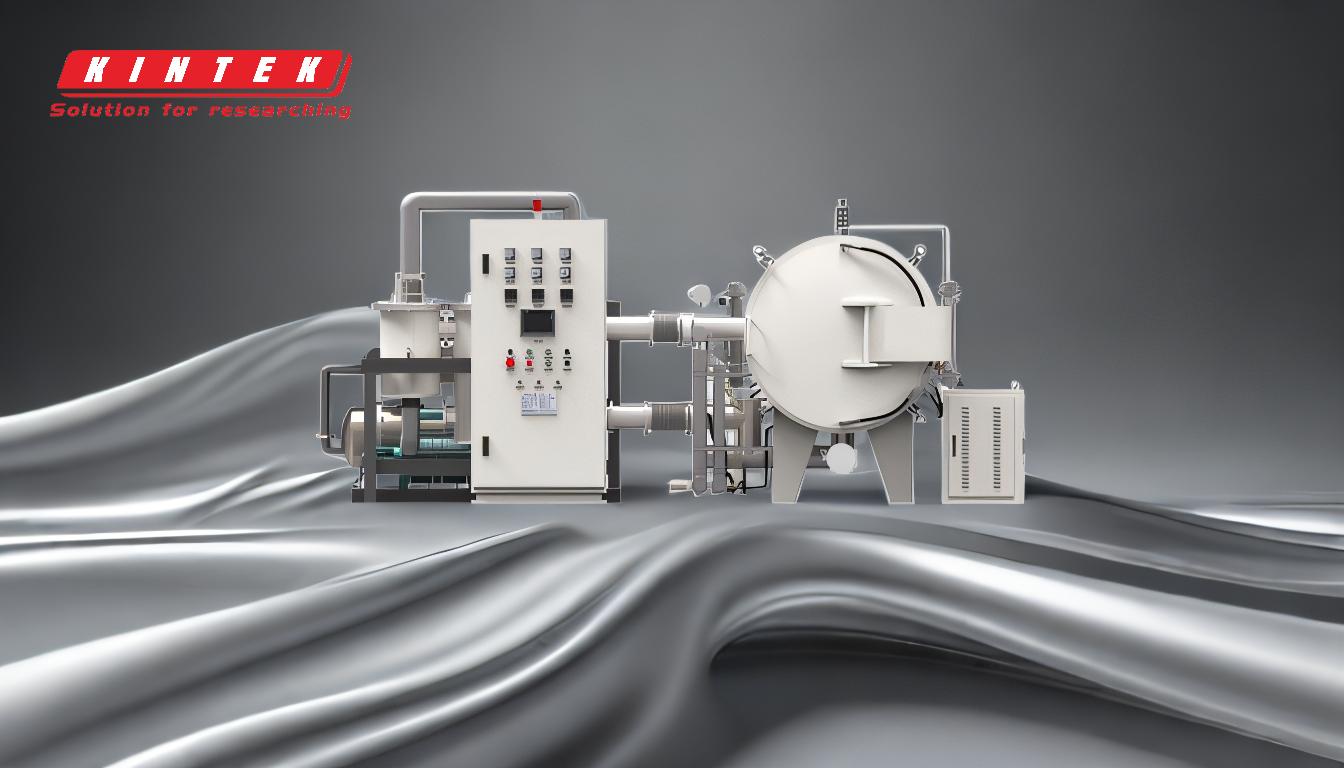
-
Temperature:
- Role: Temperature is one of the most critical factors in thermal cracking. Higher temperatures provide the energy needed to break the chemical bonds in large hydrocarbon molecules.
- Optimal Range: Typically, thermal cracking occurs at temperatures between 450°C to 750°C. The exact temperature depends on the type of feedstock and the desired products.
- Impact: Higher temperatures generally increase the rate of cracking, leading to the production of lighter hydrocarbons. However, excessively high temperatures can lead to unwanted side reactions, such as coking (formation of solid carbon deposits).
-
Pressure:
- Role: Pressure affects the phase of the hydrocarbons and the rate of cracking reactions. Lower pressures favor the formation of gaseous products, while higher pressures can lead to more liquid products.
- Optimal Range: Thermal cracking is often conducted at low to moderate pressures, typically between 1 to 10 atmospheres. The choice of pressure depends on the desired product slate and the specific cracking process used.
- Impact: Lower pressures can enhance the formation of lighter hydrocarbons, but they may also increase the risk of coking. Higher pressures can reduce coking but may decrease the yield of lighter products.
-
Residence Time:
- Role: Residence time refers to the duration that the feedstock is exposed to the cracking conditions. It is crucial for controlling the extent of cracking and the distribution of products.
- Optimal Range: Residence times can vary widely depending on the process, ranging from a few seconds to several minutes. Shorter residence times are typically used in processes like steam cracking, while longer times may be used in delayed coking.
- Impact: Longer residence times allow for more extensive cracking, which can increase the yield of lighter products. However, excessive residence times can lead to over-cracking, producing unwanted by-products and increasing coking.
-
Feedstock Composition:
- Role: The type of hydrocarbon feedstock significantly influences the cracking process. Different feedstocks have varying molecular structures, which affect their cracking behavior.
- Types of Feedstock: Common feedstocks include naphtha, gas oil, and residues. Lighter feedstocks like naphtha crack more easily and produce higher yields of lighter products, while heavier feedstocks like residues require more severe conditions and produce more by-products.
- Impact: The choice of feedstock affects the temperature, pressure, and residence time required for optimal cracking. Heavier feedstocks may require higher temperatures and longer residence times but can also increase the risk of coking and produce more complex product slates.
-
Catalyst (if applicable):
- Role: While traditional thermal cracking does not use a catalyst, some modern processes, such as catalytic cracking, employ catalysts to enhance the cracking reactions.
- Impact: Catalysts can lower the activation energy required for cracking, allowing the process to occur at lower temperatures and pressures. This can improve the selectivity of the cracking process, leading to higher yields of desired products and reducing unwanted by-products.
-
Reactor Design:
- Role: The design of the reactor used for thermal cracking can influence the efficiency and effectiveness of the process. Reactor design affects heat transfer, mixing, and the distribution of residence times.
- Types of Reactors: Common reactor types include tubular reactors, fluidized bed reactors, and delayed coking drums. Each type has its advantages and disadvantages in terms of heat transfer, residence time control, and ease of operation.
- Impact: The choice of reactor design can affect the temperature and pressure profiles within the reactor, influencing the extent of cracking and the distribution of products. Proper reactor design is essential for achieving optimal cracking conditions and minimizing unwanted side reactions.
-
Quenching:
- Role: Quenching is the rapid cooling of the cracked products to stop further cracking reactions. This is crucial for controlling the final product distribution.
- Methods: Quenching can be achieved using water, steam, or other cooling media. The method and rate of quenching depend on the specific process and desired product slate.
- Impact: Effective quenching helps to preserve the desired product distribution by preventing over-cracking and the formation of unwanted by-products. It also helps to reduce the risk of coking in downstream equipment.
In summary, the conditions for thermal cracking are determined by a combination of temperature, pressure, residence time, feedstock composition, and reactor design. Each of these factors plays a crucial role in determining the efficiency of the cracking process and the quality of the final products. By carefully controlling these conditions, operators can optimize the cracking process to produce the desired mix of lighter hydrocarbons while minimizing unwanted by-products and operational issues such as coking.
Summary Table:
Factor | Role | Optimal Range | Impact |
---|---|---|---|
Temperature | Provides energy to break hydrocarbon bonds | 450°C to 750°C | Higher temps increase cracking but may cause coking |
Pressure | Affects phase and rate of cracking reactions | 1 to 10 atmospheres | Lower pressure favors lighter hydrocarbons but may increase coking risk |
Residence Time | Controls extent of cracking and product distribution | Seconds to minutes | Longer times increase lighter yields but risk over-cracking |
Feedstock | Influences cracking behavior based on molecular structure | Naphtha, gas oil, residues | Lighter feedstocks crack easier; heavier ones require more severe conditions |
Reactor Design | Affects heat transfer, mixing, and residence time distribution | Tubular, fluidized bed, delayed coking drums | Impacts efficiency and product distribution |
Quenching | Rapidly cools products to stop further cracking | Water, steam, or other cooling media | Preserves product distribution and reduces coking risk |
Optimize your thermal cracking process with expert guidance—contact us today!