Forging is a critical manufacturing process in the automotive industry, used to produce strong, durable, and high-performance components. It involves shaping metal using localized compressive forces, typically with hammers, presses, or dies. The automotive industry relies on various forging processes to create parts like crankshafts, connecting rods, gears, and suspension components. Each forging method offers unique advantages in terms of precision, material properties, and production efficiency. Understanding the different types of forging processes helps manufacturers select the most suitable method for specific automotive applications.
Key Points Explained:
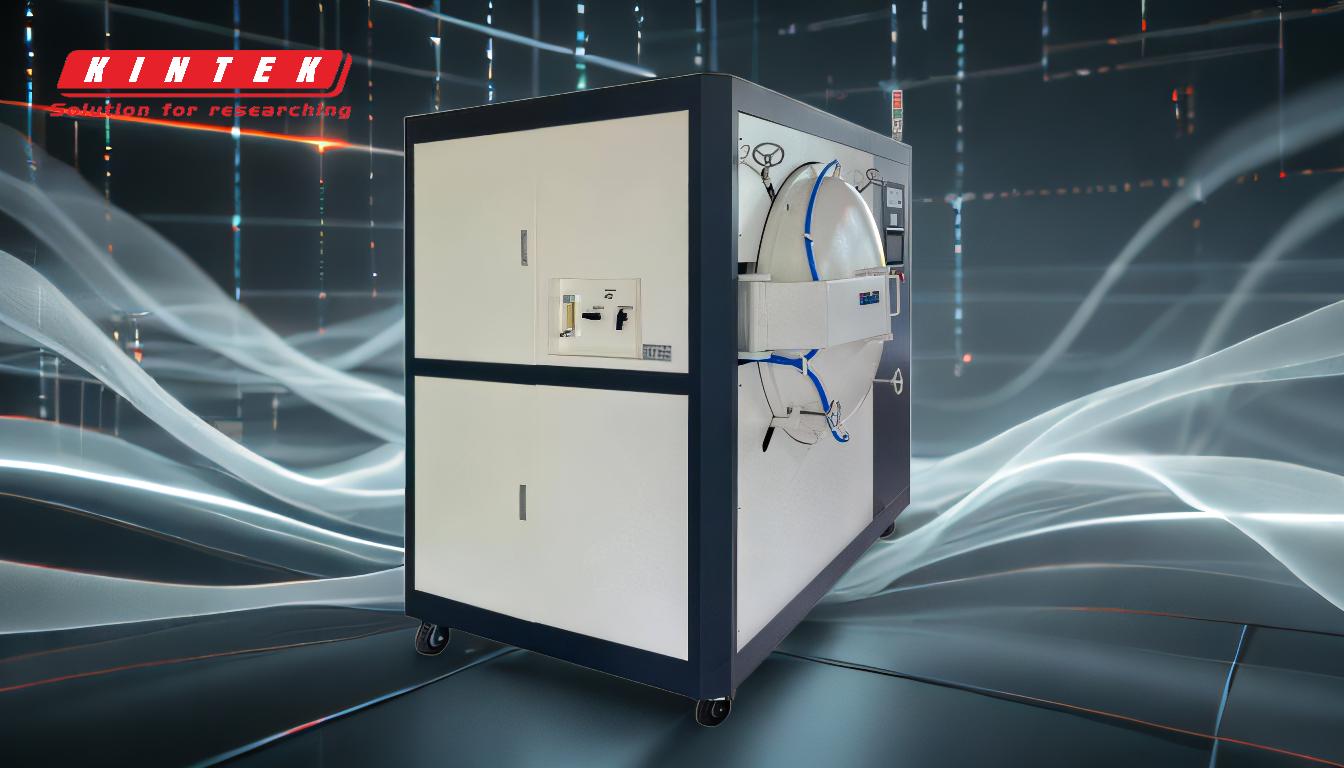
-
Open-Die Forging
- Description: Open-die forging, also known as free forging, involves deforming metal between flat or simple-shaped dies. The workpiece is not fully enclosed, allowing for flexibility in shape and size.
- Applications: Used for large, simple-shaped components like shafts, rings, and cylinders in the automotive industry.
-
Advantages:
- Suitable for large parts.
- Allows for customization and flexibility.
- Enhances material strength and grain structure.
- Limitations: Less precise compared to closed-die forging, requiring additional machining for final dimensions.
-
Closed-Die Forging (Impression-Die Forging)
- Description: In closed-die forging, the metal is compressed between two or more dies that contain a precut profile of the desired part. The material flows into the die cavities to form the final shape.
- Applications: Commonly used for producing complex automotive parts like gears, crankshafts, and connecting rods.
-
Advantages:
- High precision and dimensional accuracy.
- Minimal material waste.
- Excellent mechanical properties due to controlled grain flow.
- Limitations: Higher tooling costs and limited to smaller to medium-sized parts.
-
Roll Forging
- Description: Roll forging involves passing the metal between two rotating rolls with shaped grooves. The rolls compress and shape the metal as it passes through.
- Applications: Used for producing long, tapered components like axles, levers, and leaf springs in vehicles.
-
Advantages:
- Efficient for long parts with consistent cross-sections.
- Reduces material waste and improves surface finish.
- Limitations: Limited to parts with simple geometries and requires specialized equipment.
-
Upset Forging
- Description: Upset forging increases the diameter of a metal workpiece by compressing its length. This process is typically performed using horizontal or vertical presses.
- Applications: Ideal for creating bolt heads, valves, and other components with enlarged ends.
-
Advantages:
- Enhances material strength and density.
- Suitable for high-volume production.
- Limitations: Limited to parts with localized enlargements and requires precise control of material flow.
-
Isothermal Forging
- Description: Isothermal forging is performed at a constant temperature, typically using heated dies to maintain the workpiece temperature throughout the process.
- Applications: Used for high-performance components like turbine blades and aerospace parts, but also applicable in automotive for specialized applications.
-
Advantages:
- Produces parts with superior mechanical properties.
- Reduces residual stresses and improves dimensional accuracy.
- Limitations: High equipment and energy costs, making it less common for standard automotive parts.
-
Precision Forging
- Description: Precision forging is a near-net-shape process that produces parts with minimal machining requirements. It uses highly accurate dies to achieve tight tolerances.
- Applications: Suitable for critical automotive components like gears, transmission parts, and steering components.
-
Advantages:
- Reduces material waste and machining time.
- Enhances part strength and fatigue resistance.
- Limitations: High initial tooling costs and requires advanced equipment.
-
Cold Forging
- Description: Cold forging is performed at or near room temperature, using high-pressure dies to shape the metal.
- Applications: Commonly used for producing fasteners, bolts, and small automotive components.
-
Advantages:
- Improves material strength and surface finish.
- Cost-effective for high-volume production.
- Limitations: Limited to smaller parts and requires high-pressure equipment.
-
Hot Forging
- Description: Hot forging involves heating the metal above its recrystallization temperature to make it more malleable. The heated metal is then shaped using dies or presses.
- Applications: Widely used for producing large automotive parts like crankshafts, connecting rods, and suspension components.
-
Advantages:
- Allows for complex shapes and large parts.
- Enhances material ductility and reduces deformation resistance.
- Limitations: Higher energy consumption and potential for oxidation or scaling.
Each forging process offers distinct benefits and is chosen based on the specific requirements of the automotive component being manufactured. Factors like part complexity, material properties, production volume, and cost considerations play a crucial role in selecting the appropriate forging method. By leveraging these processes, the automotive industry can produce high-quality, durable, and reliable components that meet the demands of modern vehicles.
Summary Table:
Forging Process | Description | Applications | Advantages | Limitations |
---|---|---|---|---|
Open-Die Forging | Deforms metal between flat or simple-shaped dies. | Large, simple-shaped components like shafts, rings, and cylinders. | Suitable for large parts, customizable, enhances material strength. | Less precise, requires additional machining. |
Closed-Die Forging | Compresses metal between dies with precut profiles. | Complex parts like gears, crankshafts, and connecting rods. | High precision, minimal waste, excellent mechanical properties. | Higher tooling costs, limited to smaller to medium-sized parts. |
Roll Forging | Shapes metal between rotating rolls with grooves. | Long, tapered components like axles, levers, and leaf springs. | Efficient for long parts, reduces waste, improves surface finish. | Limited to simple geometries, requires specialized equipment. |
Upset Forging | Increases diameter by compressing length. | Bolt heads, valves, and components with enlarged ends. | Enhances strength and density, suitable for high-volume production. | Limited to localized enlargements, requires precise control. |
Isothermal Forging | Performed at constant temperature with heated dies. | High-performance components like turbine blades and aerospace parts. | Superior mechanical properties, reduces residual stresses. | High equipment and energy costs, less common for standard automotive parts. |
Precision Forging | Near-net-shape process with minimal machining. | Critical components like gears, transmission parts, and steering components. | Reduces waste and machining time, enhances strength and fatigue resistance. | High tooling costs, requires advanced equipment. |
Cold Forging | Shapes metal at or near room temperature using high-pressure dies. | Fasteners, bolts, and small automotive components. | Improves strength and surface finish, cost-effective for high-volume. | Limited to smaller parts, requires high-pressure equipment. |
Hot Forging | Heats metal above recrystallization temperature for shaping. | Large parts like crankshafts, connecting rods, and suspension components. | Allows complex shapes, enhances ductility, reduces deformation resistance. | Higher energy consumption, potential for oxidation or scaling. |
Need help selecting the right forging process for your automotive components? Contact our experts today for tailored solutions!