Physical Vapor Deposition (PVD) is a family of techniques used to deposit thin films of material onto a substrate. The primary methods include sputtering, thermal evaporation, electron-beam evaporation (e-beam evaporation), molecular beam epitaxy (MBE), ion plating, and pulsed laser deposition (PLD). These methods vary in their mechanisms, such as how the material is vaporized and deposited, but all involve the physical transfer of material from a source to a substrate without chemical reactions. Each method has unique advantages and is chosen based on the specific requirements of the application, such as film quality, deposition rate, and compatibility with the substrate material.
Key Points Explained:
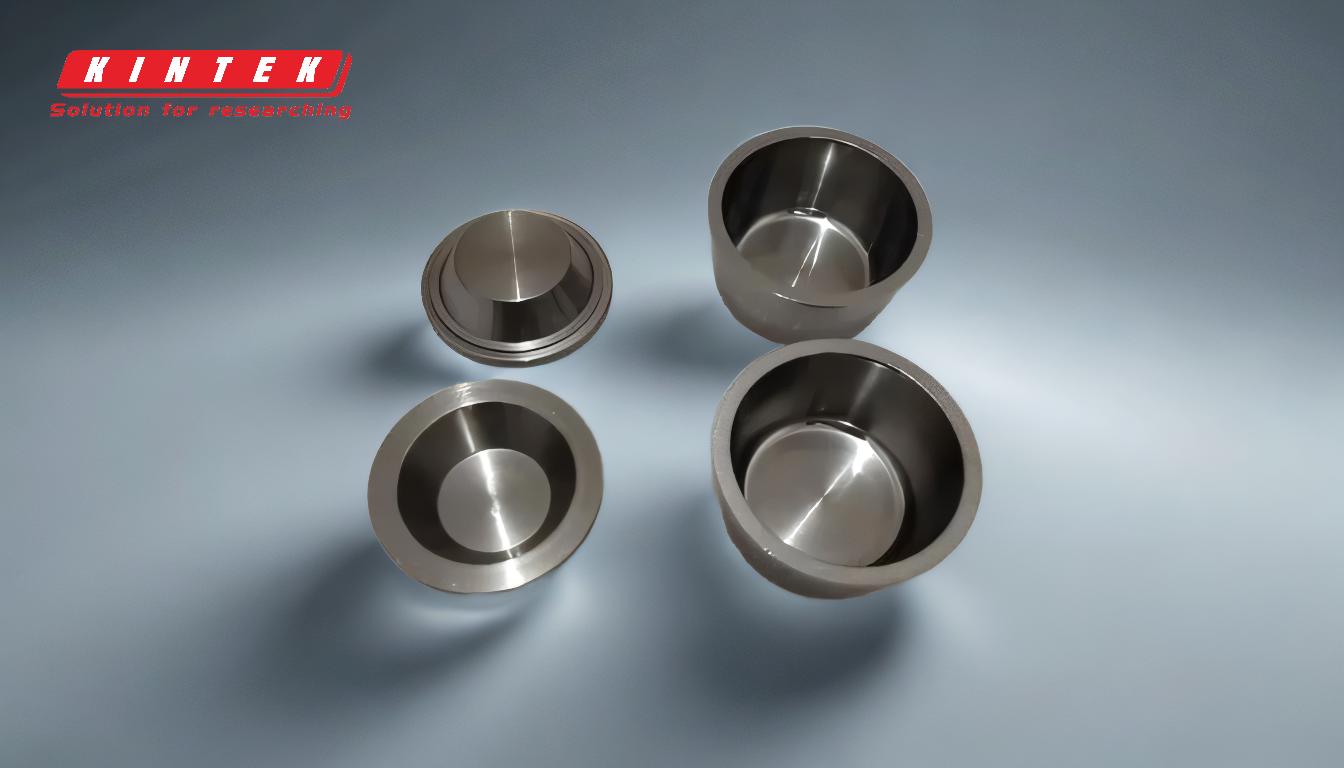
-
Sputtering:
- Process: Involves ejecting material from a target (source) by bombarding it with high-energy ions, typically in a vacuum environment. The ejected atoms then deposit onto the substrate.
- Types: Includes magnetron sputtering and ion beam sputtering.
- Applications: Widely used in the semiconductor industry, optical coatings, and decorative coatings due to its ability to deposit a wide range of materials with good adhesion and uniformity.
-
Thermal Evaporation:
- Process: Involves heating the source material in a vacuum until it vaporizes. The vapor then condenses on the cooler substrate to form a thin film.
- Types: Can be further divided into resistive heating evaporation and electron-beam evaporation.
- Applications: Commonly used for depositing metals and simple compounds in applications such as solar cells, OLEDs, and thin-film transistors.
-
Electron-Beam Evaporation (E-Beam Evaporation):
- Process: Uses a focused electron beam to heat and vaporize the source material in a vacuum. The vaporized material then deposits onto the substrate.
- Advantages: Allows for high-purity films and is suitable for materials with high melting points.
- Applications: Used in the production of high-performance optical coatings, semiconductor devices, and wear-resistant coatings.
-
Molecular Beam Epitaxy (MBE):
- Process: Involves the deposition of one or more materials onto a heated substrate in an ultra-high vacuum. The materials are evaporated from effusion cells and form a beam that deposits atom by atom on the substrate.
- Advantages: Enables precise control over film thickness and composition, making it ideal for producing high-quality crystalline films.
- Applications: Primarily used in the fabrication of semiconductor devices, such as quantum wells, superlattices, and other nanostructures.
-
Ion Plating:
- Process: Combines elements of sputtering and evaporation. The substrate is bombarded with ions during the deposition process, which improves film adhesion and density.
- Applications: Used in applications requiring strong adhesion and dense films, such as tool coatings and aerospace components.
-
Pulsed Laser Deposition (PLD):
- Process: Involves using a high-power pulsed laser to ablate material from a target, which then deposits onto the substrate.
- Advantages: Capable of depositing complex materials, such as oxides and nitrides, with high precision.
- Applications: Used in research and development for depositing thin films of complex materials, including high-temperature superconductors and ferroelectric materials.
-
Activated Reactive Evaporation (ARE):
- Process: Involves the evaporation of a material in the presence of a reactive gas, which reacts with the vapor to form a compound film on the substrate.
- Applications: Used for depositing compound films, such as nitrides and carbides, in applications like wear-resistant coatings and optical coatings.
-
Ionized Cluster Beam Deposition (ICBD):
- Process: Involves the formation of small clusters of atoms or molecules, which are ionized and then accelerated toward the substrate.
- Advantages: Provides good control over film morphology and can produce films with unique properties.
- Applications: Used in the deposition of thin films for electronic and optical devices.
Each of these PVD methods has its own set of advantages and limitations, making them suitable for different applications. The choice of method depends on factors such as the material to be deposited, the desired film properties, and the specific requirements of the application.
Summary Table:
Method | Process | Advantages | Applications |
---|---|---|---|
Sputtering | Ejects material from a target using high-energy ions. | Deposits a wide range of materials with good adhesion and uniformity. | Semiconductor industry, optical coatings, decorative coatings. |
Thermal Evaporation | Heats source material in a vacuum until it vaporizes. | Simple and effective for metals and simple compounds. | Solar cells, OLEDs, thin-film transistors. |
E-Beam Evaporation | Uses an electron beam to vaporize high-melting-point materials. | High-purity films, suitable for high-melting-point materials. | Optical coatings, semiconductor devices, wear-resistant coatings. |
MBE | Deposits materials atom by atom in an ultra-high vacuum. | Precise control over film thickness and composition. | Quantum wells, superlattices, nanostructures. |
Ion Plating | Combines sputtering and evaporation with ion bombardment. | Improves film adhesion and density. | Tool coatings, aerospace components. |
PLD | Uses a pulsed laser to ablate material from a target. | Deposits complex materials with high precision. | High-temperature superconductors, ferroelectric materials. |
ARE | Evaporates material in the presence of reactive gas to form compound films. | Deposits compound films like nitrides and carbides. | Wear-resistant coatings, optical coatings. |
ICBD | Ionizes and accelerates small clusters of atoms or molecules. | Provides control over film morphology and unique properties. | Electronic and optical devices. |
Discover the best PVD method for your application—contact our experts today!