Sintering is a critical process in ceramic manufacturing, involving the consolidation of powder particles into a dense solid through heat and sometimes pressure. Various sintering methods are employed depending on the material properties, desired outcomes, and production requirements. The most common types include Conventional Sintering, Spark Plasma Sintering (SPS), Microwave Sintering, Hot Press Sintering, Hot Isostatic Pressing (HIP), Vacuum Sintering, and Atmosphere Sintering. Each method has unique advantages, such as improved mechanical properties, reduced oxidation, or enhanced densification, and is chosen based on the specific needs of the ceramic material being processed.
Key Points Explained:
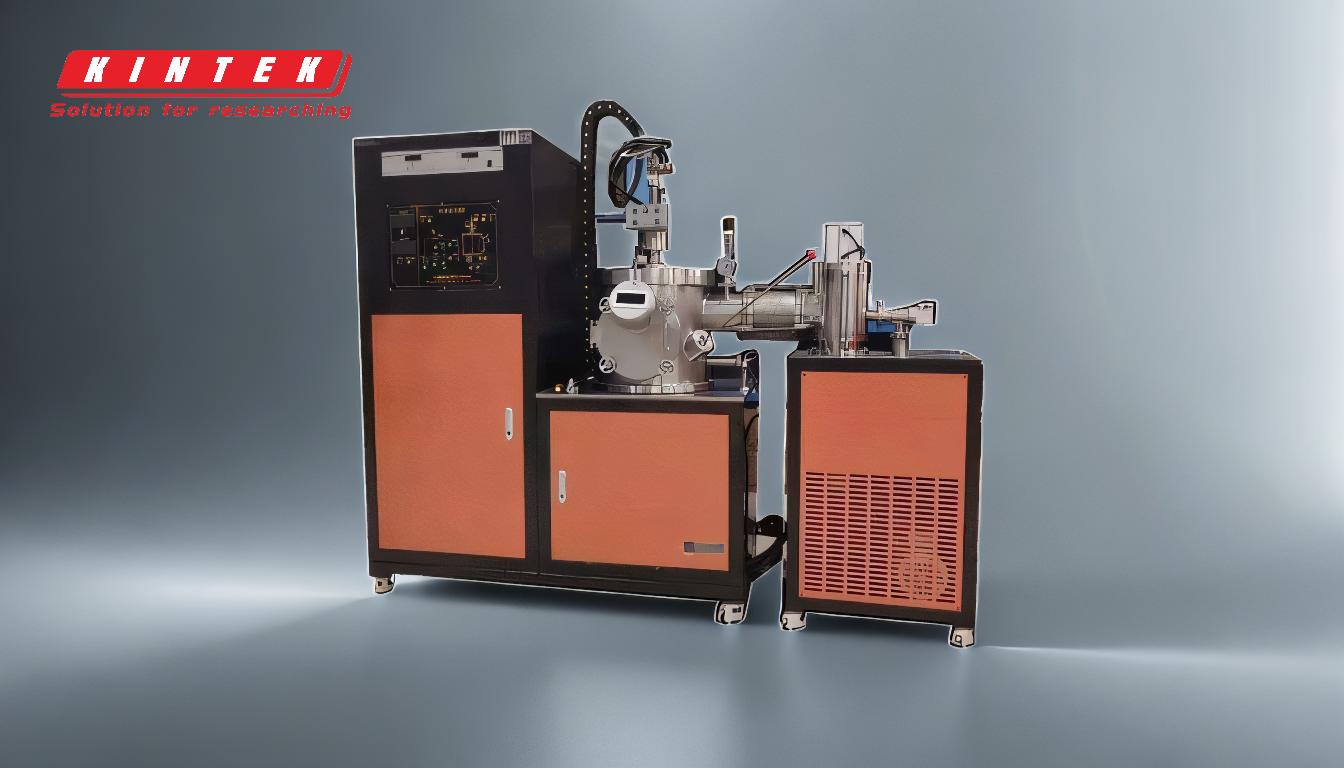
-
Conventional Sintering:
- Process: Involves heating a powder compact in a furnace without applying external pressure.
- Applications: Widely used for traditional ceramics like porcelain and structural ceramics.
- Advantages: Simple and cost-effective, suitable for large-scale production.
- Limitations: May result in lower density and mechanical properties compared to advanced methods.
-
Spark Plasma Sintering (SPS):
- Process: Utilizes pulsed electric current and pressure to achieve rapid densification at lower temperatures.
- Applications: Ideal for advanced ceramics, composites, and nanomaterials.
- Advantages: Faster processing times, improved microstructure control, and enhanced mechanical properties.
- Limitations: High equipment costs and limited scalability for large components.
-
Microwave Sintering:
- Process: Uses microwave energy to heat the material uniformly, often resulting in faster heating rates.
- Applications: Suitable for ceramics requiring precise temperature control and uniform heating.
- Advantages: Energy-efficient, reduced processing times, and minimized thermal gradients.
- Limitations: Limited to materials that absorb microwave energy effectively.
-
Hot Press Sintering:
- Process: Combines heat and uniaxial pressure to achieve densification.
- Applications: Used for high-performance ceramics and composites.
- Advantages: Higher density and improved mechanical properties compared to conventional sintering.
- Limitations: Higher equipment costs and complexity.
-
Hot Isostatic Pressing (HIP):
- Process: Applies high temperature and isostatic pressure (from all directions) to eliminate porosity.
- Applications: Common in aerospace and biomedical ceramics.
- Advantages: Produces near-net-shape components with exceptional density and uniformity.
- Limitations: Expensive and requires specialized equipment.
-
Vacuum Sintering:
- Process: Conducted in a vacuum environment to prevent oxidation and contamination.
- Applications: Suitable for high-purity ceramics and materials sensitive to oxidation.
- Advantages: Enhanced material properties and reduced impurities.
- Limitations: Requires vacuum equipment, increasing costs.
-
Atmosphere Sintering:
- Process: Performed in a controlled atmosphere (e.g., nitrogen, argon) to protect the material from reactions with the environment.
- Applications: Used for non-oxide ceramics and materials requiring specific atmospheres.
- Advantages: Prevents oxidation and contamination, improving material quality.
- Limitations: Higher operational complexity and costs.
-
Liquid Phase Sintering (LPS):
- Process: Involves the presence of a liquid phase that accelerates densification and bonding.
- Applications: Common in ceramics with low melting point additives.
- Advantages: Enhances densification and reduces sintering temperatures.
- Limitations: Requires careful control of the liquid phase composition.
-
Direct Metal Laser Sintering (DMLS):
- Process: A 3D printing technique that uses a laser to sinter metal powder layer by layer.
- Applications: Used for producing complex metal components and prototypes.
- Advantages: High precision and design flexibility.
- Limitations: Limited to metals and high costs.
-
High-Temperature Sintering:
- Process: Involves sintering at elevated temperatures to improve material properties.
- Applications: Suitable for advanced technical ceramics.
- Advantages: Reduces surface oxidation and enhances mechanical properties.
- Limitations: Requires specialized high-temperature furnaces.
Each sintering method has its unique benefits and limitations, and the choice of method depends on the specific requirements of the ceramic material and the desired properties of the final product. Understanding these differences is crucial for selecting the most appropriate sintering technique for a given application.
Summary Table:
Sintering Method | Process | Applications | Advantages | Limitations |
---|---|---|---|---|
Conventional Sintering | Heating without external pressure | Porcelain, structural ceramics | Simple, cost-effective, scalable | Lower density, mechanical properties |
Spark Plasma Sintering (SPS) | Pulsed electric current and pressure | Advanced ceramics, composites, nanomaterials | Faster processing, improved microstructure control | High costs, limited scalability |
Microwave Sintering | Microwave energy for uniform heating | Ceramics requiring precise temperature control | Energy-efficient, reduced processing times | Limited to microwave-absorbing materials |
Hot Press Sintering | Heat and uniaxial pressure | High-performance ceramics, composites | Higher density, improved mechanical properties | High costs, complex equipment |
Hot Isostatic Pressing (HIP) | High temperature and isostatic pressure | Aerospace, biomedical ceramics | Near-net-shape components, exceptional density | Expensive, specialized equipment |
Vacuum Sintering | Conducted in a vacuum to prevent oxidation | High-purity ceramics, oxidation-sensitive materials | Enhanced material properties, reduced impurities | Requires vacuum equipment, higher costs |
Atmosphere Sintering | Controlled atmosphere (e.g., nitrogen, argon) | Non-oxide ceramics, specific atmosphere materials | Prevents oxidation, improves material quality | Higher operational complexity and costs |
Liquid Phase Sintering (LPS) | Presence of a liquid phase for densification | Ceramics with low melting point additives | Enhanced densification, lower sintering temperatures | Requires careful control of liquid phase composition |
Direct Metal Laser Sintering (DMLS) | Laser sintering of metal powder layers | Complex metal components, prototypes | High precision, design flexibility | Limited to metals, high costs |
High-Temperature Sintering | Elevated temperatures for improved properties | Advanced technical ceramics | Reduces oxidation, enhances mechanical properties | Requires specialized high-temperature furnaces |
Need help selecting the right sintering method for your ceramics? Contact our experts today for personalized guidance!