Ceramic fibers, while offering excellent thermal insulation properties, come with several notable disadvantages that can impact their performance and safety in various applications. These include poor stability under certain conditions, susceptibility to erosion and peeling, and vulnerability to short-circuiting when contaminated. These drawbacks can limit their effectiveness and require careful consideration when selecting materials for high-temperature environments or electrical insulation.
Key Points Explained:
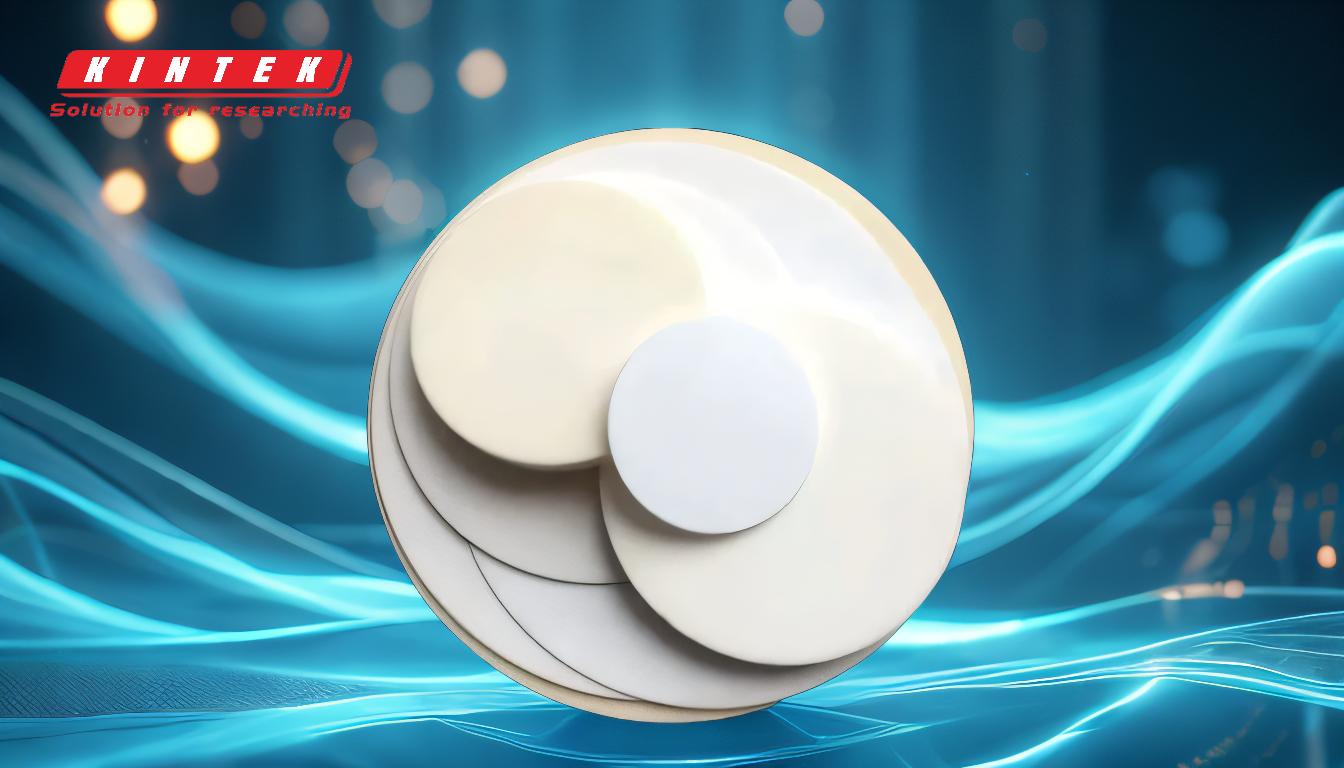
-
Poor Stability:
- Explanation: Ceramic fibers may exhibit poor stability under specific conditions, such as prolonged exposure to high temperatures or thermal cycling. This instability can lead to degradation of the material over time, reducing its insulating properties and structural integrity.
- Implications: In applications where consistent performance is critical, such as in industrial furnaces or aerospace components, the poor stability of ceramic fibers can result in frequent maintenance or replacement, increasing operational costs and downtime.
-
Poor Resistance to Erosion:
- Explanation: Ceramic fibers are prone to erosion, particularly when exposed to high-velocity air flows or abrasive particles. This erosion can cause the fibers to wear away, leading to a loss of insulation thickness and effectiveness.
- Implications: In environments where air flow or particulate matter is present, such as in power plants or chemical processing facilities, the erosion of ceramic fibers can compromise their insulating capabilities, potentially leading to heat loss or equipment damage.
-
Air Flow Erosion and Peeling Off:
- Explanation: Similar to general erosion, ceramic fibers are also susceptible to peeling off when subjected to air flow erosion. This peeling can result in the detachment of fiber layers, further reducing the material's insulating properties.
- Implications: The peeling off of ceramic fibers can create uneven insulation surfaces, leading to hot spots or thermal inefficiencies. This can be particularly problematic in applications requiring uniform temperature distribution, such as in heat treatment processes.
-
Vulnerability to Short-Circuiting:
- Explanation: Ceramic insulators made from ceramic fibers can be vulnerable to short-circuiting if they become contaminated with carbon dust, metallic condensates, or other conductive materials. These contaminants can create conductive paths, leading to electrical failures.
- Implications: In electrical insulation applications, such as in high-voltage equipment or electronic components, the risk of short-circuiting due to contamination can pose significant safety hazards and lead to equipment failure. Regular cleaning and maintenance are required to mitigate this risk, adding to the operational burden.
-
Contamination Issues:
- Explanation: Ceramic fibers can be easily contaminated by process by-products, such as graphite insulation, part fixtures, or contaminants present on the workload. These contaminants can affect the material's performance and longevity.
- Implications: Contamination can reduce the effectiveness of ceramic fibers as insulators, leading to increased energy consumption, reduced equipment lifespan, and potential safety risks. Ensuring a clean environment and proper handling of ceramic fiber materials is essential to maintain their performance.
In summary, while ceramic fibers offer significant advantages in thermal insulation, their disadvantages—such as poor stability, susceptibility to erosion and peeling, vulnerability to short-circuiting, and contamination issues—must be carefully considered. These limitations can impact their performance, safety, and cost-effectiveness in various applications, necessitating thorough evaluation and appropriate mitigation strategies when selecting materials for specific uses.
Summary Table:
Disadvantage | Explanation | Implications |
---|---|---|
Poor Stability | Degrades under high temperatures or thermal cycling | Increased maintenance, higher costs, and downtime in critical applications |
Poor Resistance to Erosion | Wears away under high-velocity air flows or abrasive particles | Insulation loss, heat inefficiency, and potential equipment damage |
Air Flow Erosion & Peeling | Fibers peel off, creating uneven insulation surfaces | Hot spots, thermal inefficiencies, and reduced performance in heat treatment |
Vulnerability to Short-Circuiting | Contamination with conductive materials causes electrical failures | Safety hazards, equipment failure, and increased maintenance needs |
Contamination Issues | Easily contaminated by process by-products or environmental factors | Reduced insulation effectiveness, higher energy use, and shorter equipment life |
Need help selecting the right insulation material? Contact our experts today for tailored solutions!