Rotary kiln incinerators, while effective for waste disposal, come with several notable disadvantages. These include high capital and operating costs, the need for trained personnel, and significant maintenance expenses due to the abrasive nature of waste and high temperatures. Additionally, rotary kilns suffer from low heat conversion efficiency, poor temperature control, and a short lifespan. Safety hazards such as electric leakage and gas fires are also concerns, alongside environmental pollution issues. These factors make rotary kilns less eco-friendly and subject to stringent regulations, while also posing challenges in operational efficiency and product quality.
Key Points Explained:
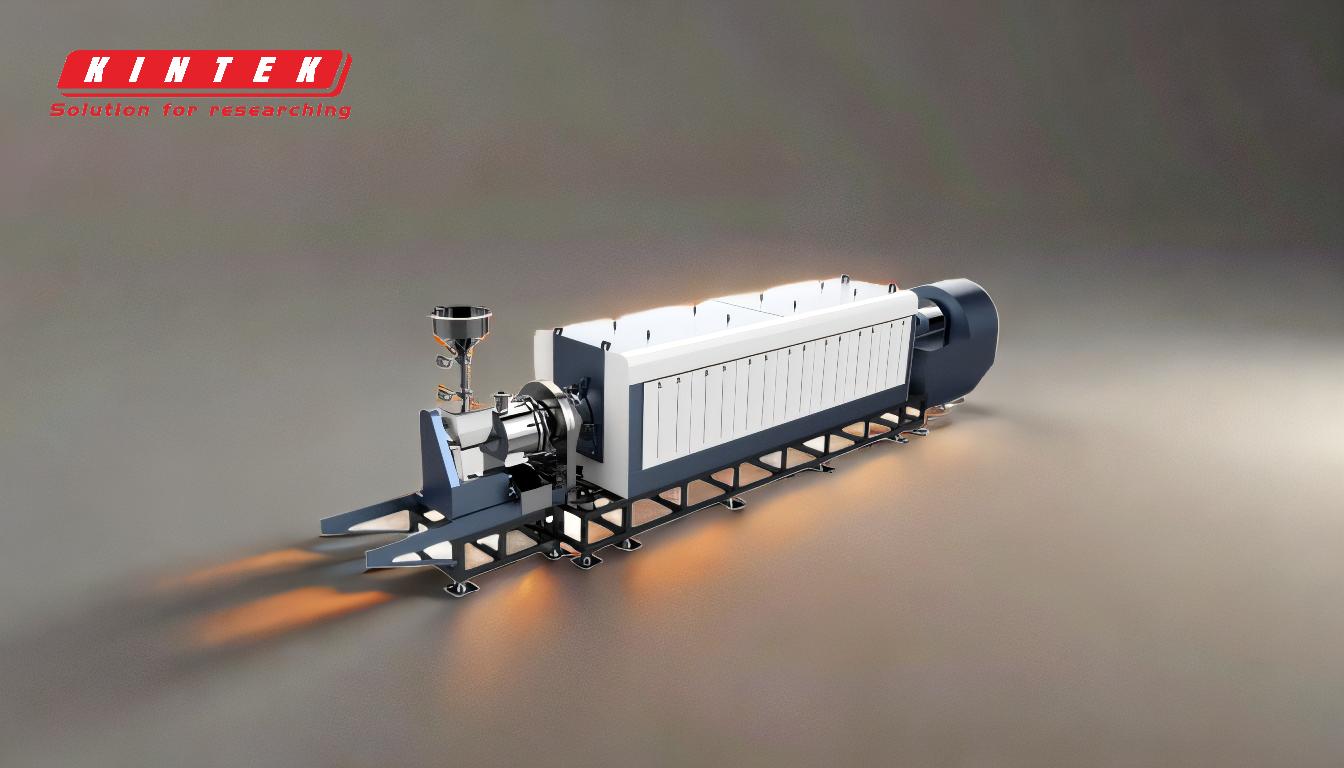
-
High Capital and Operating Costs:
- Rotary kiln incinerators require substantial initial investment and ongoing operational expenses. This includes the cost of equipment, installation, and energy consumption.
- The need for specialized materials to withstand high temperatures and abrasive waste further drives up costs.
-
Need for Trained Personnel:
- Operating a rotary kiln incinerator requires skilled personnel to manage the complex processes and ensure safety.
- Training and retaining such personnel can be costly and time-consuming.
-
High Maintenance Costs:
- The abrasive nature of the waste and the high temperatures within the kiln lead to frequent wear and tear of moving parts.
- Regular maintenance is necessary to prevent breakdowns, which can be both expensive and labor-intensive.
-
Low Heat Conversion Efficiency:
- Rotary kilns typically have a heat conversion efficiency of only 30%-70%, meaning a significant portion of the energy input is wasted.
- This inefficiency increases operational costs and reduces the overall effectiveness of the incineration process.
-
Poor Temperature Control:
- Inaccurate temperature control can lead to inconsistent product quality, lower yields, and color variations in the output.
- This lack of precision can affect the overall performance and reliability of the kiln.
-
Short Lifespan and Difficult Maintenance:
- The harsh operating conditions within a rotary kiln contribute to a relatively short lifespan of the equipment.
- Maintenance is challenging due to the high temperatures and the need to frequently replace worn-out parts.
-
Significant Safety Hazards:
- Rotary kilns pose risks such as electric leakage, electric shock, and gas leakage fires.
- These safety concerns require stringent safety measures and protocols, adding to the complexity and cost of operations.
-
Environmental Pollution:
- The incineration process in rotary kilns can produce pollutants, making them less environmentally friendly.
- Compliance with environmental and safety regulations can be burdensome and costly.
-
Challenges with Material Mixing and Temperature Variations:
- Not all materials tumble well in the kiln, leading to poor mixing and large temperature variations.
- This can reduce the efficiency of the kiln and affect the quality of the end product.
-
Dust Generation and Non-Uniform Product Quality:
- Rotary kilns can generate significant amounts of dust, which can be a nuisance and a health hazard.
- The non-uniform quality of the product can be a drawback for industries requiring consistent output.
In summary, while rotary kiln incinerators are effective for waste disposal, their high costs, maintenance challenges, safety hazards, and environmental impacts make them less attractive compared to other waste disposal methods. These disadvantages need to be carefully considered when evaluating the suitability of rotary kilns for specific applications.
Summary Table:
Disadvantages of Rotary Kiln Incinerators | Key Details |
---|---|
High Capital and Operating Costs | Substantial initial investment and ongoing expenses for equipment, installation, and energy. |
Need for Trained Personnel | Skilled operators required, increasing labor costs and training time. |
High Maintenance Costs | Frequent wear and tear due to abrasive waste and high temperatures. |
Low Heat Conversion Efficiency | Only 30%-70% efficiency, leading to energy waste. |
Poor Temperature Control | Inconsistent product quality and lower yields. |
Short Lifespan and Difficult Maintenance | Harsh conditions reduce equipment lifespan and increase repair complexity. |
Safety Hazards | Risks include electric leakage, shock, and gas fires. |
Environmental Pollution | Produces pollutants, making compliance costly. |
Material Mixing and Temperature Variations | Poor mixing and large temperature variations reduce efficiency. |
Dust Generation and Non-Uniform Product | Dust is a health hazard, and product quality is inconsistent. |
Considering the challenges of rotary kiln incinerators? Contact our experts to explore better waste disposal solutions!