Brazing is a metal-joining process that involves heating a filler metal to its melting point and allowing it to flow into the joint between two or more close-fitting parts. The essential steps in a brazing operation ensure a strong, clean, and reliable joint. These steps include preparing the joint, cleaning the surfaces, assembling the parts, heating the assembly to the brazing temperature, and post-brazing cleaning and inspection. Each step is critical to achieving a high-quality brazed joint.
Key Points Explained:
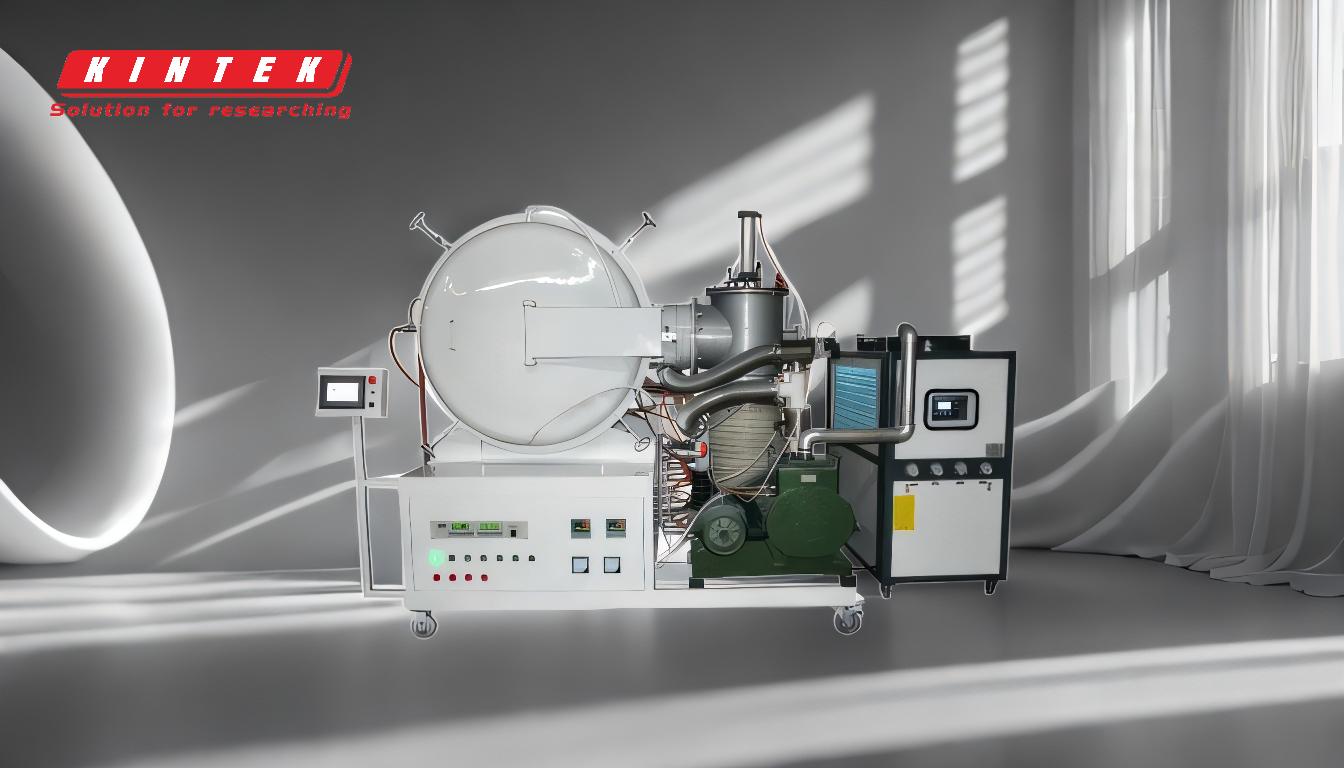
-
Joint Preparation:
- Fit and Gap Width: The first step in brazing is to ensure that the joint is properly designed and that the gap between the parts is within the recommended range. The ideal gap width is typically between 0.001 to 0.005 inches (0.025 to 0.127 mm). This gap allows the filler metal to flow into the joint by capillary action, creating a strong bond.
- Surface Cleanliness: The surfaces to be brazed must be free from contaminants such as oil, grease, oxide layers, and dirt. Contaminants can prevent the filler metal from wetting the surfaces properly, leading to weak joints. Cleaning methods include chemical cleaning, mechanical abrasion, or degreasing.
-
Cleaning the Metal Surfaces:
- Chemical Cleaning: This involves using solvents, acids, or alkaline solutions to remove oils, greases, and oxides from the metal surfaces. The choice of cleaning agent depends on the type of metal and the nature of the contaminants.
- Mechanical Cleaning: Methods such as wire brushing, sandblasting, or grinding can be used to remove heavy oxides or scale from the surfaces. Mechanical cleaning is often followed by chemical cleaning to ensure complete removal of contaminants.
- Degreasing: This step involves removing any residual oils or greases that may be present on the surfaces. Degreasing can be done using solvents or vapor degreasing techniques.
-
Assembling the Parts:
- Alignment: The parts to be brazed must be aligned accurately to ensure that the joint is properly filled with the filler metal. Misalignment can lead to gaps or voids in the joint, reducing its strength. Clamps, fixtures, or jigs are often used to hold the parts in place during the brazing process.
- Filler Metal Placement: The filler metal is placed in or near the joint before heating. It can be in the form of wire, foil, powder, or pre-placed rings. The filler metal should be positioned so that it melts and flows into the joint by capillary action when the assembly is heated.
-
Heating the Assembly:
- Temperature Control: The assembly is heated to a temperature above the melting point of the filler metal but below the melting point of the base metals. The heating must be uniform to ensure that the filler metal flows evenly into the joint. The temperature is typically controlled using a furnace, torch, or induction heating.
- Atmosphere Control: In some brazing processes, such as vacuum brazing or controlled atmosphere brazing, the heating is done in an environment that prevents oxidation of the metal surfaces. This is especially important for metals that are prone to oxidation, such as stainless steel or titanium.
-
Post-Brazing Cleaning and Inspection:
- Cleaning: After the brazing process, the assembly may need to be cleaned to remove any residual flux, oxides, or other contaminants. Cleaning methods include water rinsing, chemical cleaning, or mechanical cleaning.
- Inspection: The brazed joint should be inspected to ensure that it meets the required quality standards. Inspection methods include visual inspection, dye penetrant testing, X-ray inspection, or ultrasonic testing. The goal is to ensure that the joint is free from defects such as voids, cracks, or incomplete filling.
By following these essential steps, a high-quality brazed joint can be achieved, ensuring the strength, durability, and reliability of the assembly. Each step is critical, and attention to detail is required to produce a successful brazed joint.
Summary Table:
Step | Key Actions |
---|---|
Joint Preparation | - Ensure proper fit and gap width (0.001–0.005 inches). |
- Clean surfaces to remove contaminants. | |
Cleaning the Surfaces | - Use chemical or mechanical methods to remove oils, oxides, and dirt. |
Assembling the Parts | - Align parts accurately. |
- Place filler metal in or near the joint. | |
Heating the Assembly | - Heat uniformly above filler metal’s melting point. |
- Control atmosphere to prevent oxidation. | |
Post-Brazing Cleaning & Inspection | - Clean residual flux or oxides. |
- Inspect for defects using visual or advanced methods. |
Need expert guidance on brazing? Contact us today to achieve flawless metal joints!