Batch furnaces are widely used in heat treatment processes for metals, offering flexibility in handling various types of materials and heat treatment requirements. They are particularly suitable for low-volume production, large-sized parts, or specialized treatments like deep case carburizing. Common examples of batch furnaces include box-type, bogie-hearth, salt bath, muffle, pit, sealed-quench, bell, tempering, vacuum, and fluidized-bed furnaces. These furnaces operate by heating a batch of components to a specific temperature, holding it for a set duration, and then cooling it at a controlled rate. Batch furnaces are versatile, cost-effective, and can operate with or without controlled atmospheres, making them ideal for diverse industrial applications.
Key Points Explained:
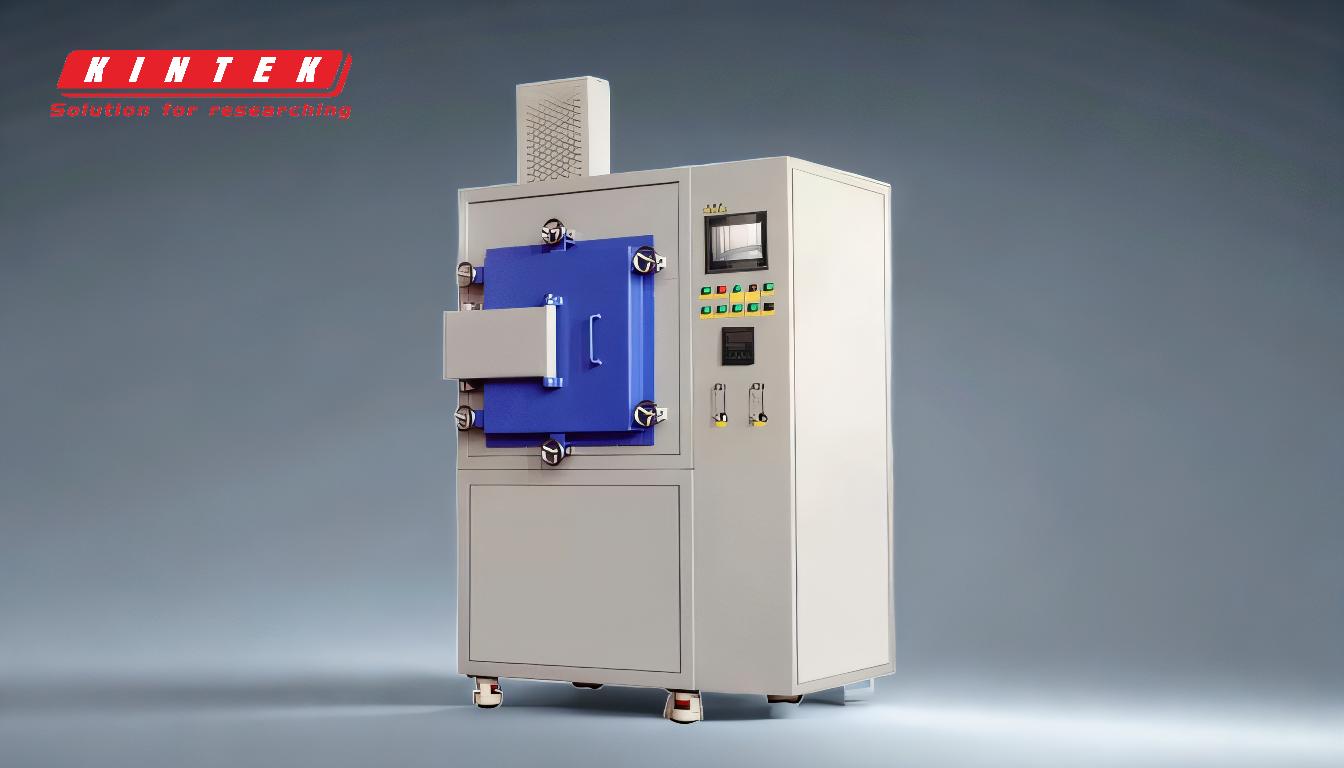
-
Box-Type Batch Furnaces:
- Description: These are rectangular or box-shaped furnaces with a front-loading door. They are versatile and can handle a wide range of heat treatment processes, including annealing, hardening, and tempering.
- Applications: Commonly used for small to medium-sized batches of parts, especially in tool and die manufacturing or aerospace industries.
-
Bogie-Hearth Furnaces:
- Description: These furnaces feature a movable hearth (bogie) that can be rolled in and out of the furnace chamber. This design facilitates easy loading and unloading of heavy or large components.
- Applications: Ideal for large or heavy parts, such as forgings, castings, or large machinery components.
-
Salt Bath Furnaces:
- Description: These furnaces use molten salt as the heating medium, providing uniform and rapid heating. The salt bath also acts as a protective atmosphere, preventing oxidation.
- Applications: Suitable for processes like hardening, tempering, and surface treatments, especially for tool steels and high-speed steels.
-
Muffle Furnaces:
- Description: These furnaces have a separate chamber (muffle) that isolates the heating elements from the workpiece, ensuring a clean and controlled environment.
- Applications: Used for processes requiring contamination-free heating, such as brazing, sintering, or laboratory testing.
-
Pit Furnaces:
- Description: These are vertical furnaces where parts are loaded from the top. They are designed to handle long or tall components, such as shafts or tubes.
- Applications: Commonly used in the automotive and aerospace industries for heat treating long components like drive shafts or landing gear.
-
Sealed-Quench Furnaces:
- Description: These furnaces combine heating and quenching in a single, sealed unit. They are designed to minimize distortion and oxidation during the quenching process.
- Applications: Ideal for processes like carburizing, hardening, and quenching of precision components.
-
Bell Furnaces:
- Description: These furnaces consist of a removable bell-shaped cover that is placed over the workpiece. They are often used with controlled atmospheres for specialized heat treatments.
- Applications: Suitable for annealing, brazing, and stress-relieving of large coils or sheets.
-
Tempering Furnaces:
- Description: Specifically designed for tempering processes, these furnaces operate at lower temperatures compared to other batch furnaces.
- Applications: Used to reduce brittleness and improve toughness in hardened steel components.
-
Vacuum Furnaces:
- Description: These furnaces operate in a vacuum environment, eliminating oxidation and contamination. They are highly precise and can achieve very high temperatures.
- Applications: Ideal for critical applications in aerospace, medical, and tooling industries, where contamination-free heat treatment is essential.
-
Fluidized-Bed Furnaces:
- Description: These furnaces use a bed of solid particles suspended by a gas flow, creating a fluid-like medium for heat transfer. They offer rapid and uniform heating.
- Applications: Used for processes like annealing, tempering, and surface treatments, especially for small or delicate parts.
By understanding the specific features and applications of each type of batch furnace, purchasers can make informed decisions based on their production needs, part sizes, and heat treatment requirements.
Summary Table:
Type of Batch Furnace | Key Features | Applications |
---|---|---|
Box-Type | Rectangular, front-loading door | Annealing, hardening, tempering |
Bogie-Hearth | Movable hearth for heavy parts | Forging, casting, large machinery |
Salt Bath | Molten salt heating, oxidation prevention | Hardening, tempering, tool steels |
Muffle | Isolated chamber for contamination-free heating | Brazing, sintering, lab testing |
Pit | Vertical loading for tall components | Automotive, aerospace long parts |
Sealed-Quench | Combines heating and quenching | Carburizing, hardening, precision parts |
Bell | Removable bell cover, controlled atmosphere | Annealing, brazing, stress-relieving |
Tempering | Lower temperature operations | Reducing brittleness in steel |
Vacuum | Contamination-free, high precision | Aerospace, medical, tooling |
Fluidized-Bed | Rapid, uniform heating with gas flow | Annealing, tempering, delicate parts |
Need help choosing the right batch furnace for your heat treatment process? Contact our experts today!