The rate of melting is influenced by several factors, including the material's properties, environmental conditions, and external energy sources. Understanding these factors is crucial for optimizing processes in industries such as metallurgy, food processing, and materials science. Key factors include the material's thermal conductivity, specific heat capacity, and melting point, as well as external factors like temperature, pressure, and the presence of impurities. Additionally, the method of heat transfer (conduction, convection, or radiation) and the geometry of the material being melted also play significant roles. By controlling these variables, one can effectively manage the melting rate to achieve desired outcomes in various applications.
Key Points Explained:
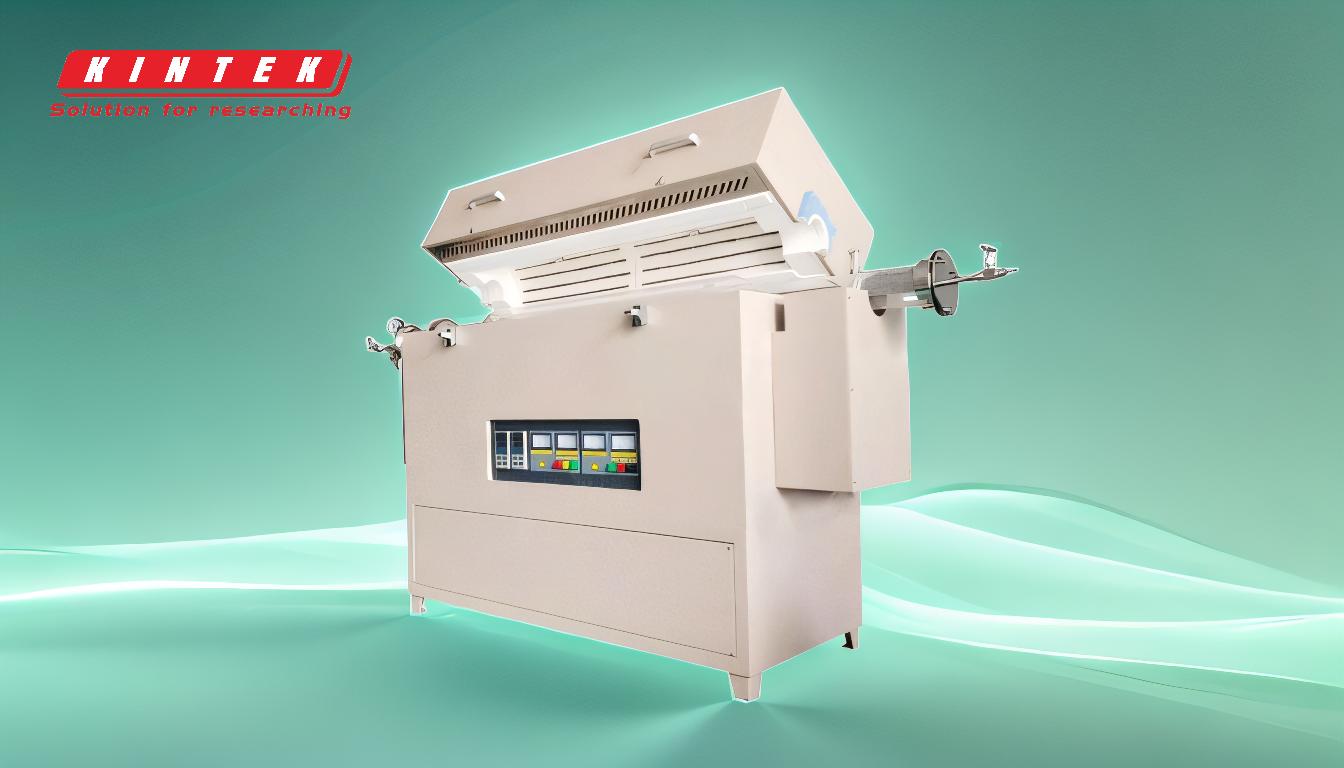
-
Material Properties:
- Thermal Conductivity: Materials with high thermal conductivity, such as metals, melt faster because they transfer heat more efficiently. For example, copper melts quicker than plastic due to its superior thermal conductivity.
- Specific Heat Capacity: Materials with low specific heat capacity require less energy to raise their temperature, leading to a faster melting rate. For instance, ice melts faster than wax because ice has a lower specific heat capacity.
- Melting Point: Materials with lower melting points, like ice, melt more quickly than those with higher melting points, such as steel. The melting point is a critical factor in determining the energy required to initiate and sustain melting.
-
Environmental Conditions:
- Temperature: Higher ambient temperatures accelerate the melting process by providing more energy to the material. For example, ice melts faster in a warm room than in a freezer.
- Pressure: Changes in pressure can affect the melting point of a material. Increased pressure generally raises the melting point, requiring more energy to melt the material. Conversely, reduced pressure can lower the melting point, facilitating faster melting.
- Impurities: The presence of impurities can alter the melting behavior of a material. Impurities often lower the melting point and can create localized areas of faster melting. For example, salt added to ice lowers its melting point, causing it to melt more quickly.
-
External Energy Sources:
- Heat Transfer Methods: The method of heat transfer significantly impacts the melting rate. Conduction, convection, and radiation each have different efficiencies in transferring heat to the material. For instance, conduction is highly effective in metals, while convection might be more efficient in liquids.
- Energy Input Rate: The rate at which energy is supplied to the material directly affects the melting speed. Higher energy input rates, such as using a more powerful heat source, can significantly increase the melting rate.
-
Geometry and Surface Area:
- Surface Area: Materials with larger surface areas relative to their volume melt faster because more area is exposed to the heat source. For example, crushed ice melts faster than a solid ice block due to its increased surface area.
- Shape and Thickness: The shape and thickness of the material also influence the melting rate. Thin materials or those with shapes that maximize heat exposure, such as flakes or powders, tend to melt more quickly than thick or bulky materials.
-
Phase Change Considerations:
- Latent Heat of Fusion: The amount of energy required to change a material from solid to liquid without changing its temperature is known as the latent heat of fusion. Materials with lower latent heat of fusion values melt more quickly because they require less energy to undergo the phase change.
- Supercooling: In some cases, materials can be cooled below their melting point without solidifying, a phenomenon known as supercooling. When such materials are heated, they may melt more rapidly once the melting point is reached.
By understanding and manipulating these factors, one can control the rate of melting to suit specific industrial or scientific needs. Whether it's optimizing the melting process in a foundry or ensuring uniform melting in food production, these principles are fundamental to achieving efficient and effective outcomes.
Summary Table:
Category | Key Factors | Impact on Melting Rate |
---|---|---|
Material Properties | Thermal Conductivity, Specific Heat Capacity, Melting Point | High thermal conductivity, low specific heat capacity, and low melting point speed up melting. |
Environmental Conditions | Temperature, Pressure, Impurities | Higher temperature and lower pressure accelerate melting; impurities can lower melting point. |
External Energy Sources | Heat Transfer Methods (Conduction, Convection, Radiation), Energy Input Rate | Efficient heat transfer and higher energy input rates increase melting speed. |
Geometry and Surface Area | Surface Area, Shape, Thickness | Larger surface area and thinner shapes melt faster due to increased heat exposure. |
Phase Change Considerations | Latent Heat of Fusion, Supercooling | Lower latent heat of fusion and supercooling can lead to faster melting. |
Need help optimizing your melting processes? Contact our experts today for tailored solutions!