Brazing, while a highly effective joining process, comes with several hazards that need to be carefully managed to ensure safety and quality. The primary risks include thermal distortion, uneven heating, improper braze flow, and potential cracking or splattering during rapid cooling. Additionally, safety precautions such as wearing protective equipment, ensuring proper ventilation, and handling materials safely are critical to mitigate risks like burns, inhalation of fumes, and fire hazards. Understanding these hazards and implementing appropriate measures can significantly reduce the likelihood of accidents and ensure successful brazing operations.
Key Points Explained:
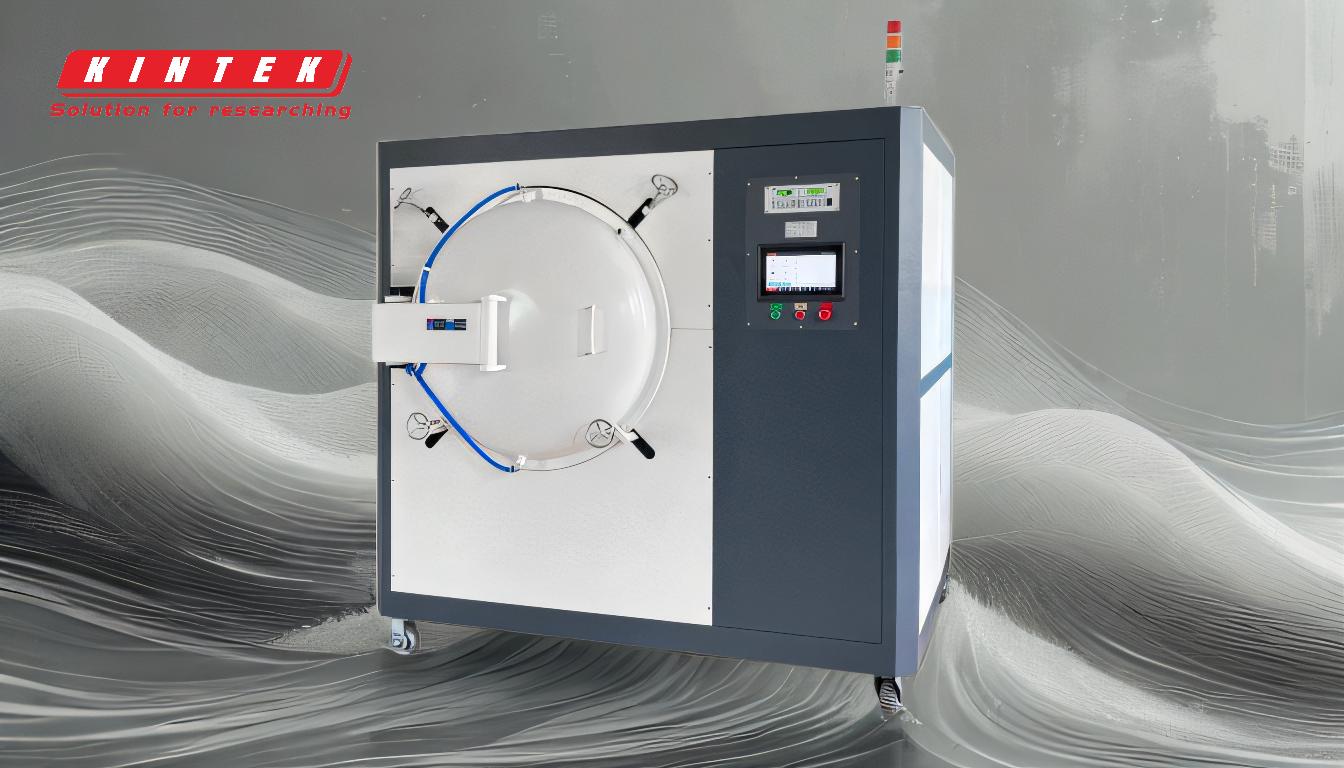
-
Thermal Distortion and Uneven Heating
- Cause: Rapid heating or cooling during the brazing process can lead to thermal distortion. This occurs when different parts of the assembly heat up or cool down at uneven rates, causing stress and warping.
- Impact: Distortion can compromise the structural integrity of the assembly, leading to misalignment or failure of the joint. Uneven heating can also result in improper braze flow, where the filler metal does not distribute evenly, weakening the bond.
- Prevention: To avoid this, it is crucial to control the heating and cooling rates. Gradual temperature changes allow the assembly to stabilize, ensuring even heat distribution and proper braze flow.
-
Quench Cracking and Splatter
- Cause: Rapid quenching, or cooling, can cause thermal shock, leading to cracks in the braze joint. Splatter occurs when the molten filler metal is ejected due to sudden temperature changes or improper handling.
- Impact: Quench cracking weakens the joint, making it prone to failure under stress. Splatter can cause safety hazards, such as burns or damage to nearby equipment.
- Prevention: Controlled cooling rates and proper handling of the assembly during the brazing process can minimize these risks. Using appropriate quenching mediums and techniques is essential.
-
Safety Precautions
- Protective Equipment: Wearing heat-resistant gloves, safety goggles, and protective clothing is essential to protect against burns and other injuries.
- Ventilation: Brazing often involves the use of fluxes and filler metals that can release harmful fumes. Working in a well-ventilated area or using fume extraction systems reduces the risk of inhaling toxic substances.
- Fire Safety: Having a fire extinguisher nearby and following safe material handling procedures can prevent fires caused by sparks or hot materials.
-
Material Handling and Preparation
- Cause: Improper preparation of the assembly, such as inadequate cleaning or improper fit-up, can lead to poor braze flow and weak joints.
- Impact: Poor material preparation can result in incomplete bonding, porosity, or contamination of the joint, reducing its strength and durability.
- Prevention: Thoroughly cleaning the surfaces to be joined and ensuring proper fit-up are critical steps. Using appropriate fluxes and filler metals also contributes to a successful brazing process.
-
Environmental and Health Hazards
- Cause: The use of fluxes and filler metals can release hazardous fumes, dust, or particulates during brazing.
- Impact: Exposure to these substances can cause respiratory issues, skin irritation, or long-term health problems.
- Prevention: Implementing proper ventilation, using personal protective equipment (PPE), and following safety guidelines can mitigate these risks.
By understanding and addressing these hazards, brazing can be performed safely and effectively, ensuring high-quality joints and minimizing risks to personnel and equipment.
Summary Table:
Hazard | Cause | Impact | Prevention |
---|---|---|---|
Thermal Distortion | Rapid heating or cooling causing uneven stress and warping | Compromised structural integrity, misalignment, or joint failure | Control heating and cooling rates; ensure gradual temperature changes |
Quench Cracking & Splatter | Rapid cooling causing thermal shock or improper handling of molten metal | Joint weakening, burns, or equipment damage | Use controlled cooling rates and proper quenching techniques |
Safety Precautions | Lack of protective equipment, poor ventilation, or unsafe material handling | Burns, inhalation of fumes, or fire hazards | Wear PPE, ensure proper ventilation, and follow fire safety protocols |
Material Handling | Improper cleaning, fit-up, or use of incorrect fluxes/filler metals | Weak joints, porosity, or contamination | Clean surfaces thoroughly, ensure proper fit-up, and use appropriate materials |
Environmental Hazards | Release of hazardous fumes, dust, or particulates | Respiratory issues, skin irritation, or long-term health problems | Use ventilation systems, PPE, and follow safety guidelines |
Ensure safe and effective brazing operations—contact our experts today for personalized guidance!