Additive manufacturing, commonly known as 3D printing, has seen rapid advancements in recent years, revolutionizing industries from healthcare to aerospace. The latest technologies in this field focus on improving precision, speed, material versatility, and scalability. Innovations such as multi-material printing, AI-driven design optimization, and advanced post-processing techniques are pushing the boundaries of what can be achieved. Additionally, the integration of IoT and cloud-based platforms is enabling smarter, more efficient manufacturing processes. These advancements are not only enhancing the quality and functionality of printed objects but also making additive manufacturing more accessible and cost-effective for a wider range of applications.
Key Points Explained:
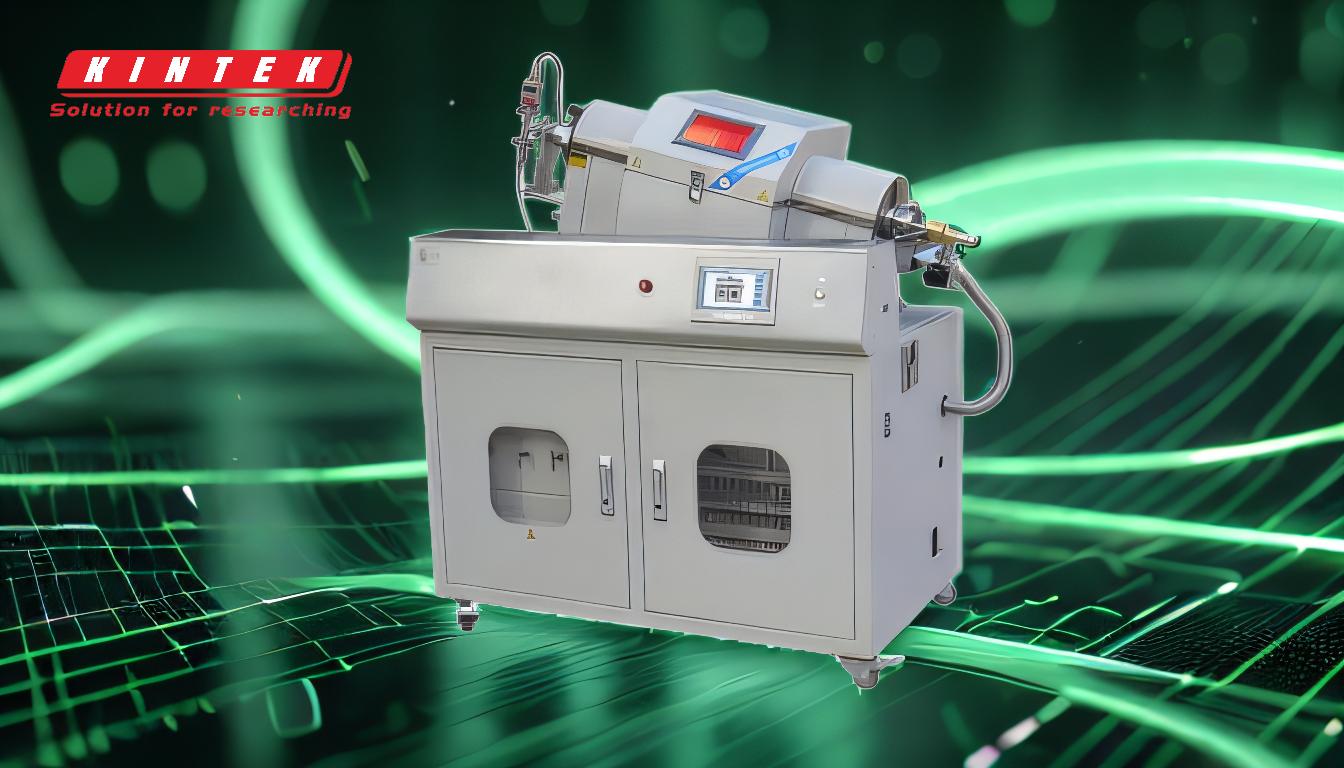
-
Multi-Material Printing:
- Explanation: Traditional 3D printing often limits users to a single material per print. However, the latest technologies allow for the simultaneous use of multiple materials, enabling the creation of more complex and functional objects. This is particularly useful in industries like healthcare, where implants can be made with both rigid and flexible materials to better mimic natural tissues.
- Impact: This technology expands the possibilities for product design and functionality, allowing for the creation of objects with varying mechanical properties within a single print.
-
AI-Driven Design Optimization:
- Explanation: Artificial intelligence is being integrated into additive manufacturing to optimize designs for strength, weight, and material usage. AI algorithms can analyze and modify designs in real-time, ensuring that the final product meets specific performance criteria.
- Impact: This reduces material waste and production time while improving the overall quality and performance of printed objects. It also allows for more complex geometries that were previously impossible to achieve.
-
Advanced Post-Processing Techniques:
- Explanation: Post-processing is a critical step in additive manufacturing that involves finishing the printed object to meet desired specifications. New techniques, such as automated polishing, chemical smoothing, and advanced heat treatments, are being developed to enhance the surface finish and mechanical properties of printed parts.
- Impact: These techniques improve the durability and aesthetic quality of printed objects, making them more suitable for end-use applications in industries like automotive and consumer goods.
-
Integration of IoT and Cloud-Based Platforms:
- Explanation: The Internet of Things (IoT) and cloud computing are being integrated into additive manufacturing to create smarter, more connected production environments. IoT devices can monitor and control the printing process in real-time, while cloud-based platforms enable remote design, simulation, and collaboration.
- Impact: This leads to more efficient manufacturing processes, reduced downtime, and the ability to scale production more easily. It also facilitates collaboration across global teams, accelerating innovation and time-to-market.
-
High-Speed Printing Technologies:
- Explanation: Speed has always been a challenge in additive manufacturing, but new technologies are addressing this issue. Techniques like Continuous Liquid Interface Production (CLIP) and High-Speed Sintering (HSS) are significantly reducing print times while maintaining high levels of precision.
- Impact: Faster printing speeds make additive manufacturing more viable for large-scale production, opening up new opportunities in industries like construction and mass customization.
-
Material Innovations:
- Explanation: The range of materials available for additive manufacturing is continually expanding. New polymers, metals, ceramics, and composites are being developed to meet the specific needs of various industries. For example, biocompatible materials are being used in medical applications, while high-strength alloys are being employed in aerospace.
- Impact: These material innovations are enabling the production of more durable, functional, and specialized products, further broadening the applications of additive manufacturing.
-
Scalability and Industrial Adoption:
- Explanation: As additive manufacturing technologies mature, they are becoming more scalable and suitable for industrial applications. Large-format 3D printers and automated production lines are being developed to meet the demands of high-volume manufacturing.
- Impact: This shift is making additive manufacturing a more attractive option for industries that require large-scale production, such as automotive and aerospace, where it can offer significant cost and time savings.
In summary, the latest technologies in additive manufacturing are focused on enhancing the capabilities, efficiency, and accessibility of 3D printing. These advancements are not only improving the quality and functionality of printed objects but also expanding the range of applications across various industries. As these technologies continue to evolve, they are likely to play an increasingly important role in the future of manufacturing.
Summary Table:
Technology | Key Features | Impact |
---|---|---|
Multi-Material Printing | Simultaneous use of multiple materials | Enables complex, functional objects with varying mechanical properties |
AI-Driven Design Optimization | Real-time design optimization for strength, weight, and material usage | Reduces waste, improves quality, and enables complex geometries |
Advanced Post-Processing | Automated polishing, chemical smoothing, and heat treatments | Enhances durability and surface finish for end-use applications |
IoT & Cloud Integration | Real-time monitoring, remote design, and collaboration | Improves efficiency, scalability, and global collaboration |
High-Speed Printing | Techniques like CLIP and HSS for faster printing | Makes large-scale production and mass customization feasible |
Material Innovations | New polymers, metals, ceramics, and biocompatible materials | Expands applications in healthcare, aerospace, and other industries |
Scalability & Industrial Adoption | Large-format printers and automated production lines | Enables cost-effective, high-volume manufacturing |
Ready to leverage the latest in additive manufacturing? Contact us today to learn how these technologies can transform your business!