Carbon nanotubes (CNTs) are versatile materials with applications ranging from conductive additives in lithium-ion batteries to advanced uses in concrete, films, and electronics. Their unique properties, such as high electrical conductivity, mechanical strength, and thermal stability, make them highly desirable in various industries. However, the synthesis of CNTs often results in impurities, including amorphous carbon, metal catalysts, and other carbonaceous materials. Purification is a critical step to ensure the quality and performance of CNTs in their intended applications. This answer explores the methods of carbon nanotube purification, focusing on their relevance to industries like energy storage, construction, and electronics.
Key Points Explained:
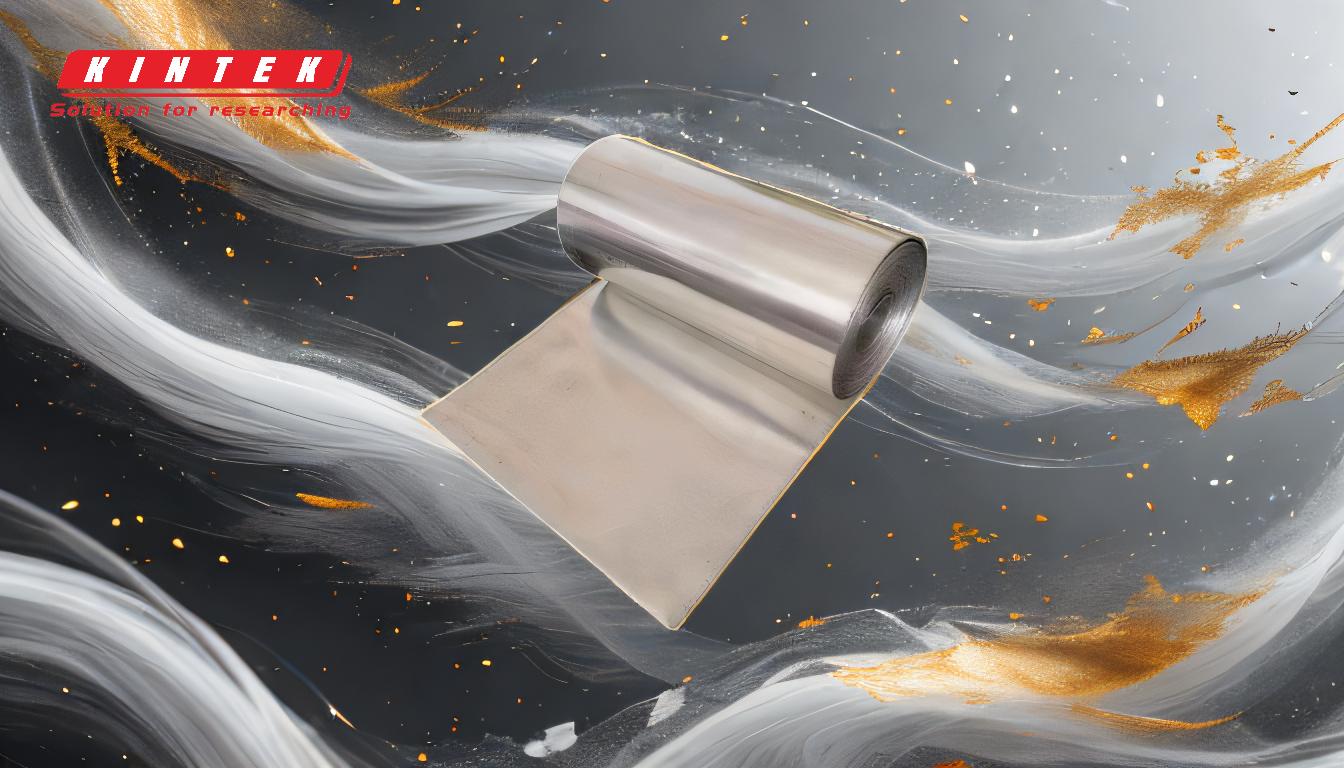
-
Introduction to Carbon Nanotube Purification
- Carbon nanotubes are synthesized through methods like chemical vapor deposition (CVD), arc discharge, and laser ablation. These processes often introduce impurities, such as metal catalyst particles, amorphous carbon, and graphitic nanoparticles.
- Purification aims to remove these impurities while preserving the structural integrity and properties of the CNTs. The choice of purification method depends on the type of impurities and the intended application of the CNTs.
-
Oxidation-Based Purification
- Oxidation is one of the most common methods for purifying CNTs. It involves exposing the CNTs to oxidizing agents like air, oxygen, or acids (e.g., nitric acid or sulfuric acid).
- The process selectively oxidizes and removes amorphous carbon and metal catalysts, which are more reactive than the CNTs themselves.
- Advantages: Effective for removing carbonaceous impurities and metal residues.
- Limitations: Over-oxidation can damage the CNTs, reducing their length and structural integrity.
-
Acid Treatment Purification
- Acid treatment involves refluxing CNTs in strong acids, such as nitric acid or a mixture of nitric and sulfuric acids. This method targets metal catalysts and amorphous carbon.
- The acids dissolve metal particles and oxidize carbonaceous impurities, leaving behind purified CNTs.
- Advantages: High efficiency in removing metal impurities and improving CNT dispersion in solvents.
- Limitations: Prolonged exposure to acids can introduce defects in the CNT structure, affecting their electrical and mechanical properties.
-
Filtration and Centrifugation
- Filtration and centrifugation are physical methods used to separate CNTs from impurities based on size and density differences.
- Filtration involves passing a CNT suspension through a membrane that retains larger impurities, while centrifugation separates components based on their sedimentation rates.
- Advantages: Non-destructive to CNT structure and suitable for large-scale purification.
- Limitations: Less effective for removing small-sized impurities like metal nanoparticles.
-
Chromatography-Based Purification
- Chromatography techniques, such as size exclusion chromatography (SEC) and gel permeation chromatography (GPC), are used to separate CNTs based on their size and molecular weight.
- These methods are particularly useful for isolating specific types of CNTs, such as single-walled CNTs (SWCNTs) from multi-walled CNTs (MWCNTs).
- Advantages: High selectivity and precision in separating CNTs.
- Limitations: Expensive and time-consuming, making them less suitable for industrial-scale purification.
-
Thermal Annealing
- Thermal annealing involves heating CNTs to high temperatures in an inert atmosphere to remove volatile impurities and graphitic particles.
- This method is effective for improving the crystallinity of CNTs and removing residual carbonaceous materials.
- Advantages: Enhances the structural quality of CNTs without introducing chemical contaminants.
- Limitations: Requires specialized equipment and may not remove metal catalysts effectively.
-
Combination Methods
- Many purification processes combine multiple techniques to achieve higher purity levels. For example, acid treatment followed by filtration or centrifugation can effectively remove both metal and carbonaceous impurities.
- Advantages: Comprehensive removal of impurities while minimizing damage to CNTs.
- Limitations: Increased complexity and cost of the purification process.
-
Emerging Purification Techniques
- Recent advancements include the use of supercritical fluids, microwave-assisted purification, and biological methods. These techniques aim to improve efficiency and reduce environmental impact.
- Supercritical Fluids: Utilize the unique properties of fluids at supercritical conditions to dissolve and remove impurities.
- Microwave-Assisted Purification: Uses microwave radiation to selectively heat and remove impurities.
- Biological Methods: Employ enzymes or microorganisms to degrade impurities.
-
Importance of Purification in Applications
- In lithium-ion batteries, purified CNTs enhance conductivity and stability, improving battery performance.
- In concrete and films, purified CNTs provide superior mechanical strength and durability.
- In electronics, high-purity CNTs are essential for achieving reliable and efficient devices.
By understanding and selecting the appropriate purification method, manufacturers can ensure the high quality and performance of carbon nanotubes in their specific applications. The choice of method depends on factors such as the type of impurities, the scale of production, and the desired properties of the CNTs.
Summary Table:
Method | Description | Advantages | Limitations |
---|---|---|---|
Oxidation-Based | Uses oxidizing agents to remove amorphous carbon and metal catalysts. | Effective for carbonaceous impurities and metal residues. | Over-oxidation can damage CNTs. |
Acid Treatment | Refluxes CNTs in strong acids to dissolve metal particles and oxidize impurities. | High efficiency in removing metal impurities. | Prolonged exposure can introduce defects. |
Filtration/Centrifugation | Separates CNTs from impurities based on size and density differences. | Non-destructive and suitable for large-scale purification. | Less effective for small-sized impurities. |
Chromatography-Based | Separates CNTs by size and molecular weight using techniques like SEC or GPC. | High selectivity and precision. | Expensive and time-consuming. |
Thermal Annealing | Heats CNTs in an inert atmosphere to remove volatile impurities. | Enhances structural quality without chemical contaminants. | May not remove metal catalysts effectively. |
Combination Methods | Combines multiple techniques for comprehensive impurity removal. | Minimizes damage to CNTs while achieving high purity. | Increased complexity and cost. |
Emerging Techniques | Includes supercritical fluids, microwave-assisted, and biological methods. | Improves efficiency and reduces environmental impact. | Still under development, scalability challenges. |
Need help selecting the right carbon nanotube purification method? Contact our experts today for tailored solutions!