Carbon nanotubes (CNTs) are primarily prepared using methods such as laser ablation, arc discharge, and chemical vapor deposition (CVD), with CVD being the most commercially dominant due to its cost-effectiveness and structural controllability. Emerging methods focus on sustainability, utilizing green or waste feedstocks like carbon dioxide and methane pyrolysis. The synthesis process, particularly in CVD, involves thermal treatments and catalyst deposition, which require careful management to minimize environmental impacts. Challenges in CNT production include functionalization, purification, and integration into macro-scale products, with post-processing and dispersion technologies playing a critical role in market success.
Key Points Explained:
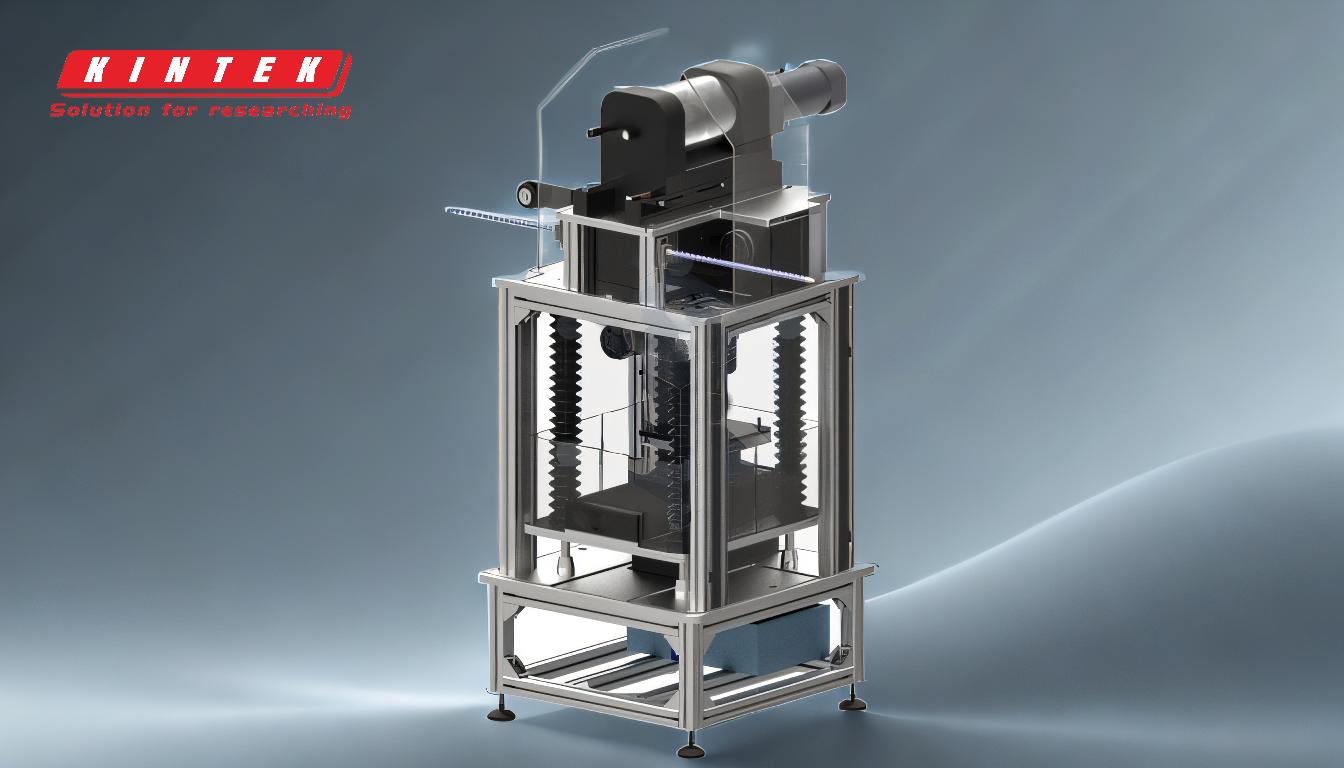
-
Traditional Methods of CNT Preparation:
- Laser Ablation: This method involves using a high-power laser to vaporize a carbon target in the presence of a catalyst. The vaporized carbon condenses to form CNTs. While effective, this method is less commercially viable due to high energy consumption and cost.
- Arc Discharge: In this technique, an electric arc is generated between two carbon electrodes in an inert gas atmosphere. The high temperature causes carbon atoms to vaporize and form CNTs. Although this method produces high-quality CNTs, it is also energy-intensive and not scalable for large-scale production.
-
Chemical Vapor Deposition (CVD):
- Dominant Commercial Process: CVD is the most widely used method for CNT production due to its scalability, cost-effectiveness, and ability to control the structure of the CNTs. It involves decomposing a carbon-containing gas (e.g., methane, ethylene) on a substrate coated with a catalyst at high temperatures.
- Catalytic Chemical Vapor Deposition (CCVD): A variant of CVD, CCVD uses a catalyst to facilitate the decomposition of the carbon source, leading to the growth of CNTs. This method allows for precise control over the diameter, length, and alignment of the nanotubes, making it highly suitable for industrial applications.
-
Emerging Sustainable Methods:
- Green Feedstocks: Researchers are exploring the use of sustainable carbon sources, such as carbon dioxide captured by electrolysis in molten salts. This approach not only reduces the environmental impact but also utilizes waste materials effectively.
- Methane Pyrolysis: Another emerging method involves the thermal decomposition of methane into hydrogen and solid carbon, which can then be used to synthesize CNTs. This process is considered environmentally friendly as it produces hydrogen as a byproduct, which can be used as a clean fuel.
-
Challenges in CNT Production:
- Functionalization and Purification: CNTs often require functionalization to improve their compatibility with other materials and purification to remove impurities. These processes can be complex and costly.
- Separation and Integration: Separating CNTs based on their properties (e.g., diameter, chirality) and integrating them into macro-scale products like sheets, veils, or yarns present significant technical challenges.
- Post-Processing and Dispersion: Effective post-processing and dispersion technologies are crucial for ensuring the uniform distribution of CNTs in composite materials, which is essential for achieving the desired mechanical, electrical, and thermal properties.
-
Environmental Considerations:
- Material and Energy Consumption: The synthesis process, particularly in CVD, involves significant material and energy consumption. Optimizing these parameters is essential to reduce the environmental footprint of CNT production.
- Greenhouse Gas Emissions: Limiting greenhouse gas emissions during the synthesis process is critical to minimizing the life cycle ecotoxicity of CNTs. This can be achieved through the use of sustainable feedstocks and energy-efficient processes.
In summary, while traditional methods like laser ablation and arc discharge are still used, CVD has become the dominant commercial process for CNT preparation due to its scalability and cost-effectiveness. Emerging methods focus on sustainability, utilizing green or waste feedstocks. However, challenges such as functionalization, purification, and integration into macro-scale products remain, with post-processing and dispersion technologies being critical for market success. Environmental considerations, including material and energy consumption and greenhouse gas emissions, are also key factors in the production of CNTs.
Summary Table:
Method | Description | Advantages | Challenges |
---|---|---|---|
Laser Ablation | Uses a high-power laser to vaporize carbon in the presence of a catalyst. | Produces high-quality CNTs. | High energy consumption, costly, and less scalable. |
Arc Discharge | Generates an electric arc between carbon electrodes in an inert gas atmosphere. | High-quality CNTs. | Energy-intensive and not suitable for large-scale production. |
Chemical Vapor Deposition (CVD) | Decomposes carbon-containing gas on a catalyst-coated substrate at high temperatures. | Scalable, cost-effective, and controllable CNT structure. | Requires careful management of environmental impacts. |
Emerging Sustainable Methods | Utilizes green feedstocks like CO2 and methane pyrolysis. | Reduces environmental impact and utilizes waste materials. | Limited commercial adoption and technical challenges in scalability. |
Interested in learning more about CNT preparation methods? Contact our experts today for tailored solutions!