Vacuum coating is a versatile technology used across various industries to apply thin films to surfaces, enhancing their performance, durability, and aesthetics. The methods of vacuum coating are diverse, each tailored to specific applications and materials. These methods include physical vapor deposition (PVD), chemical vapor deposition (CVD), and other specialized techniques. Each method has unique advantages, making them suitable for different industrial needs, such as creating optical coatings, wear-resistant layers, or decorative finishes. Below, we explore the key methods of vacuum coating in detail.
Key Points Explained:
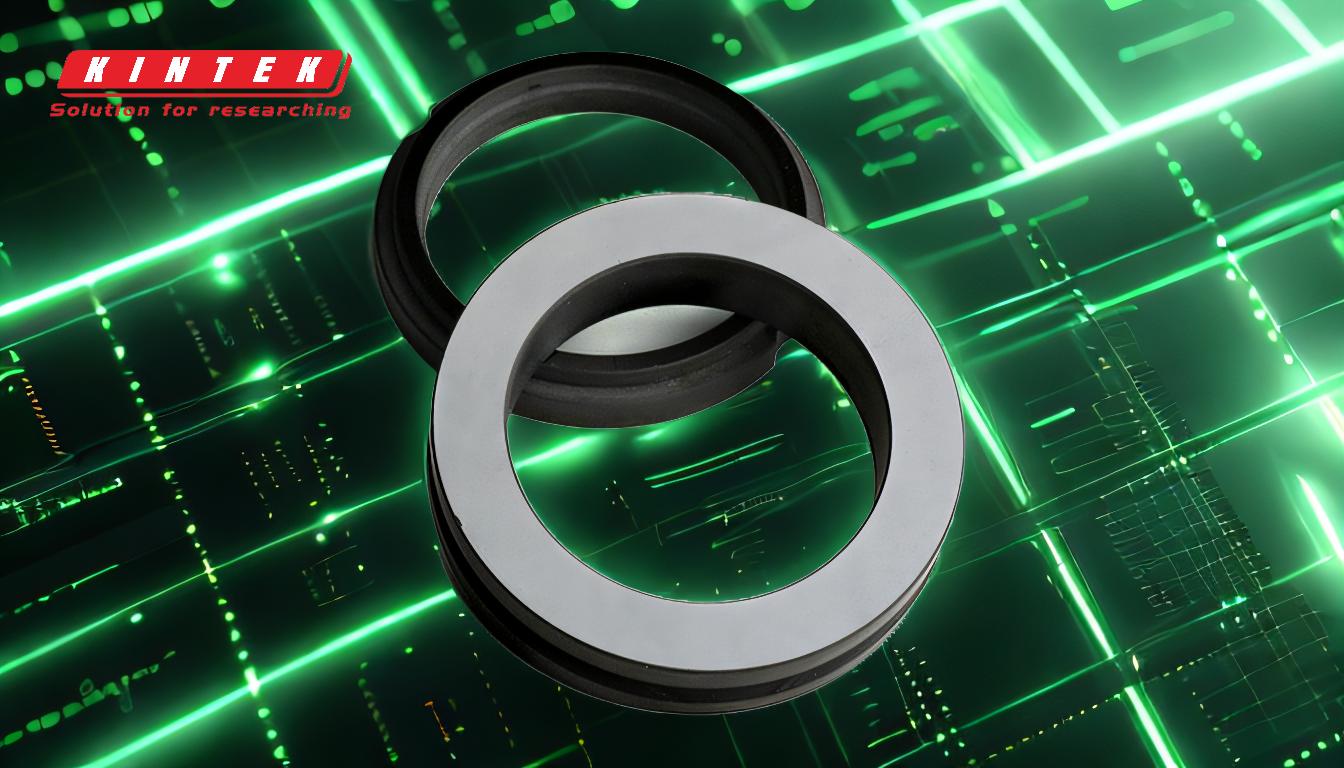
-
Physical Vapor Deposition (PVD)
- PVD is a widely used vacuum coating method where materials are vaporized in a vacuum environment and then deposited onto a substrate.
- Common PVD techniques include:
- Evaporation: A material is heated until it vaporizes, and the vapor condenses on the substrate. This method is often used for optical and decorative coatings.
- Sputtering: A target material is bombarded with ions, causing atoms to be ejected and deposited onto the substrate. Sputtering is ideal for creating wear-resistant and conductive coatings.
- PVD is favored for its ability to produce high-purity, durable coatings with excellent adhesion.
-
Chemical Vapor Deposition (CVD)
- CVD involves chemical reactions in a vacuum chamber to deposit a solid material onto a substrate.
- The process typically uses gaseous precursors that react at the substrate surface, forming a thin film.
- CVD is commonly used for creating hard coatings, such as those for engine components, and for depositing materials like silicon carbide and diamond-like carbon.
- Advantages of CVD include uniform coating thickness and the ability to coat complex geometries.
-
Ion Plating
- Ion plating combines PVD and plasma technology to enhance coating adhesion and density.
- In this process, ions are accelerated toward the substrate, improving the bonding between the coating and the surface.
- Ion plating is often used for applications requiring high wear resistance, such as automotive and aerospace components.
-
Thermal Evaporation
- This method involves heating a material until it evaporates in a vacuum, forming a thin film on the substrate.
- It is particularly useful for creating optical coatings, such as anti-reflective and mirror coatings.
- Thermal evaporation is a cost-effective method for large-scale production.
-
Electron Beam Evaporation
- In this technique, an electron beam is used to heat and vaporize the coating material.
- It is suitable for depositing high-melting-point materials, such as ceramics and metals.
- Electron beam evaporation is widely used in the semiconductor and optical industries.
-
Arc Vapor Deposition
- This method uses an electric arc to vaporize the coating material, which is then deposited onto the substrate.
- It is known for producing dense, high-quality coatings with excellent adhesion.
- Arc vapor deposition is commonly used for tool coatings and wear-resistant applications.
-
Magnetron Sputtering
- A variation of sputtering, magnetron sputtering uses magnetic fields to enhance the ionization of the sputtering gas, increasing deposition rates.
- It is widely used for depositing thin films in electronics, optics, and decorative applications.
-
Applications of Vacuum Coating
- Optical Coatings: Used in lenses, mirrors, and filters to enhance light transmission or reflection.
- Decorative Coatings: Applied to consumer products like jewelry, watches, and home furnishings for aesthetic purposes.
- Wear-Resistant Coatings: Used in industrial and automotive components to improve durability and performance.
- Energy-Saving Coatings: Examples include low-emissivity glass used in energy-efficient windows.
-
Advantages of Vacuum Coating
- High precision and control over coating thickness.
- Ability to deposit a wide range of materials, including metals, ceramics, and polymers.
- Enhanced surface properties, such as hardness, corrosion resistance, and electrical conductivity.
-
Challenges and Considerations
- High initial investment in equipment and infrastructure.
- Requires skilled personnel for operation and maintenance.
- Limited to batch processing in some cases, which may affect production scalability.
In summary, vacuum coating methods such as PVD, CVD, and their variations offer versatile solutions for enhancing the performance and aesthetics of various materials. These techniques are integral to industries ranging from aerospace to consumer electronics, providing durable, high-quality coatings tailored to specific needs.
Summary Table:
Method | Key Features | Applications |
---|---|---|
Physical Vapor Deposition (PVD) | High-purity, durable coatings; includes evaporation and sputtering. | Optical, decorative, wear-resistant coatings. |
Chemical Vapor Deposition (CVD) | Uniform thickness; coats complex geometries. | Hard coatings for engine components, silicon carbide, and diamond-like carbon. |
Ion Plating | Combines PVD and plasma for enhanced adhesion and density. | Automotive and aerospace components requiring high wear resistance. |
Thermal Evaporation | Cost-effective; ideal for optical coatings. | Anti-reflective and mirror coatings. |
Electron Beam Evaporation | Deposits high-melting-point materials. | Semiconductor and optical industries. |
Arc Vapor Deposition | Produces dense, high-quality coatings. | Tool coatings and wear-resistant applications. |
Magnetron Sputtering | Enhanced ionization for higher deposition rates. | Electronics, optics, and decorative applications. |
Ready to elevate your materials with advanced vacuum coating techniques? Contact our experts today to learn more!