Sintering is a critical process in materials science, particularly in the production of ceramics and metals, where powdered materials are heated to form a solid mass without melting. The physical properties of sintered materials are influenced by various factors such as temperature, pressure, particle size, and the composition of the materials. These factors affect the microstructure, porosity, and mechanical properties of the final product. Understanding these properties is essential for optimizing the sintering process to achieve desired material characteristics.
Key Points Explained:
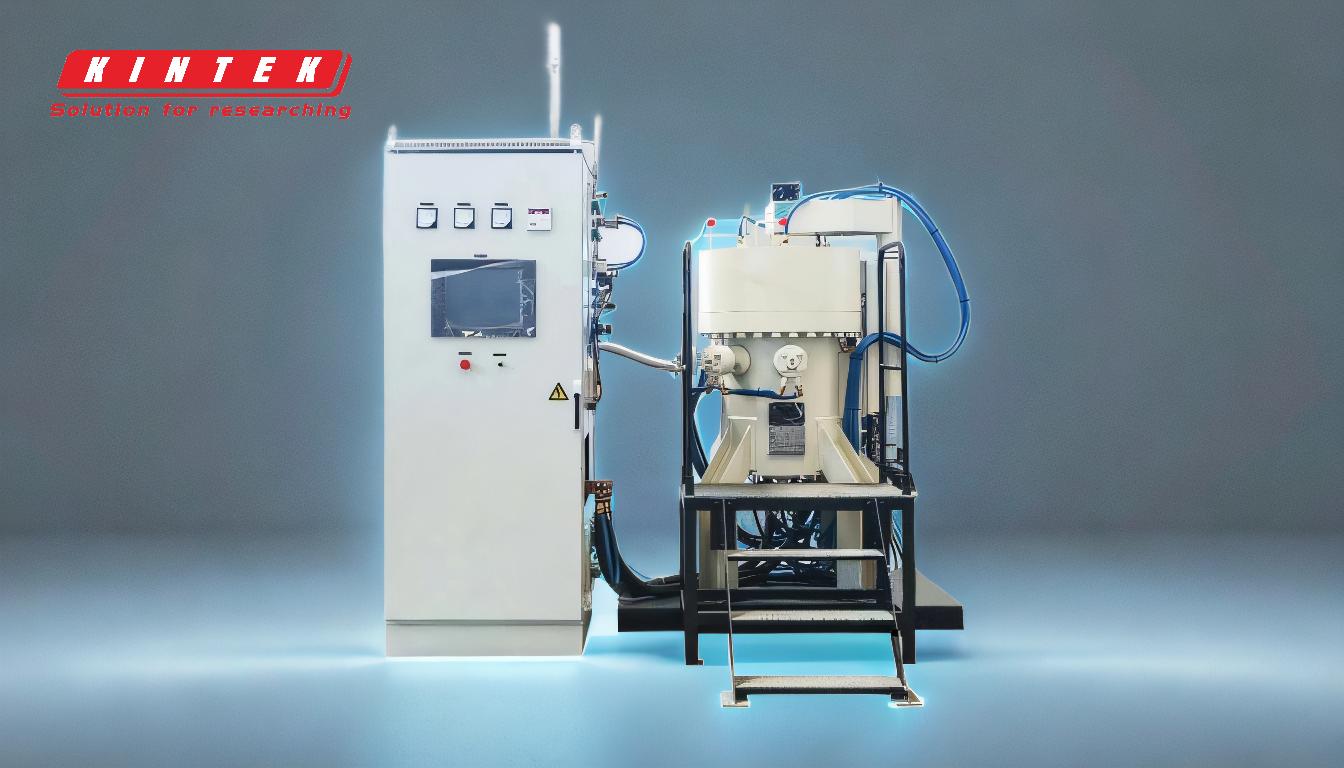
-
Microstructure Composition:
- The microstructure of sintered materials typically includes phases such as hematite, magnetite, and calcium ferrite.
- The evolution of these phases during sintering is influenced by the basicity of the sintering mix, which affects the final product's properties.
-
Influence of Sintering Variables:
- Atmosphere: The sintering atmosphere (air, vacuum, or inert gases like argon/nitrogen) can significantly affect the properties of the sintered material.
- Temperature: Higher sintering temperatures generally increase tensile strength, bending fatigue strength, and impact energy.
- Cooling Rate: The rate at which the sintered material is cooled can also impact its final properties.
-
Techniques and Parameters:
- Different sintering techniques depend on the use of electrical currents, pressure, heat sources, and the specific materials being sintered.
- Parameters such as sintering temperature, applied pressure, average grain size, and gaseous atmosphere are crucial for optimizing the sintering process.
-
Porosity and Densification:
- The final porosity of sintered ceramics is influenced by the initial porosity of the green compact, as well as the temperature and duration of the sintering process.
- Applying pressure during sintering can reduce porosity and sintering time, especially for pure oxide ceramics which require longer sintering times and higher temperatures due to solid-state particle diffusion.
-
Process Control:
- Factors such as air volume, vacuum, layer thickness, speed, and sintering endpoint are controlled during the sintering process.
- For example, the air volume is typically 3200m³ per ton of sintering ore, and the sintering area is calculated as 70-90 m³/(cm²·min).
-
Material Properties:
- The binding area associated with particle size is crucial for determining properties such as strength and conductivity.
- Controllable variables like temperature and initial grain size play a significant role, as vapor pressure is temperature-dependent.
-
Sintering Kinetics:
- Temperature determines the kinetics of sintering and the resulting material properties.
- The heating rate affects densification, with faster heating rates potentially leading to better densification.
-
Particle Size and Composition:
- Smaller particles and homogeneous compositions promote better densification during sintering.
- The composition of the material also impacts sintering behavior, with different materials requiring tailored sintering conditions.
Understanding these key points helps in designing sintering processes that yield materials with desired physical properties, ensuring optimal performance in their intended applications.
Summary Table:
Factor | Impact on Sintered Materials |
---|---|
Temperature | Higher temperatures increase tensile strength, bending fatigue strength, and impact energy. |
Atmosphere | Air, vacuum, or inert gases (argon/nitrogen) influence material properties. |
Cooling Rate | Affects final properties; controlled cooling ensures desired microstructure. |
Particle Size | Smaller particles improve densification and enhance material strength. |
Composition | Homogeneous compositions and tailored conditions optimize sintering behavior. |
Pressure | Reduces porosity and sintering time, especially for oxide ceramics. |
Heating Rate | Faster heating rates can lead to better densification. |
Optimize your sintering process with expert guidance—contact us today!